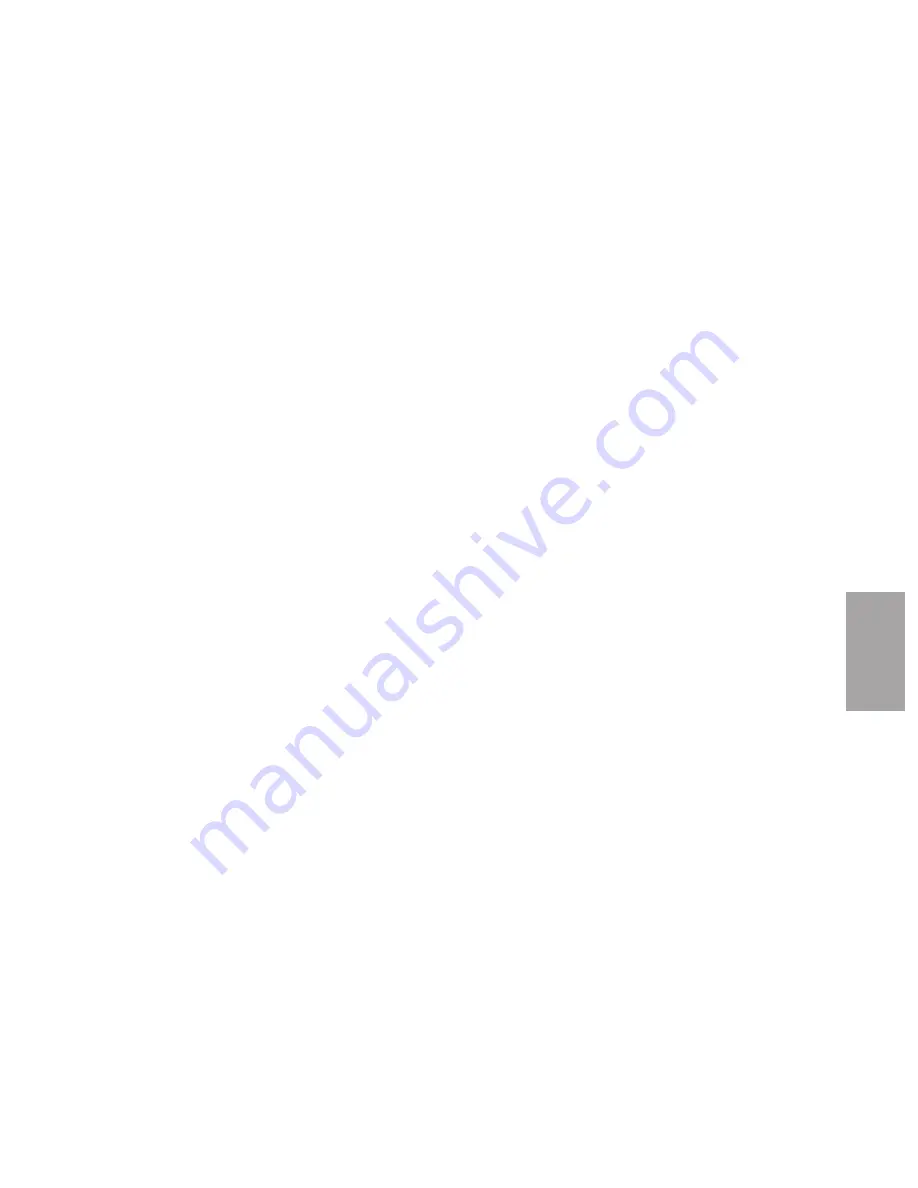
4
O
p
er
at
io
n
O p e r a t i o n l
4-105
Using the OptiMizer™
(continued)
•
Pre-dry Airflow Flow (CFM)
– This airflow setpoint is used when the Process
Air VSD is in the PID Control (automatic) mode. PID control means that the
controller adjusts the actual VSD output percentage in order to keep the airflow
at the specific CFM recipe setpoint. The controller will take the output % of
the VSD to the maximum or minimum range to achieve the setpoint. However,
if a setpoint is used that can not be achieved, the system will stay at the maxi-
mum or minimum range during Pre-dry operation. The recommended starting
point for this setpoint is 90% of the maximum airflow as shown on the
‘OptiMizer™ Max Airflow Setup’ HMI screen detailed above.
•
Pre-dry Temperature (°F)
– This temperature setpoint is for the process deliv-
ery air for the dryer. The setpoint for this temperature needs to be set above the
desired Material Target Temperature and at or below the manufacturer’s tem-
perature maximum limit for the resin being used or 375 °F (maximum recipe
setpoint) whichever is lower. The recommended setpoint for this temperature is
the midpoint between the Material Temperature Target setpoint and the manu-
facturer’s temperature maximum or recipe limit.
•
Cool Down Temperature (°F)
– Cool Down temperature is used when the
temperature method of Cool Down is selected. The user will select a DMII
temperature probe (T1-T6) to use for Cool Down. When the system Cool
Down is activated or the Auto Cool Down is enabled and the system is shut-
down and the temperature of that probe falls below the Cool Down temperature
setpoint, the process blower shuts down and the regeneration system begins its
shutdown sequence.
•
Material Target Temperature (°F)
– This temperature setpoint is for the
material at the IMM or extruder machine throat as measured by the Conair
Material Temperature RTD. The main goal of the OptiMizer™ operation is to
keep the material temperature at this setpoint using the least amount of energy
as possible. This temperature is usually determined by the material and extrud-
ing or molding machinery being used.
•
Material Maximum Temperature (°F)
– This temperature setpoint is for the
material at the IMM or extruder machine throat as measured by the Conair
Material Temperature RTD. The OptiMizer™ uses this value for the upper
limit of the Material Temperature setpoint to ensure that the material tempera-
ture does not exceed the temperature rating of the material.
•
Optimized
– For an initial or new recipe, this should be set to 0 (OFF). This
means that the recipe is a non-Optimized recipe and the system will take the
necessary steps to achieve an Optimized state. When that state has been
achieved and the system displays the Optimized message, the Dynamic set-
points in the recipe can be changed and this setting can be changed
to 1 (ON).
(continued)
Содержание HTC 120
Страница 10: ...viii l Table of Contents ...
Страница 30: ...2 14 l Description ...
Страница 35: ...Installation General Installation General l 3 5 3 I n s t a l l a t i o n ...
Страница 65: ...Installation Hard Piping Kits Installation Piping Hoses l 3 35 3 I n s t a l l a t i o n ...
Страница 80: ...3 50 l Installation Piping Hoses ...
Страница 81: ...3 I n s t a l l a t i o n Installation Main Power Connections Installation Main Power Connections l 3 51 ...
Страница 88: ...3 58 l Installation Piping Hoses ...
Страница 89: ...3 I n s t a l l a t i o n Installation Main Power Connections l 3 59 Installation Conveying Lines ...
Страница 92: ...3 62 l Installation Conveying Lines ...
Страница 93: ...Installation Water Lines 3 I n s t a l l a t i o n Installation Water Lines l 3 63 ...
Страница 115: ...Installation Compressed Air Lines 3 I n s t a l l a t i o n Installation Compressed Air Lines l 3 85 ...
Страница 124: ...3 94 l Installation Gas Piping and Exhaust Flue ...
Страница 125: ...Installation Testing 3 I n s t a l l a t i o n Installation Testing l 3 95 ...
Страница 149: ...4 O p e r a t i o n Operation l 4 7 Control Function Flow Charts continued Operation Flow Chart 1 1A 2 3 4 continued 5 ...
Страница 152: ...Control Function Flow Charts continued Setup Flow Chart 1 1B 19 38 20 34 37 4 10 l Operation continued ...
Страница 250: ...4 108 l Operation ...
Страница 286: ...5 36 l Maintenance ...