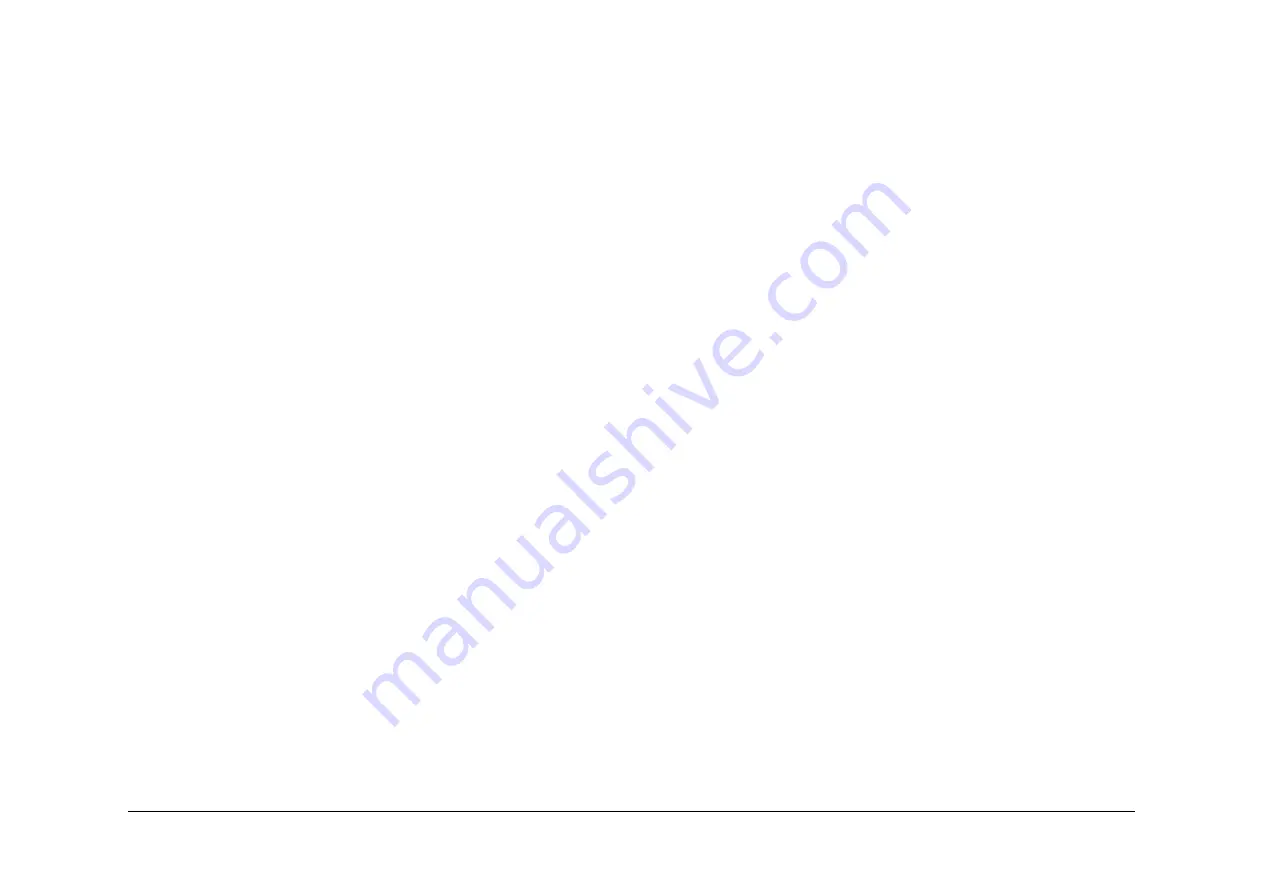
May 2013
2-594
Xerox® WorkCentre® 5790 Family
OF1
Status Indicator RAPs
•
A mooing, grunting or moaning noise at the machine cycle down/end of run cycle.
Cause:
–
The noise occurs when the drum moves slowly under the cleaning blade as the
drives come to a stop.
–
The environment (temperature, humidity, type of media, print density, etc.) will also
effect the coefficient of friction between the cleaning blade and the drum, directly
effecting the noise.
Solution:
–
Dusting the drum with Kynar or zinc stearate will quiet the noise temporarily, but as
these lubricants wear off the noise will return.
–
A new xerographic module,
PL 9.20 Item 2
(40-90 ppm) or
PL 9.22 Item 2
(35 ppm)
may be less noisy than the xerographic module currently in the machine, at a noise
sensitive customer’s site this may provide a solution, but the old xerographic module
should be kept for use in a more noise tolerant environment.
Fuser
Possible causes and potential solutions are:
•
Grinding noise.
Possible causes are:
–
The fuser web motor not turning the fuser web, causing excessive loading on the
fuser drives. This will also cause toner contamination on the stripper fingers and
paper jams in the inverter.
–
The fuser web drive dog, 35-55 ppm
PL 10.8 Item 2
or 65-90 ppm
PL 10.10 Item 2
.
Solution:
–
Go to
10A
Fuser Web Motor RAP.
NOTE: Do not change the fuser module, because of the appearance of wrinkles on
the pressure roll. This is normal for the pressure roll, caused by the conductive
sleeve that stretches as the silicon rubber base of the roll expands. The pressure
rolls are more wrinkled due to the higher run temperatures on the 65-90 ppm
machines.
1K LCSS
Run the following components:
•
Enter
dC330
code 11-000 Transport Motor 1, to run the entry transport rolls,
PL 11.110
Item 2
and
PL 11.110 Item 9
,
PL 11.110 Item 6
.
•
Enter
dC330
code 11-001 Transport Motor 2, to run the entry rolls,
PL 11.120 Item 13
.
•
Enter
dC330
code 11-024 Paddle Wheel Motor Run, rotates the paddle wheel,
PL 11.104
Item 4
.
•
Enter
dC330
code 11-009 Tamp Mot Cycle, cycles the front and rear tampers,
PL 11.112
Item 1
.
•
Enter
dC330
code 11-023 Eject Mot Cycle, cycles the eject assembly,
PL 11.114 Item 1
.
•
Enter
dC330
code 11-033 Bin 1 Elevator Motor Cycle, to move bin 1 up and down,
PL
11.106 Item 8
.
NOTE: . The bin will move down and then move up to the home position.
Possible causes and potential solutions are:
•
2 knocks for each stapled set.
Possible causes are:
–
LCSS set ejector.
Solution:
–
Go to the
11-320-120, 11-322-120
Ejector Movement Failure RAP.
•
Clicking Noise from the LCSS.
Possible causes are:
–
The staple head continually operating for approximately 15 seconds. This occurs
every time the LCSS top cover or front door is opened then closed, because the sta-
pler is attempting to prime the staple head, by indexing the staple stick forward and
pre-forming two staples.
Solution:
–
Check the staple cartridge for jammed staples and remove any that are found.
–
Ensure the staple cartridge is fully seated.
–
Ensure that the correct staple cartridge is installed.
–
Perform
11-364-120
Stapling Failure RAP.
2K LCSS
Run the following components:
•
Enter
dC330
code 11-000 Transport Motor 1, to run the entry transport rolls,
PL 11.14
Item 6
.
•
Enter
dC330
code 11-001 Transport Motor 2, to run the entry rolls,
PL 11.22 Item 5
.
•
Enter
dC330
code 11-024 Paddle wheel Motor run, rotates the paddle wheel,
PL 11.8
Item 4
.
•
Enter
dC330
code 11-009 Tamp Mot Cycle, cycles the front and rear tampers,
PL 11.16
Item 1
.
•
Enter
dC330
code 11-023 Eject Mot Cycle, cycles the eject assembly,
PL 11.18 Item 1
.
•
Enter
dC330
code 11-033 Bin 1 Elevator Motor Cycle, to move bin 1 up and down,
PL
11.10 Item 8
.
NOTE: The bin will move down and then move up to the home position.
•
Enter
dC330
code 11-043 Punch Head run, rotates the punch head,
PL 11.6 Item 3
.
•
Enter
dC330
code 11-055 SU1 index Mot Cycle, cycles the stapler from the front to the
rear,
PL 11.20 Item 5
.
Possible causes and potential solutions are:
•
2 knocks for each stapled set.
Solution:
–
Go to the
11-320-110, 11-322-110
Ejector Movement Failure RAP.
•
Noise from the right hand side of the machine.
Possible causes are:
–
The LCSS is not aligned correctly.
Solution:
–
Check the machine to LCSS alignment,
ADJ 11.2-110
.
–
Adjust the components if appropriate.
–
Install new parts as necessary.
Summary of Contents for WorkCentre 5790 Series
Page 1: ...Xerox WorkCentre 5790 Family Service Manual 708P90298 May 2013 ...
Page 4: ...May 2013 ii Xerox WorkCentre 5790 Family Introduction ...
Page 20: ...May 2013 xviii Xerox WorkCentre 5790 Family Translation of Warnings Introduction ...
Page 22: ...May 2013 1 2 Xerox WorkCentre 5790 Family Service Call Procedures ...
Page 32: ...May 2013 1 12 Xerox WorkCentre 5790 Family SCP 7 Service Call Procedures ...
Page 53: ...May 2013 2 21 Xerox WorkCentre 5790 Family 01B Status Indicator RAPs Figure 1 3 3V Return ...
Page 54: ...May 2013 2 22 Xerox WorkCentre 5790 Family 01B Status Indicator RAPs Figure 2 3 3V Return ...
Page 56: ...May 2013 2 24 Xerox WorkCentre 5790 Family 01B Status Indicator RAPs Figure 3 5V Return ...
Page 57: ...May 2013 2 25 Xerox WorkCentre 5790 Family 01B Status Indicator RAPs Figure 4 5V Return ...
Page 59: ...May 2013 2 27 Xerox WorkCentre 5790 Family 01B Status Indicator RAPs Figure 5 12V Return ...
Page 61: ...May 2013 2 29 Xerox WorkCentre 5790 Family 01B Status Indicator RAPs Figure 6 24V Return ...
Page 62: ...May 2013 2 30 Xerox WorkCentre 5790 Family 01B Status Indicator RAPs Figure 7 24V Return ...
Page 63: ...May 2013 2 31 Xerox WorkCentre 5790 Family 01B Status Indicator RAPs Figure 8 24V Return ...
Page 95: ...May 2013 2 63 Xerox WorkCentre 5790 Family 01K Status Indicator RAPs Figure 2 Circuit diagram ...
Page 96: ...May 2013 2 64 Xerox WorkCentre 5790 Family 01K Status Indicator RAPs ...
Page 178: ...May 2013 2 146 Xerox WorkCentre 5790 Family 06 350 Status Indicator RAPs ...
Page 592: ...May 2013 2 560 Xerox WorkCentre 5790 Family 16B 16C Status Indicator RAPs ...
Page 596: ...May 2013 2 564 Xerox WorkCentre 5790 Family 19 409 Status Indicator RAPs ...
Page 698: ...May 2013 3 2 Xerox WorkCentre 5790 Family Image Quality ...
Page 736: ...May 2013 3 40 Xerox WorkCentre 5790 Family IQS 8 Image Quality ...
Page 742: ...May 2013 4 6 Xerox WorkCentre 5790 Family Repairs Adjustments ...
Page 772: ...May 2013 4 34 Xerox WorkCentre 5790 Family REP 3 4 Repairs Adjustments ...
Page 938: ...May 2013 4 200 Xerox WorkCentre 5790 Family REP 9 10 Repairs Adjustments ...
Page 994: ...May 2013 4 256 Xerox WorkCentre 5790 Family REP 11 17 110 Repairs Adjustments ...
Page 1014: ...May 2013 4 276 Xerox WorkCentre 5790 Family REP 11 15 120 Repairs Adjustments ...
Page 1166: ...May 2013 4 428 Xerox WorkCentre 5790 Family REP 14 20 Repairs Adjustments ...
Page 1168: ...May 2013 4 430 Xerox WorkCentre 5790 Family ADJ 3 1 ADJ 3 2 Repairs Adjustments ...
Page 1174: ...May 2013 4 436 Xerox WorkCentre 5790 Family ADJ 4 1 Repairs Adjustments ...
Page 1242: ...May 2013 4 504 Xerox WorkCentre 5790 Family ADJ 14 1 ADJ 14 2 Repairs Adjustments ...
Page 1386: ...May 2013 6 2 Xerox WorkCentre 5790 Family General Procedures Information ...
Page 1524: ...May 2013 6 140 Xerox WorkCentre 5790 Family Fax Tags General Procedures Information ...
Page 1526: ...May 2013 7 2 Xerox WorkCentre 5790 Family Wiring Data ...
Page 1554: ...May 2013 7 30 Xerox WorkCentre 5790 Family PJ Locations Wiring Data ...
Page 1604: ...May 2013 8 2 Xerox WorkCentre 5790 Family Accessories ...
Page 1606: ...May 2013 8 4 Xerox WorkCentre 5790 Family ACC 1 Accessories ...
Page 1610: ...XEROX EUROPE ...