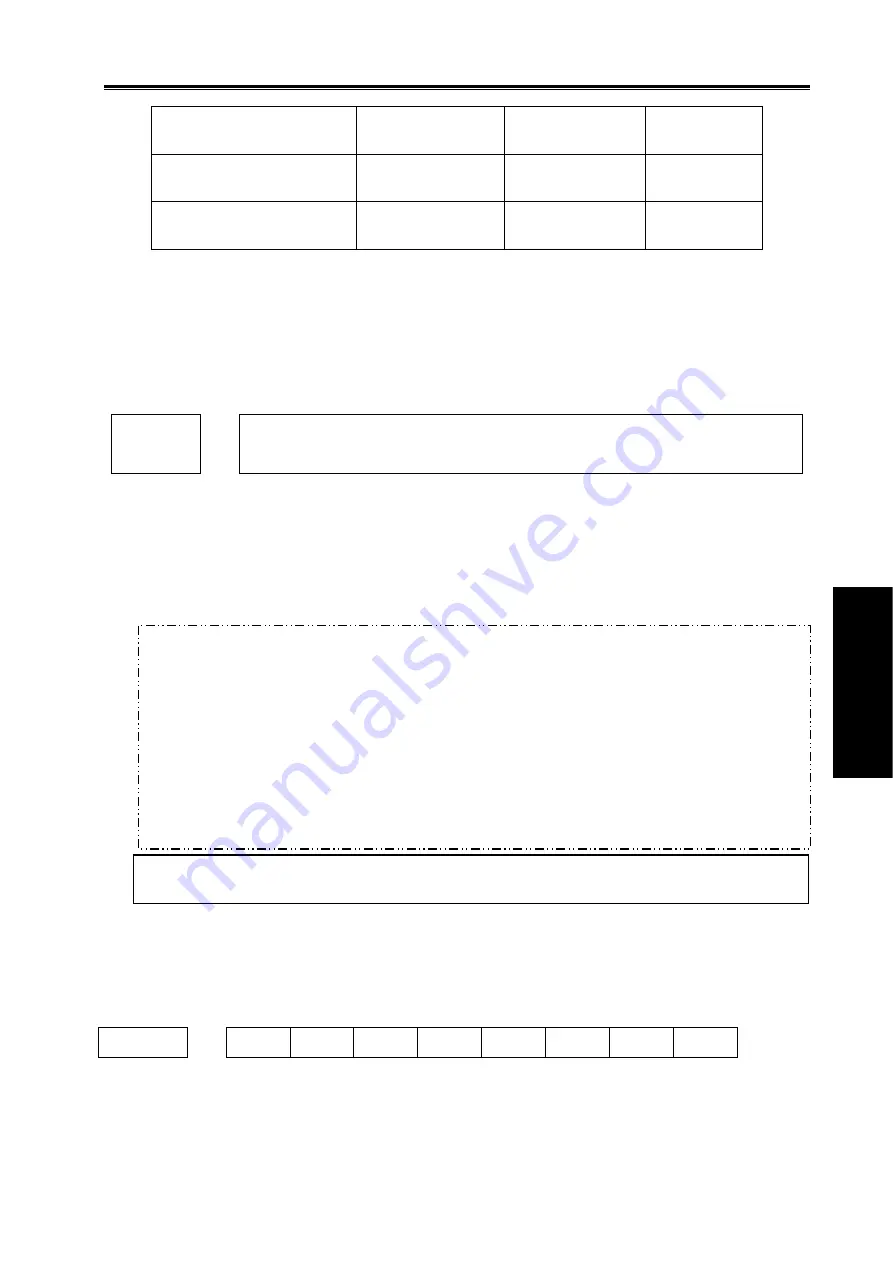
Appendix 1 Parameters
423
Appendix
IS-B
IS-C
UNITS
Machine in metric
system
0, 6
~
24 000
0, 6
~
10 000
mm/min
Machine in inch
system
0, 6
~
9 600
0, 6
~
4 800
inch/min
Set the valid maximum feedrate of the polar coordinate interpolation. If the commanded speed is
greater than the value, the speed is limited by the maximum one. When the parameter is set as 0, the
speed in the polar coordinate interpolation is limited by the maximum cutting feedrate (parameter
NO.1422) value.
5463
Allowable auto override percentage in polar coordinate interpolation
(
API
)
『
Modification authority
』
:Equipment management
『
Value Range
』
: 0
~
100 (%)
『
Default Setting
』
: 0
When the polar coordinate interpolation is set, the percentages of the auto override are allowed
to limit the cutting feedrate of the rotary axis.
Note: When the parameter value is set as 0, it is taken as 90%;
To limit the auto speed override and the auto speed, the parameter AFC (NO.5450#1) is set as 1.
Appendix 1.18 Parameter of User Macro Program
#7 #6 #5 #4 #3 #2 #1 #0
6000
SBM
G67
『
Modification authority
』
:Equipment management
『
Default Setting
』
: 0000 0000
#0 G67 Macro program mode calling (G66) mode is not set, but mode calling command (G67) is
The allowable speed of the rotary axis = Maximum cutting feedrate X override
percentage
In polar coordinate interpolation, the more closely the tool is near to the work piece
center, the bigger the speed vector of the rotary axis is. When it exceeds the allowable speed,
the feedrate automatically multiplies by the override value calculated through the following
formula:
Override = Allowable speed of the rotary axis/the speed vector of the rotary axis X 100%
If the revolving speed after timing the override still exceeds the allowable speed, the feedrate
is limited in the allowable maximum cutting feedrate (auto speed limit function) .
Summary of Contents for GSK988TA
Page 6: ...GSK988TA GSK988TA1 GSK988TB Turning Center CNC System User Manual Programming Operation VI ...
Page 19: ...1 Ⅰ Programming PROGRAMMING ...
Page 227: ...209 Ⅱ Operation OPERATION ...
Page 369: ...Chater 10 Machining Example 351 Ⅱ Operation ...
Page 371: ...353 Appendix ...
Page 465: ...Appendix 1 Parameters 447 Appendix ...
Page 479: ...Appendix 3 Interface Explanation 461 Appendix ...
Page 527: ...Appendix 5 Installation Layout 509 Appendix ...