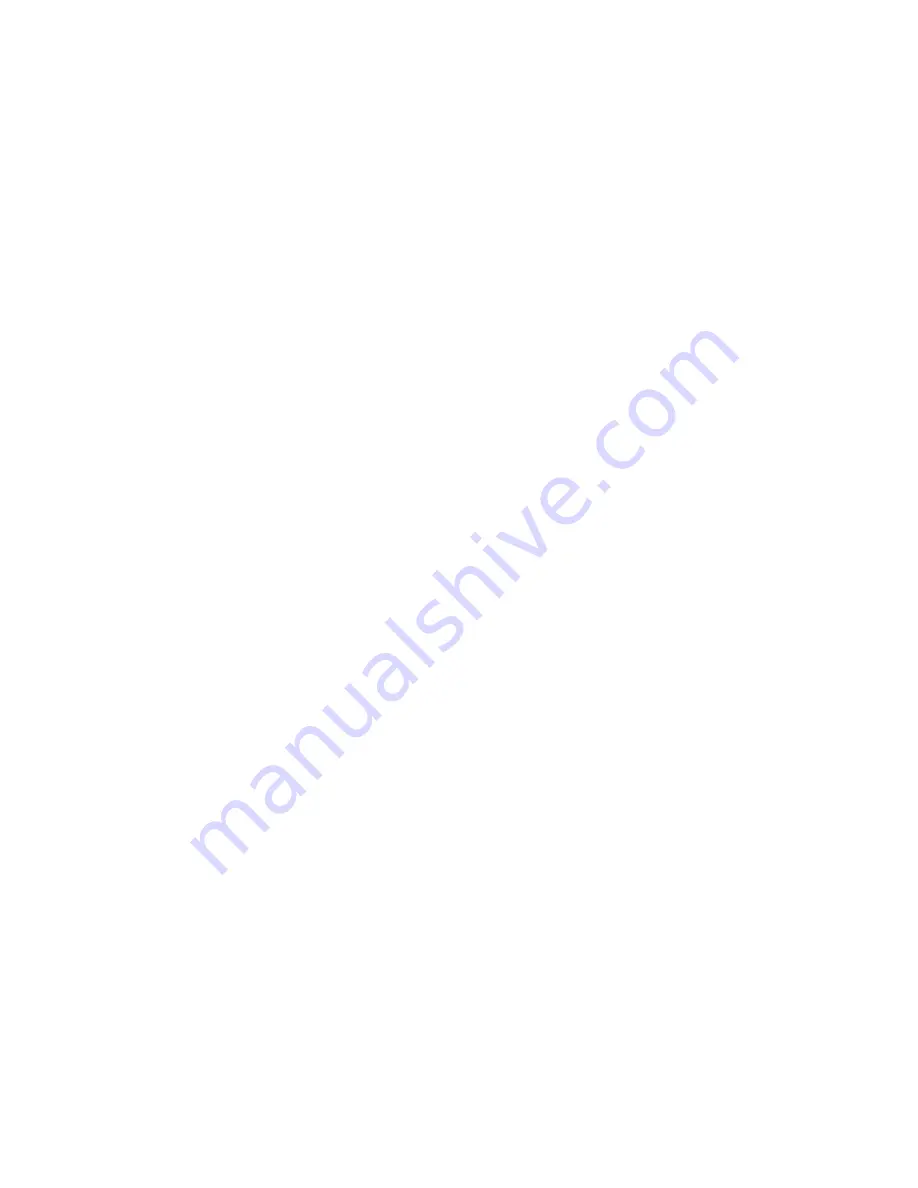
D-76
Parameter Reference
AC30 series Variable Speed Drive
V/F Shape
The function allows the user to parameterise the Drive’s conventional V/F motor fluxing scheme. Four V/F shapes are available, LINEAR LAW, FAN
LAW, USER DEFINED, and APPLICATION DEFINED:
Linear Law V/F shape should be used in applications requiring constant motor torque though out the speed range (e.g. machine tools or
hoists).
Fan Law V/F shape provides less torque capabilities for lower speeds, which means some energy savings can be achieved for fan or
pump applications when they operate at lower speed/load setpoints. When choosing fan law shape the user should carefully consider if
such profile is suitable for the overall load cycle of their application.
User Defined V/F shape provides a method for the user to define any profile. 10 user definable (x,y) points are provided. Linear
interpolation is used between each point. The drive also assumes the following points - (0%,0%) and (100%,100%) - though these may
be overridden. For example, (USER FREQ 1 = 0%, USER VOLTAGE 1 = 5%) takes precedence over (0%, 0%).
Application Defined V/F shape provides a method for the user to define any fluxing profile within the application layer. In the application
the user can set desired voltage level for any operating frequency, and the application will dynamically provide that value to the
firmware, via the “Application Volts” parameter. If this mode is used, it is recommended that such application is executed in 1ms time
frame.
For any of these V/F shapes the
Base Frequency
parameter (in the
Motor Nameplate
function) which is the value of Drive output frequency at
which maximum output volts is provided, can be set by the user.
Boost Parameters
Correct no-load motor fluxing at low Drive output frequencies can be achieved by setting the
Fixed Boost
parameter.
Correct motor fluxing under load conditions is achieved by setting the
Auto Boost
parameter. The motor is correctly fluxed when the
Actual Field Current
diagnostic in the
Feedbacks
function reads 100.0% .
Additional
Fixed
Boost
can be applied during acceleration by setting the
Acceleration Boost
parameter. This can be useful for starting
heavy/high stiction loads.
Saving Energy
An
Energy Saving
mode is provided to allow the user to choose to optimize energy consumption under low load conditions in steady state. As soon
as the load is increased or acceleration is required, the drive suspends energy saving mode, and returns to it only if the load conditions are such that
it is allowed to do so. If enabled, energy saving mode is reducing the voltage of the motor to a level required to maintain specific setpoint speed at a
particular low load. For sustained low load conditions it is not necessary to keep the motor fluxed for rated torque capabilities, so the motor voltage is
Summary of Contents for AC30 series
Page 48: ...4 27 Installation AC30 series Variable Speed Inverter Basic Speed Control Wiring...
Page 50: ...4 29 Installation AC30 series Variable Speed Inverter Auto Manual Control Wiring...
Page 52: ...4 31 Installation AC30 series Variable Speed Inverter Raise Lower Trim Wiring...
Page 54: ...4 33 Installation AC30 series Variable Speed Inverter Presets Speeds Wiring...
Page 56: ...4 35 Installation AC30 series Variable Speed Inverter PID Control Wiring...
Page 150: ...9 25 Setup Wizard AC30 series Variable Speed Inverter Figure 9 16 Charting Drive Parameters...
Page 233: ...Compliance C 20 AC30 series Variable Speed Inverter Frame H...
Page 234: ...C 21 Compliance AC30 series Variable Speed Inverter Frame J...
Page 266: ...D 6 Parameter Reference AC30 series Variable Speed Drive...
Page 343: ...Parameter Reference D 83 AC30 series Variable Speed Drive Offset Input 100 100 x Scale Value...
Page 495: ...E Plan Library E 2 AC30 series Variable Speed Inverter Which then brings up the E Plan page...