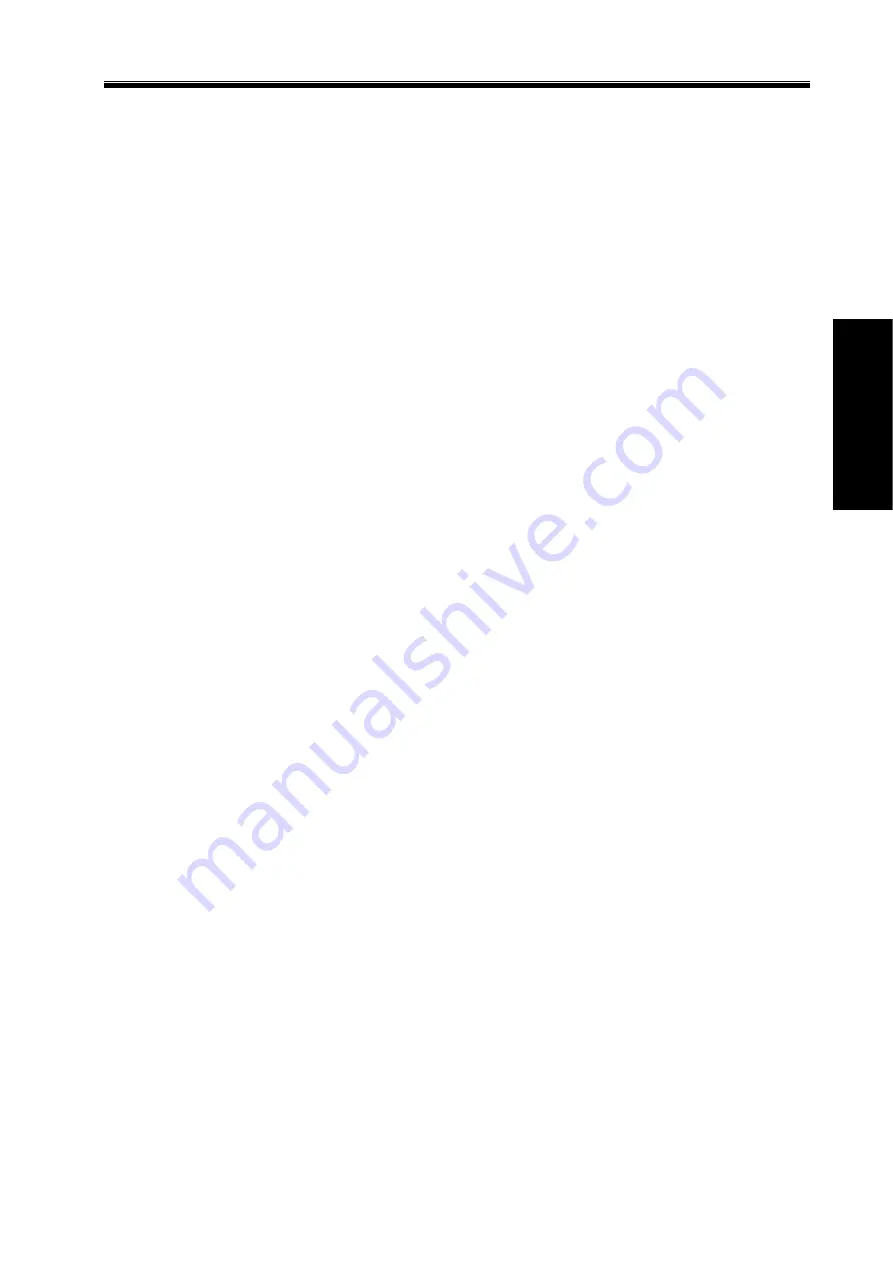
Chapter 2 G Commands
55
Ⅰ
Programming
SKIP signal (SKIP): X0.4
Type: input signal
Function: X0.4 ends the skip cutting. I.e. in a block containing G31, the skip signal becoming
the absolute coordinate position of “1” is to be stored in the macro variable
(#5061
~
#5065, its last bit digit corresponds to the No. n axis of the system), at the
same time, the movement in G31 block ends. No. 6200 Bit1 (SK0) sets the invalid
input state of the skip signal, and when it is set to 0, the input signal 1 is valid.
Operation: When the skip signal becomes “1”, CNC executes as follows: When the block is
executing G31, CNC stores the current absolute coordinates for each axis. CNC
stops G31 to execute the next block, the skip signal detects its state instead of its
RISING EDGE. So when the skip signal is “1”, it meets the skip conditions.
Note 1: When the skip signal is input, the feedrate override, the dry run, and automatic acceleration/
deceleration are invalid in the course of movement by the skip function, which is to improve the tool
positioning precision. Set No. 6200 Bit7(SKF) to 1 to make these function valid.
Note 2: The skip signal is valid, the CNC immediately stops the feed axis (without acceleration/ deceleration
execution), and G31 feedrate should be as low as possible to get the precise stop position.
2.13 Automatic Tool Offset G36, G37
Command function:
When the code is executed to make the tool move to the measured
position, the CNC system automatically measures the difference between
the current actual coordinates and the code coordinates to be the tool
offset value. The function is used to the automatic toolsetting.
Command format:
G36 X__;
G37 Z__;
Explanations:
X absolute coordinate(only used to G36), Z absolute coordinate (only used to
G37);
Non-modal G code (00 group);
Cancel the tool nose radius compensation before using it;
Only use the absolute programming;
Specify the tool offset number before using the code;
Measure position arrival signal:
XAE(X0.6)
――――
corresponding to G36
ZAE(X0.7)
――――
corresponding to G37
Type: input signal
Function: When the position measured by the program code is different from that where the tool
actually reaches (i.e. at the time, the measured position arrival signal becomes the state
set by No.6240#0), the difference of the coordinates is added to the current tool
compensation value to update the compensation value. When G36X_(or G37Z_) is
executed, the tool firstly rapidly traverses to the position
γ
measured by the code, and
decelerates and temporarily stop the position before the measured position, and then,
reaches to the measured position at the speed set by No.6241 (or No.6242). When the
measured position arrival signal corresponding to G code becomes the state set by No.
6240#0, and the tool is in the measured position range ±
ε
, the system updates the offset
Summary of Contents for GSK988TA
Page 6: ...GSK988TA GSK988TA1 GSK988TB Turning Center CNC System User Manual Programming Operation VI ...
Page 19: ...1 Ⅰ Programming PROGRAMMING ...
Page 227: ...209 Ⅱ Operation OPERATION ...
Page 369: ...Chater 10 Machining Example 351 Ⅱ Operation ...
Page 371: ...353 Appendix ...
Page 465: ...Appendix 1 Parameters 447 Appendix ...
Page 479: ...Appendix 3 Interface Explanation 461 Appendix ...
Page 527: ...Appendix 5 Installation Layout 509 Appendix ...