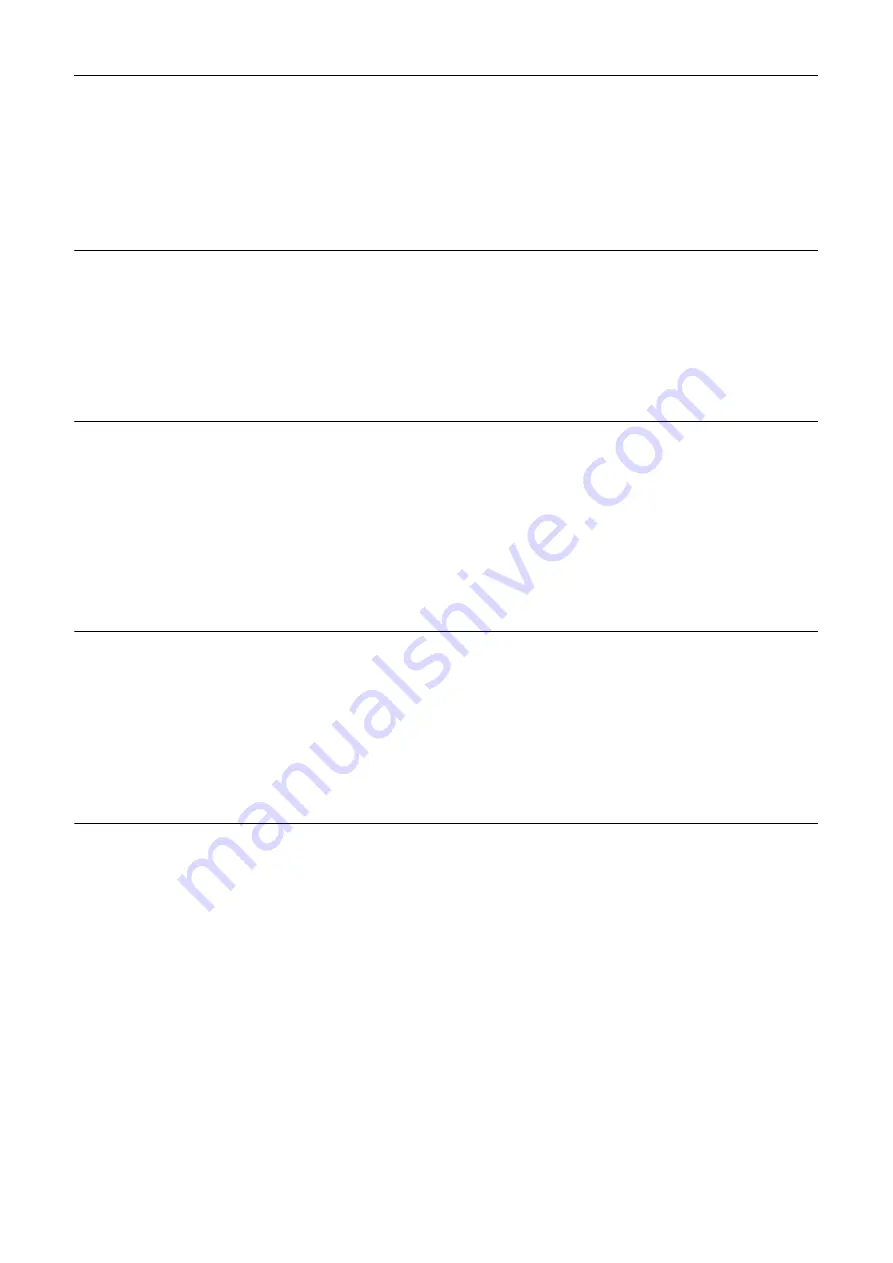
SINAMICS G120D
List Manual (LH14), 01/2016, A5E33842313
869
4 Faults and alarms
4.2 List of faults and alarms
Alarm value (r2124, interpret decimal):
1:
The upper output limit in p2291 is set lower than the lower output limit in p2292.
Remedy:
For alarm value = 1:
Set the output limit in p2291 higher than in p2292.
See also: p2291 (Technology controller maximum limiting), p2292 (Technology controller minimum limiting)
F07435 (N)
Drive: Setting the ramp-function generator for sensorless vector control
Message class:
Application/technological function faulted (17)
Reaction:
OFF2 (IASC/DCBRK, NONE, OFF1, OFF3)
Acknowledge:
IMMEDIATELY
Cause:
During operation with sensorless vector control (r1407.1) the ramp-function generator was stopped (p1141). An
internal setting command of the ramp-function generator output caused the set setpoint speed to be frozen.
Remedy:
- de-activate the holding command for the ramp-function generator (p1141).
- suppress the fault (p2101, p2119). This is necessary if the ramp-function generator is held using jogging and the
speed setpoint is simultaneously inhibited (r0898.6).
A07440
EPOS: Jerk time is limited
Message class:
Error in the parameterization / configuration / commissioning procedure (18)
Reaction:
NONE
Acknowledge:
NONE
Cause:
The calculation of the jerk time Tr = max(p2572, p2573) / p2574 resulted in an excessively high value so that the jerk
time is internally limited to 1000 ms.
Note:
The alarm is also output if jerk limiting is not active.
Remedy:
- increase the jerk limiting (p2574).
- reduce maximum acceleration or maximum deceleration (p2572, p2573).
See also: p2572 (EPOS maximum acceleration), p2573 (EPOS maximum deceleration), p2574 (EPOS jerk limiting)
A07441
LR: Save the position offset of the absolute encoder adjustment
Message class:
Error in the parameterization / configuration / commissioning procedure (18)
Reaction:
NONE
Acknowledge:
NONE
Cause:
The status of the absolute encoder adjustment has changed.
In order to permanently save the determined position offset (p2525) it must be saved in a non-volatile fashion
(p0971).
Remedy:
Not necessary.
This alarm automatically disappears after the offset has been saved.
See also: p2507 (LR absolute encoder adjustment status), p2525 (LR encoder adjustment offset)
F07442 (A)
LR: Multiturn does not match the modulo range
Message class:
Error in the parameterization / configuration / commissioning procedure (18)
Reaction:
OFF1 (OFF2, OFF3)
Acknowledge:
IMMEDIATELY
Cause:
The ratio between the multiturn resolution and the modulo range (p2576) is not an integer number.
This results in the adjustment being set back, as the position actual value cannot be reproduced after switch-
off/switch-on.
Remedy:
Make the ration between the multiturn resolution and the modulo range an integer number.
The ratio v is calculated as follows:
1. Motor encoder
v = (p0421 * p2506 * p2505) / (p2504 * p2576)
2. Direct encoder
v = (p0421 * p2506) / p2576
See also: p0412, p0432, p0433, p2504, p2505, p2506, p2576