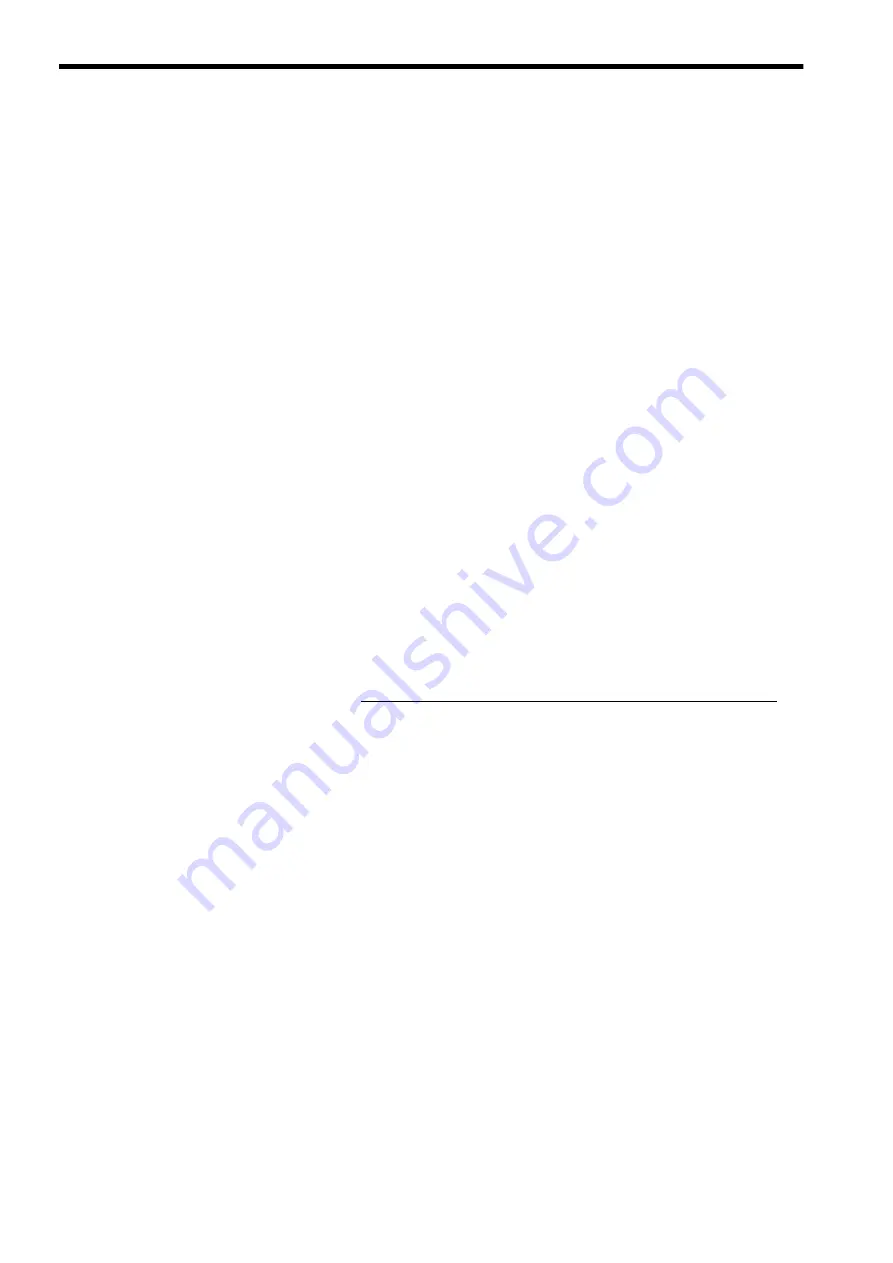
Drive set-up procedure
14.2.1 Position control
14-36
14.2 Servo control
14.2.1 Position control
In DSC, CNC and a drive share the position control, so that CNC also has the position con-
trol-related machine data. The following explains how to set fundamental machine data and
parameters for position control.
CNC setting
• MD10230 SCALING FACTOR_USER_DEF [9] (For all axes in common) ##
Meaning:
Position loop gain setting unit
Setting value: 1.0 [1/s]
With this setting, the unit of position loop gain MD32200 becomes [1/s].
Note: If 16.66666667 has been assigned, the setting unit of MD32200
(position loop gain) is [m/min/mm].
• MD32200 POSCTRL_GAIN [0] (For each units)
Meaning:
Position loop gain
Setting value: [1/s] (The unit defined by MD10230 becomes the unit of the position
loop gain.)
• MD36400 CONTOR_TOL (For each axis)
Meaning:
Maximum deviation [Command unit (mm, deg, and others)]
Setting value: To be set to the following value.
Drive setting
Servo drive
• MD3000 digit 1 (Pn000 digit 1) FUNCTION_SWITCH_BASIC (For each axis) ##
Meaning:
Position control is enabled/disabled.
Setting value: 0 --- Position control is disabled.
1 --- Position control is enabled.
7 --- Position control and speed control are switched over.
Must be set to "7".
• MD3032 (Pn102) KP (For each axis)
Meaning:
Position loop gain
Setting value: [0.1/s]
This value is not used for DSC control, but used internally for calculating
gain and others of the quadrant error compensation function. Set this
parameter to a value of MD32200 at CNC, paying attention to the setting
unit.
Maximum feed speed [Command unit (mm, deg, and others)]
×
1.2
Position loop gain [1/s]
×
60
Summary of Contents for CNC Series
Page 1: ...Maintenance Manual Serviceman Handbook MANUAL No NCSIE SP02 19 Yaskawa Siemens CNC Series...
Page 26: ...Part 1 Hardware...
Page 38: ...System Configuration 1 2 3 Spindle motor designations 1 12...
Page 58: ...Installing the control panels 2 3 5 Installing lightning surge absorbers 2 20...
Page 62: ...Installing the motors 3 4...
Page 84: ...Connection method 4 3 2 Setting the rotary switches on the inverters and servo units 4 22...
Page 96: ...Part 2 Software...
Page 102: ...Software configuration 6 6...
Page 113: ...7 2 Network settings 7 11 8 Click on the radio button to the left of Specify an IP address...
Page 121: ...7 2 Network settings 7 19...
Page 122: ...Part 3 PLC...
Page 154: ...Part 4 Setting up and maintenance...
Page 160: ...Overview of System 10 1 2 Basic operation 10 6...
Page 204: ...How to use Digital Operation 12 2 9 Setting the password setting for write prohibit 12 32...
Page 327: ...Error and Troubleshooting 15 4...
Page 328: ...15 1 Errors without Alarm Display and Troubleshooting 15 5...
Page 329: ...Error and Troubleshooting 15 6...
Page 343: ...Maintenance and Check 16 3 3 Setting up Initializing Absolute encoder 16 14...