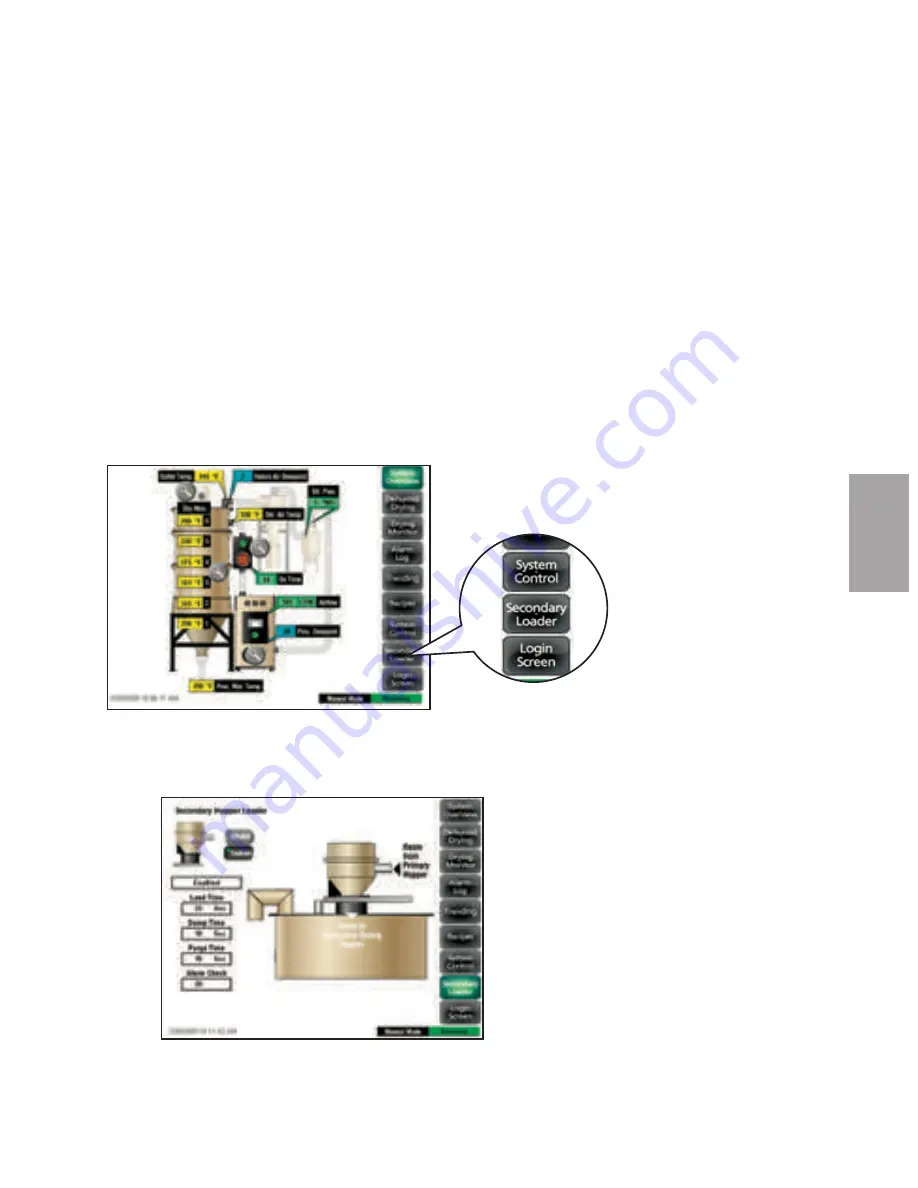
3
In
st
al
la
tio
n
I n s t a l l a t i o n - Te s t i n g l
3-107
Testing the Secondar y Receiver
(optional)
1
Make sure there is no material in the secondary hopper.
2
Disconnect the material supply hose of the receiver at the source.
(Bottom
of primary hopper)
3
Login to the EnergySmart Dryer control under the appropriate user name
and password.
See Operation section entitled, Control Function Descriptions,
Screen 1A-Login Screen.
4
Navigate to the System Overview Screen (Screen 6).
5
Press the “Secondary Loader” button to access the Secondary Loader
Screen (Screen 18).
(continued)
NOTE:
Secondary loader must
have been enabled in setup.
✐
Содержание HTC 120
Страница 10: ...viii l Table of Contents ...
Страница 30: ...2 14 l Description ...
Страница 35: ...Installation General Installation General l 3 5 3 I n s t a l l a t i o n ...
Страница 65: ...Installation Hard Piping Kits Installation Piping Hoses l 3 35 3 I n s t a l l a t i o n ...
Страница 80: ...3 50 l Installation Piping Hoses ...
Страница 81: ...3 I n s t a l l a t i o n Installation Main Power Connections Installation Main Power Connections l 3 51 ...
Страница 88: ...3 58 l Installation Piping Hoses ...
Страница 89: ...3 I n s t a l l a t i o n Installation Main Power Connections l 3 59 Installation Conveying Lines ...
Страница 92: ...3 62 l Installation Conveying Lines ...
Страница 93: ...Installation Water Lines 3 I n s t a l l a t i o n Installation Water Lines l 3 63 ...
Страница 115: ...Installation Compressed Air Lines 3 I n s t a l l a t i o n Installation Compressed Air Lines l 3 85 ...
Страница 124: ...3 94 l Installation Gas Piping and Exhaust Flue ...
Страница 125: ...Installation Testing 3 I n s t a l l a t i o n Installation Testing l 3 95 ...
Страница 149: ...4 O p e r a t i o n Operation l 4 7 Control Function Flow Charts continued Operation Flow Chart 1 1A 2 3 4 continued 5 ...
Страница 152: ...Control Function Flow Charts continued Setup Flow Chart 1 1B 19 38 20 34 37 4 10 l Operation continued ...
Страница 250: ...4 108 l Operation ...
Страница 286: ...5 36 l Maintenance ...