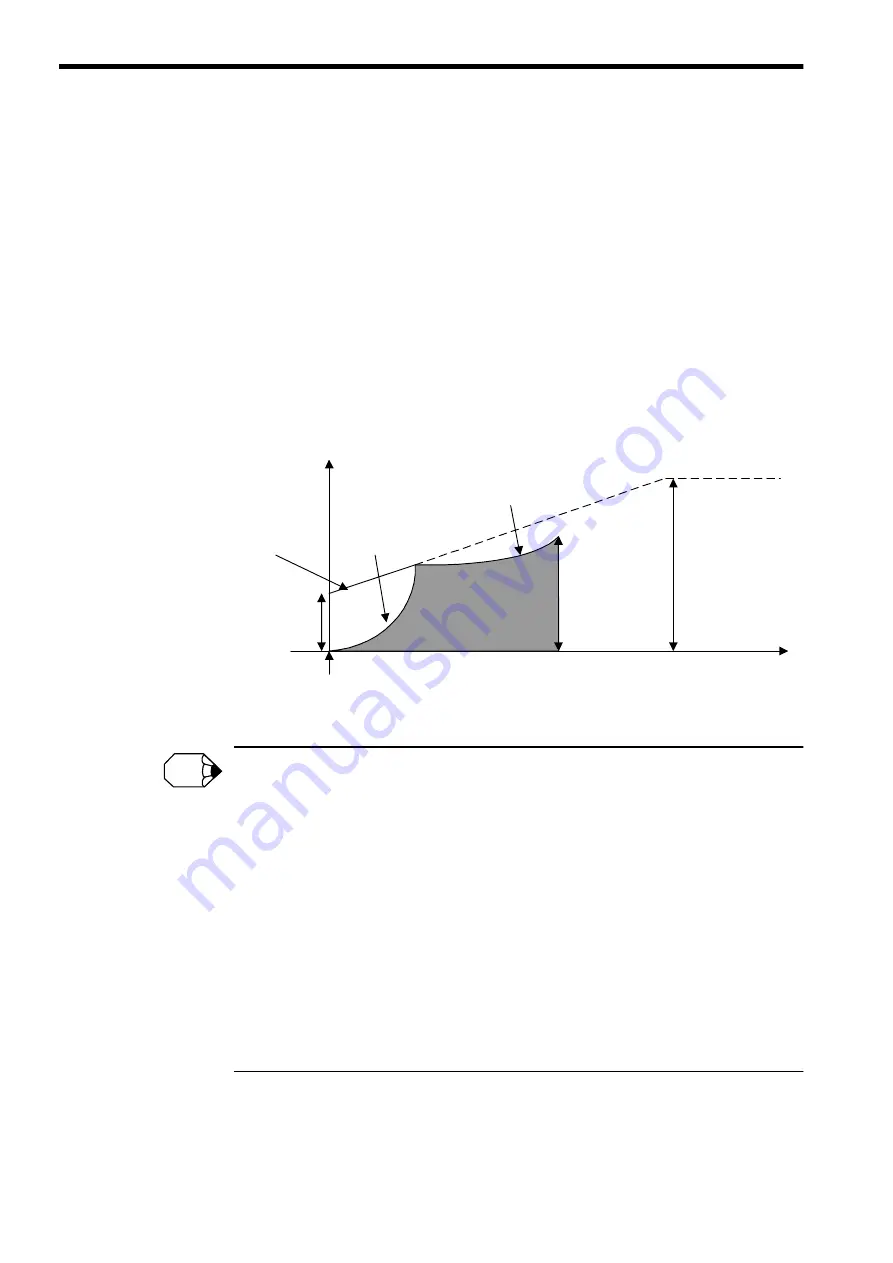
Drive set-up procedure
14.2.5 Quadrant error compensation
14-42
• MD3112 (Pn152) N_LMT_CLAMP_QUAD_ERR_COMP (For each axis)
Meaning:
Quadrant error compensation upper limit value (Positive -> Negative)
Setting value: [0.01%/ms]
• MD3113 (Pn153) TIMING_CONST_QUAD_ERR_COMP (For each axis)
Meaning:
Quadrant error compensation timing constant
Setting value: [0.1/s]
• MD3083 (Pn135) EQUIV_KP_ADJ_PREDICTED_I
Meaning:
1st predictive control equivalent Kp fine adjustment amount (Quadrant
error compensation timing constant when predictive control is used.)
Setting value: [0.1/s]
The following figure shows relations between above-mentioned parameters and compensa-
tion amount waveform.
Fig. 14.1 Functional quadrant error compensation waveform
You can use
quadrant error
compensation 1st-stage gain and
quadrant error
compensation 2nd-stage
gain as replacement parameters of
quadrant error
compensation 1st-stage integration time constant
and
quadrant error
compensation 2nd-stage integration time constant of J300/J100 specification
respectively. However, notice that their setting values are different.
By previous specification, the
quadrant error
compensation n-th stage gain "Kn" was expressed in
(Tin [sec]), while by this specification, the "Kn" is expressed as follows:
Kn [0.00001/s
3
] = Kp x Kv/Tin/10000
Where,
Kp: Position loop gain [1/s]
Kv: Speed loop gain [1/s] (Pay attention that this is not the drive setting unit [Hz].)
Tin: Quadrant error compensation n-th stage integration time constant [sec] (Pay attention
that previous parameter setting value is [0.01 ms].)
Example) When Kp = 40 [1/s], Kv = 300 [1/s], and Tim = 0.5 [ms], Kn [0.00001/s
3
] = 40
×
300/
0.0005/100000 = 240 [0.00001/s
3
]
Quadrant error
compensation 2nd-stage
limit
Quadrant error
compensation
limit offset value
Quadrant error
compensation 1st-
stage gain
Quadrant error
compensation 2nd-
stage gain
Quadrant error compensation timing
constant
Quadrant error
compensation limit
increment value
Time
Compensation
amount
INFO
Summary of Contents for CNC Series
Page 1: ...Maintenance Manual Serviceman Handbook MANUAL No NCSIE SP02 19 Yaskawa Siemens CNC Series...
Page 26: ...Part 1 Hardware...
Page 38: ...System Configuration 1 2 3 Spindle motor designations 1 12...
Page 58: ...Installing the control panels 2 3 5 Installing lightning surge absorbers 2 20...
Page 62: ...Installing the motors 3 4...
Page 84: ...Connection method 4 3 2 Setting the rotary switches on the inverters and servo units 4 22...
Page 96: ...Part 2 Software...
Page 102: ...Software configuration 6 6...
Page 113: ...7 2 Network settings 7 11 8 Click on the radio button to the left of Specify an IP address...
Page 121: ...7 2 Network settings 7 19...
Page 122: ...Part 3 PLC...
Page 154: ...Part 4 Setting up and maintenance...
Page 160: ...Overview of System 10 1 2 Basic operation 10 6...
Page 204: ...How to use Digital Operation 12 2 9 Setting the password setting for write prohibit 12 32...
Page 327: ...Error and Troubleshooting 15 4...
Page 328: ...15 1 Errors without Alarm Display and Troubleshooting 15 5...
Page 329: ...Error and Troubleshooting 15 6...
Page 343: ...Maintenance and Check 16 3 3 Setting up Initializing Absolute encoder 16 14...