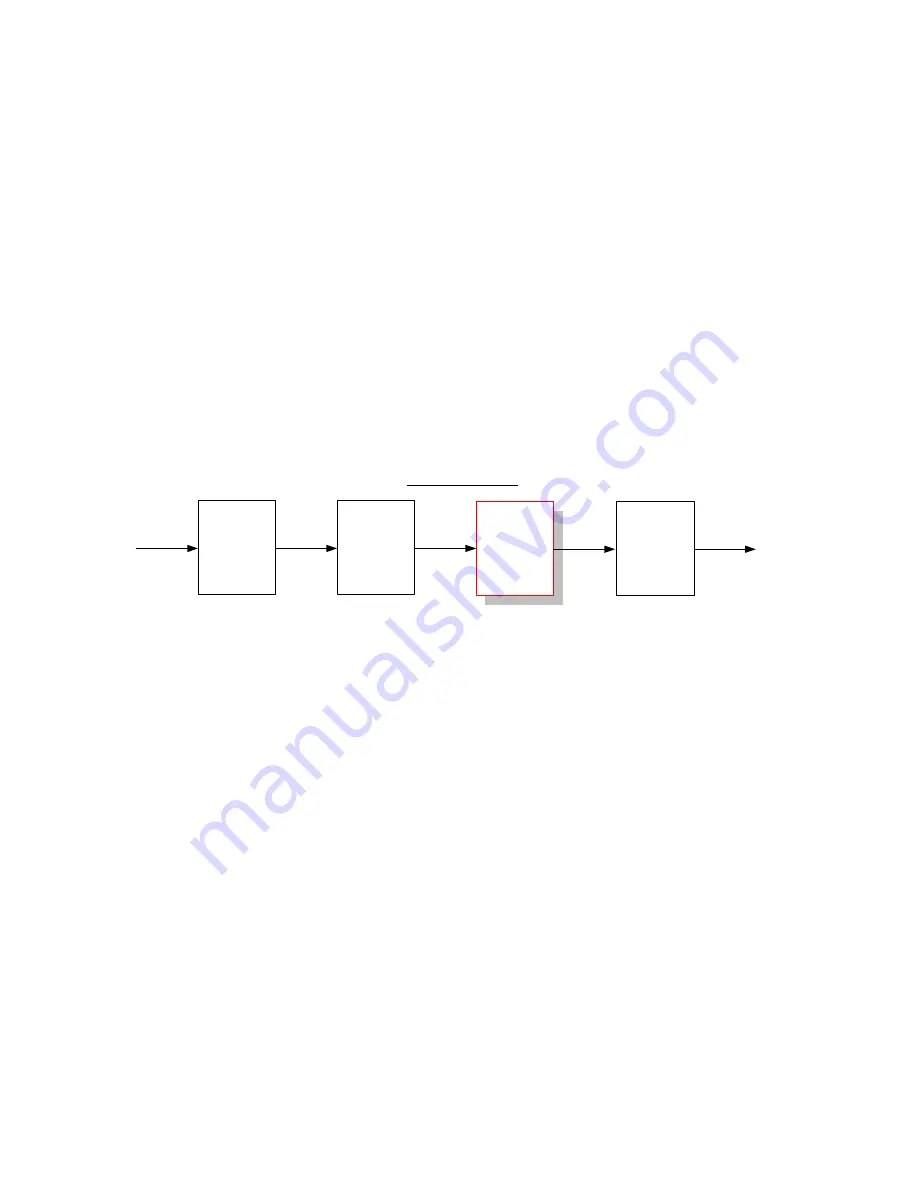
D-44
Parameter Reference
AC30 series Variable Speed Drive
Functional Description
During a fast deceleration, the kinetic energy of the motor load is regenerated to the drive, charging the DC link capacitors.
When the
VDC Lim Level
is reached, the speed septoint is held, waiting for the DC link to go below
VDC Lim Level
.
When the DC link falls below this level, the speed setpoint is released and is ramped down using system ramp deceleration.
This sequence is run until the speed septoint reaches the user speed demand.
By Default,
VDC Lim Level
is set to the same value as the braking threshold.
This feature is run at a rate of 1 milli-second.
Ramp
Power Loss
Ride Thru
DC Link
Volts Limit
Slew Rate
(V/Hz only)
Speed Setpoint path
User
Speed control loop
Summary of Contents for AC30 series
Page 48: ...4 27 Installation AC30 series Variable Speed Inverter Basic Speed Control Wiring...
Page 50: ...4 29 Installation AC30 series Variable Speed Inverter Auto Manual Control Wiring...
Page 52: ...4 31 Installation AC30 series Variable Speed Inverter Raise Lower Trim Wiring...
Page 54: ...4 33 Installation AC30 series Variable Speed Inverter Presets Speeds Wiring...
Page 56: ...4 35 Installation AC30 series Variable Speed Inverter PID Control Wiring...
Page 150: ...9 25 Setup Wizard AC30 series Variable Speed Inverter Figure 9 16 Charting Drive Parameters...
Page 233: ...Compliance C 20 AC30 series Variable Speed Inverter Frame H...
Page 234: ...C 21 Compliance AC30 series Variable Speed Inverter Frame J...
Page 266: ...D 6 Parameter Reference AC30 series Variable Speed Drive...
Page 343: ...Parameter Reference D 83 AC30 series Variable Speed Drive Offset Input 100 100 x Scale Value...
Page 495: ...E Plan Library E 2 AC30 series Variable Speed Inverter Which then brings up the E Plan page...