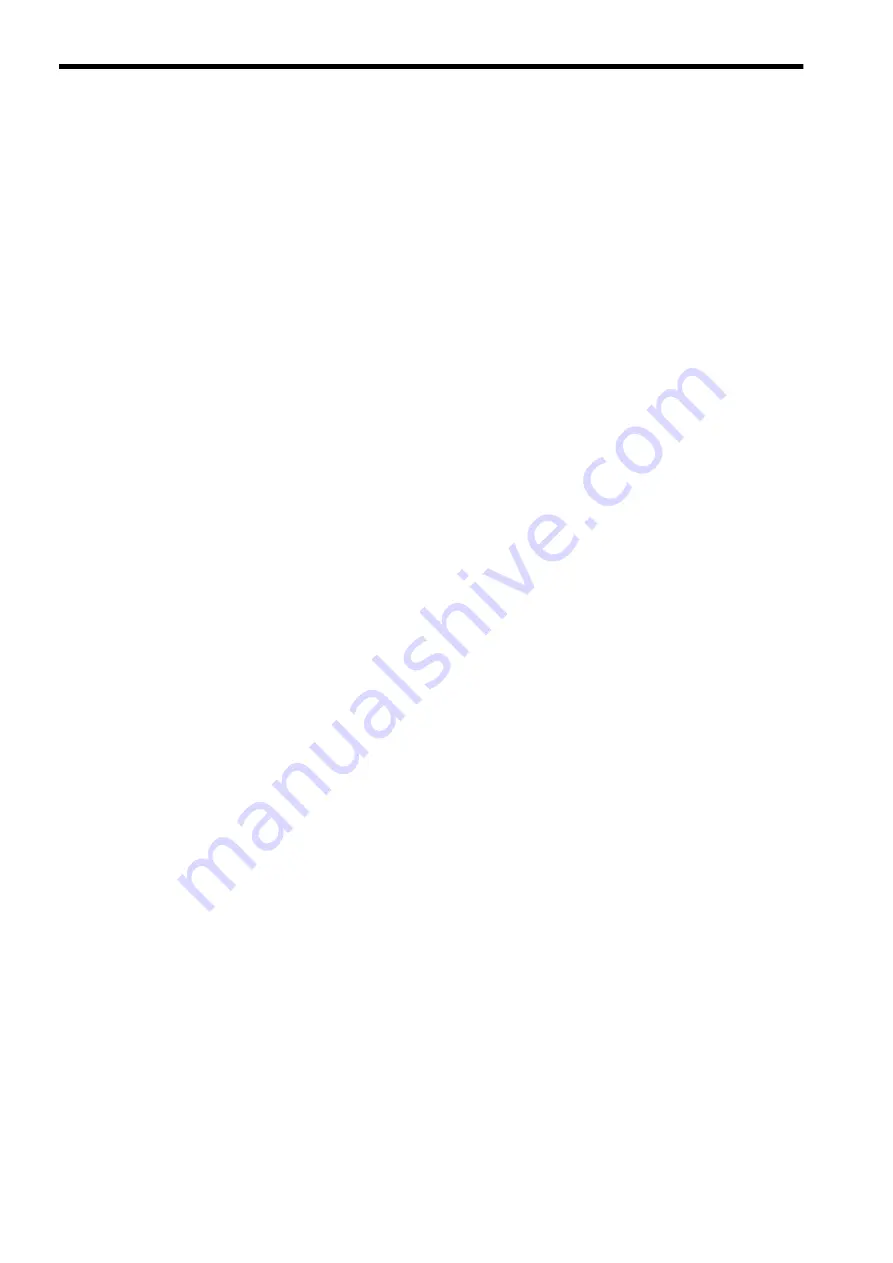
Drive set-up procedure
14.3.8 Torque Control and Fixed Stop Function
14-76
Spindle drive
• MD6423 (Cn423) TORQUE_LIMIT_SELECT (For each axis)
Meaning:
Variable torque limit selection
Torque limit command from CNC is enabled.
Setting value: 0---disabled
1---enabled
Note: You must specify "1".
For Fixed Stop function, the tail stock press control, for example, is processed on the follow-
ing steps.
1. With CNC program command, the feed axes moves toward the object and simulta-
neously the torque control is enabled.
• CNC programming: G01X100. FXS [X] = 1
• CNC sends the torque control value set with the machine data MD37010 or FXST
command.
2. The feed axis contacts the object and then the torque and the amount of deviation
increase.
3. Drive torque reference is cramped at the limiting value. The amount of deviation
increases further.
4. When the increment of position deviation from steady state of Step 1 reaches the setting
value with the machine data MD37030,
• the drive is switched over to the speed control state and the torque is maintained with
the torque control. (Speed reference is internally output. Position deviation = 0.
• CNC program transfers to the nest block.
In this way, the torque control state is enabled with the torque control.
5. When FXS[X] = 0 command is output,
• the drive returns to the steady state.
In this way, Fixed Stop function is disabled and the normal position control state is
recovered. The pressing is released with the reverse procedure of Step 1.
Summary of Contents for CNC Series
Page 1: ...Maintenance Manual Serviceman Handbook MANUAL No NCSIE SP02 19 Yaskawa Siemens CNC Series...
Page 26: ...Part 1 Hardware...
Page 38: ...System Configuration 1 2 3 Spindle motor designations 1 12...
Page 58: ...Installing the control panels 2 3 5 Installing lightning surge absorbers 2 20...
Page 62: ...Installing the motors 3 4...
Page 84: ...Connection method 4 3 2 Setting the rotary switches on the inverters and servo units 4 22...
Page 96: ...Part 2 Software...
Page 102: ...Software configuration 6 6...
Page 113: ...7 2 Network settings 7 11 8 Click on the radio button to the left of Specify an IP address...
Page 121: ...7 2 Network settings 7 19...
Page 122: ...Part 3 PLC...
Page 154: ...Part 4 Setting up and maintenance...
Page 160: ...Overview of System 10 1 2 Basic operation 10 6...
Page 204: ...How to use Digital Operation 12 2 9 Setting the password setting for write prohibit 12 32...
Page 327: ...Error and Troubleshooting 15 4...
Page 328: ...15 1 Errors without Alarm Display and Troubleshooting 15 5...
Page 329: ...Error and Troubleshooting 15 6...
Page 343: ...Maintenance and Check 16 3 3 Setting up Initializing Absolute encoder 16 14...