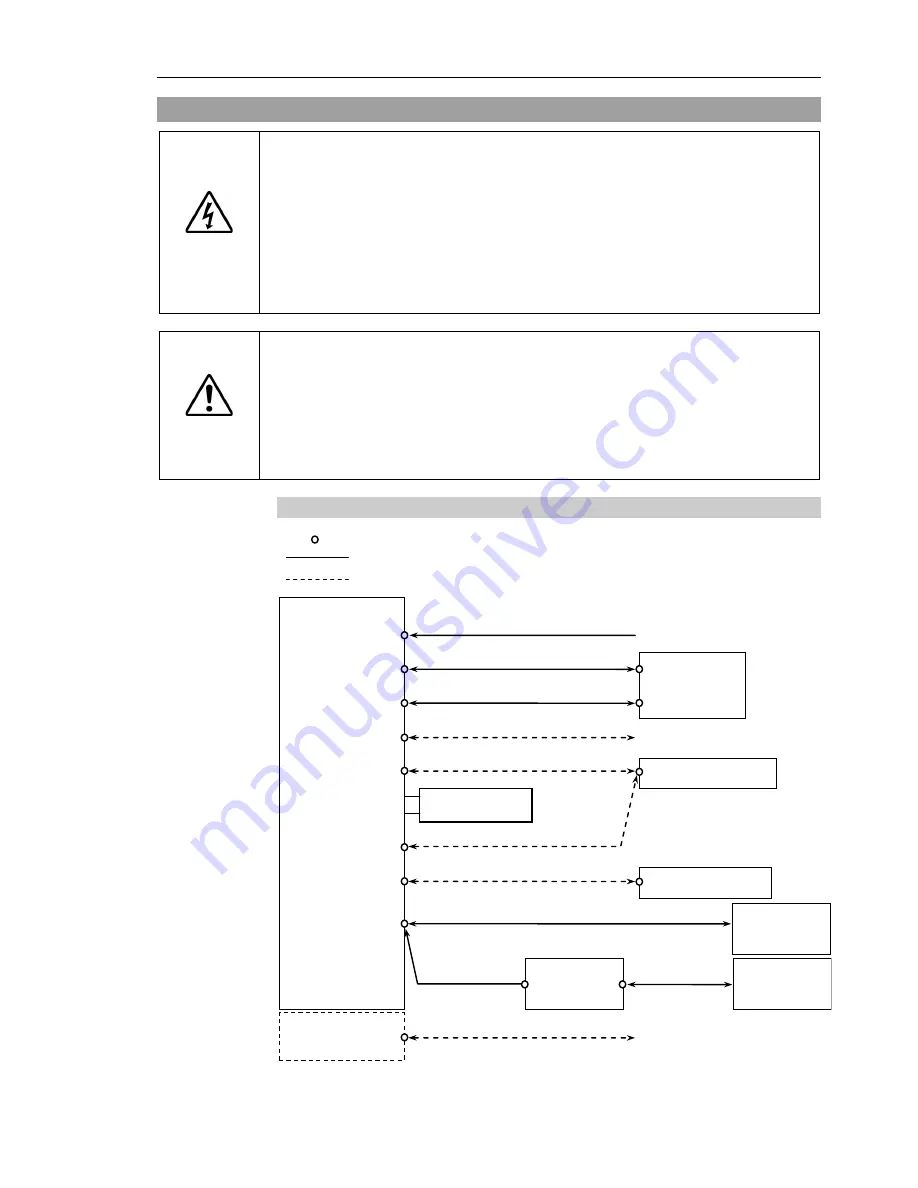
Setup & Operation 3. Installation
RC180 Rev.17
27
3.4 Cable Connection
WARNING
■ Make sure that the power to the Controller is turned OFF and the power plug is
disconnected before connecting or disconnecting any cables. Connecting or
disconnecting any cables with the power ON is extremely hazardous and may
result in electric shock and malfunction of the Controller.
■ Be sure to connect the cables properly. Do not allow unnecessary strain on the
cables. (Do not put heavy objects on the cables. Do not bend or pull the cables
forcibly.) The unnecessary strain on the cables may result in damage to the
cables, disconnection, and/or contact failure. Damaged cables, disconnection,
or contact failure is extremely hazardous and may result in electric shock and/or
improper function of the system.
CAUTION
■ The serial number of the Manipulator that should be connected is indicated on the
Connection Check Label on the Controller. Connect the Controller and the
Manipulator correctly. Improper connection between the Controller and the
Manipulator may cause not only improper function of the robot system but also
safety problems.
■ Before connecting the connector, make sure that the pins are not bent.
Connecting with the pins bent may damage the connector and result in
malfunction of the robot system.
3.4.1 Typical Cable Connection
Manipulator
(6) USB Memory
PC for Development
Input/Output Device
Connect by (5) or (7)
Controller
(1) AC Power Terminal Block
(2) M/C Power Cable
(3) M/C Signal Cable
(4) EMERGENCY
(5) PC for Development
200-240VAC
(7) LAN (Ethernet
Communication)
(8) I/O Connector
(9) TP Cable B
Emergency Stop
Safety Door, etc.
Operator
Panel
(10) OP Cable
(9) TP Cable A
Teach
Pendant
Teach
Pendant
Option Unit
Disconnectable connector
Cable attached at delivery
Cable prepared by users
FieldBus
Expansion I/O
RS-232C
*1
Summary of Contents for RC180
Page 1: ...Rev 17 EM164C3205F ROBOT CONTROLLER RC180 ...
Page 2: ...ROBOT CONTROLLER RC180 Rev 17 ...
Page 13: ...Safety This section contains information for safety of the Robot System ...
Page 14: ......
Page 20: ......
Page 124: ...Setup Operation 12 Option Units 112 RC180 Rev 17 ...
Page 125: ...Maintenance This section contains maintenance procedures for the Robot Controller ...
Page 126: ...114 ...