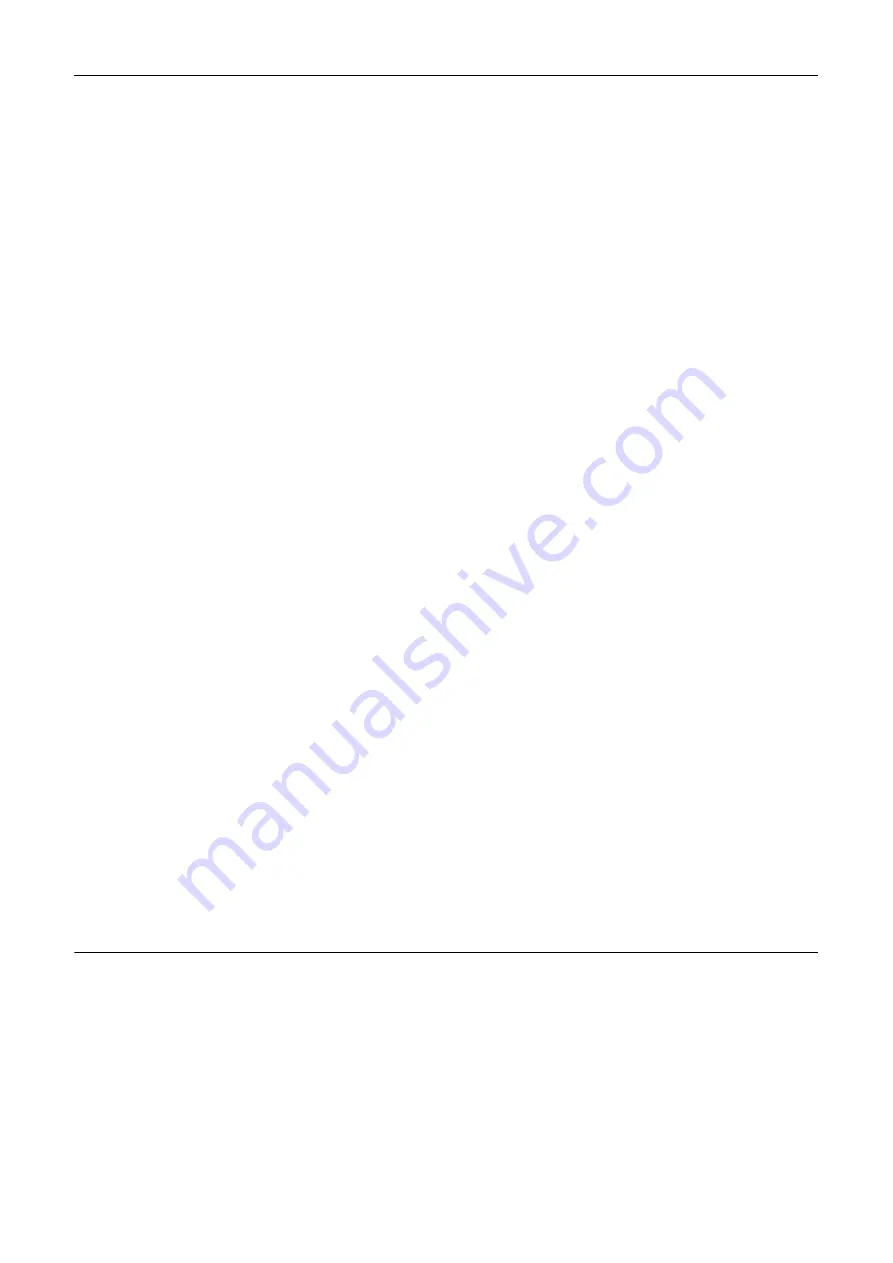
4 Faults and alarms
4.2 List of faults and alarms
SINAMICS G120D
826
List Manual (LH14), 01/2016, A5E33842313
Fault value (r0949, interpret hexadecimal):
xyy hex: x = fault cause, yy = component number or connection number.
1yy:
The communications clock cycle of the DRIVE-CLiQ connection on the Control Unit is not sufficient for all read
transfers.
2yy:
The communications clock cycle of the DRIVE-CLiQ connection on the Control Unit is not sufficient for all write
transfers.
3yy:
Cyclic communication is fully utilized.
4yy:
The DRIVE-CLiQ cycle starts before the earliest end of the application. An additional dead time must be added to the
control. Sign-of-life errors can be expected.
The conditions of operation with a current controller sampling time of 31.25 µs have not been maintained.
5yy:
Internal buffer overflow for net data of a DRIVE-CLiQ connection.
6yy:
Internal buffer overflow for receive data of a DRIVE-CLiQ connection.
7yy:
Internal buffer overflow for send data of a DRIVE-CLiQ connection.
8yy:
The component clock cycles cannot be combined with one another
900:
The lowest common multiple of the clock cycles in the system is too high to be determined.
901:
The lowest common multiple of the clock cycles in the system cannot be generated with the hardware.
Remedy:
- check the DRIVE-CLiQ wiring.
- reduce the number of components on the DRIVE-CLiQ line involved and distribute these to other DRIVE-CLiQ
sockets of the Control Unit. This means that communication is uniformly distributed over several lines.
For fault value = 1yy - 4yy in addition:
- increase the sampling times (p0112, p0115, p4099). If necessary, for DCC or FBLOCKS, change the assignment of
the run-time group (p21000, p20000) so that the sampling time (r21001, r20001) is increased.
- if necessary, reduce the number of cyclically calculated blocks (DCC) and/or function blocks (FBLOCKS).
- reduce the function modules (r0108).
- establish the conditions for operation with a current controller sampling time of 31.25 µs (at the DRIVE-CLiQ line,
only operate Motor Modules and Sensor Modules with this sampling time and only use a permitted Sensor Module
(e.g. SMC20, this means a 3 at the last position of the order number)).
- For an NX, the corresponding Sensor Module for a possibly existing second measuring system should be
connected to a free DRIVE-CLiQ socket of the NX.
For fault value = 8yy in addition:
- check the clock cycles settings (p0112, p0115, p4099). Clock cycles on a DRIVE-CLiQ line must be perfect integer
multiples of one another. As clock cycle on a line, all clock cycles of all drive objects in the previously mentioned
parameters apply, which have components on the line involved.
For fault value = 9yy in addition:
- check the clock cycles settings (p0112, p0115, p4099). The lower the numerical value difference between two clock
cycles, the higher the lowest common multiple. This behavior has a significantly stronger influence, the higher the
numerical values of the clock cycles.
F01505 (A)
BICO: Interconnection cannot be established
Message class:
Error in the parameterization / configuration / commissioning procedure (18)
Reaction:
NONE
Acknowledge:
IMMEDIATELY
Cause:
A PROFIdrive telegram has been set (p0922).
An interconnection contained in the telegram was not able to be established.
Fault value (r0949, interpret decimal):
Parameter receiver that should be changed.
Remedy:
Establish another interconnection.