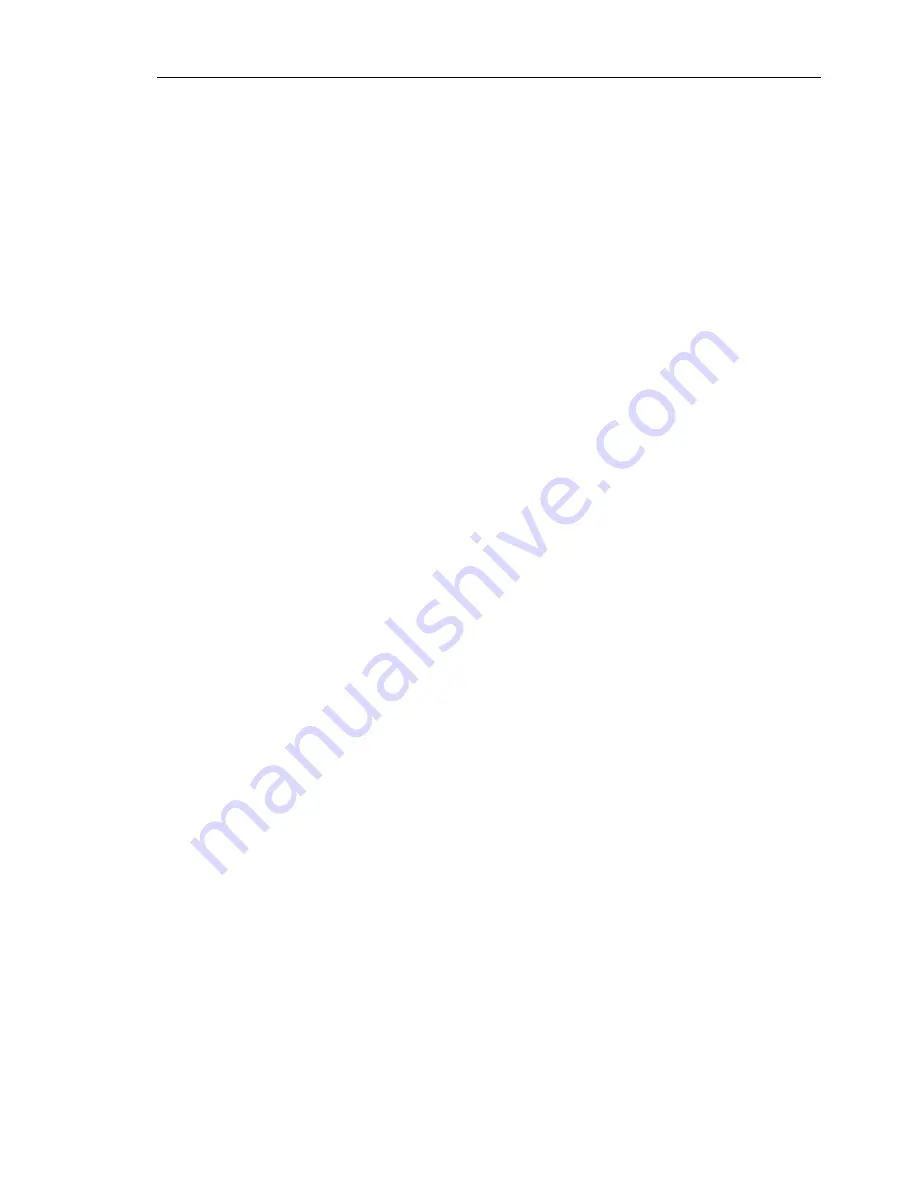
Setup & Operation 2. Part Names and Functions
RC180 Rev.17
19
Low Power Mode
The motor power is reduced in this mode.
Executing a power status change instruction will change to the restricted (low power)
status regardless of conditions of the safety door or operation mode. The restricted
(low power) status ensures the safety of the operator and reduces the possibility of
peripheral equipment destruction or damage caused by careless operation.
Dynamic Brake
The dynamic brake circuit includes relays that short the motor armatures. The dynamic
brake circuit is activated when there is an Emergency Stop input or when any of the
following errors is detected: encoder cable disconnection, motor overload, irregular
motor torque, motor speed error, servo error (positioning or speed overflow), irregular
CPU, memory check-sum error and overheat condition inside the Motor Driver Module.
Encoder Cable Disconnection Error Detection
The dynamic brake circuit is activated when the Motor Encoder Signal cable is
disconnected.
Motor Overload Detection
The dynamic brake circuit is activated when the system detects that the load on the
motor has exceeded its capacity.
Irregular Motor Torque (out-of-control manipulator) Detection
The dynamic brake circuit is activated when irregularity with motor torque (motor
output) is detected (in which case the Manipulator is out of control).
Motor Speed Error Detection
The dynamic brake circuit is activated when the system detects that the motor is running
at incorrect speed.
Positioning Overflow –Servo Error- Detection
The dynamic brake circuit is activated when the system detects that the difference
between the Manipulator’s actual position and commanded position exceeds the margin
of error allowed.
Speed Overflow –Servo Error- Detection
The dynamic brake circuit is activated when the Manipulator’s actual speed is detected
to mark an overflow (the actual speed is outside the nominal range) error.
CPU Irregularity Detection
Irregularity of CPU that controls the motor is detected by the watchdog timer. The
system CPU and the motor controlling CPU inside the Controller are also designed to
constantly check each other for any discrepancies. If a discrepancy is detected, the
dynamic brake circuit is activated.
Memory Check-sum Error Detection
The dynamic brake circuit is activated when a memory check-sum error is detected.
Summary of Contents for RC180
Page 1: ...Rev 17 EM164C3205F ROBOT CONTROLLER RC180 ...
Page 2: ...ROBOT CONTROLLER RC180 Rev 17 ...
Page 13: ...Safety This section contains information for safety of the Robot System ...
Page 14: ......
Page 20: ......
Page 124: ...Setup Operation 12 Option Units 112 RC180 Rev 17 ...
Page 125: ...Maintenance This section contains maintenance procedures for the Robot Controller ...
Page 126: ...114 ...