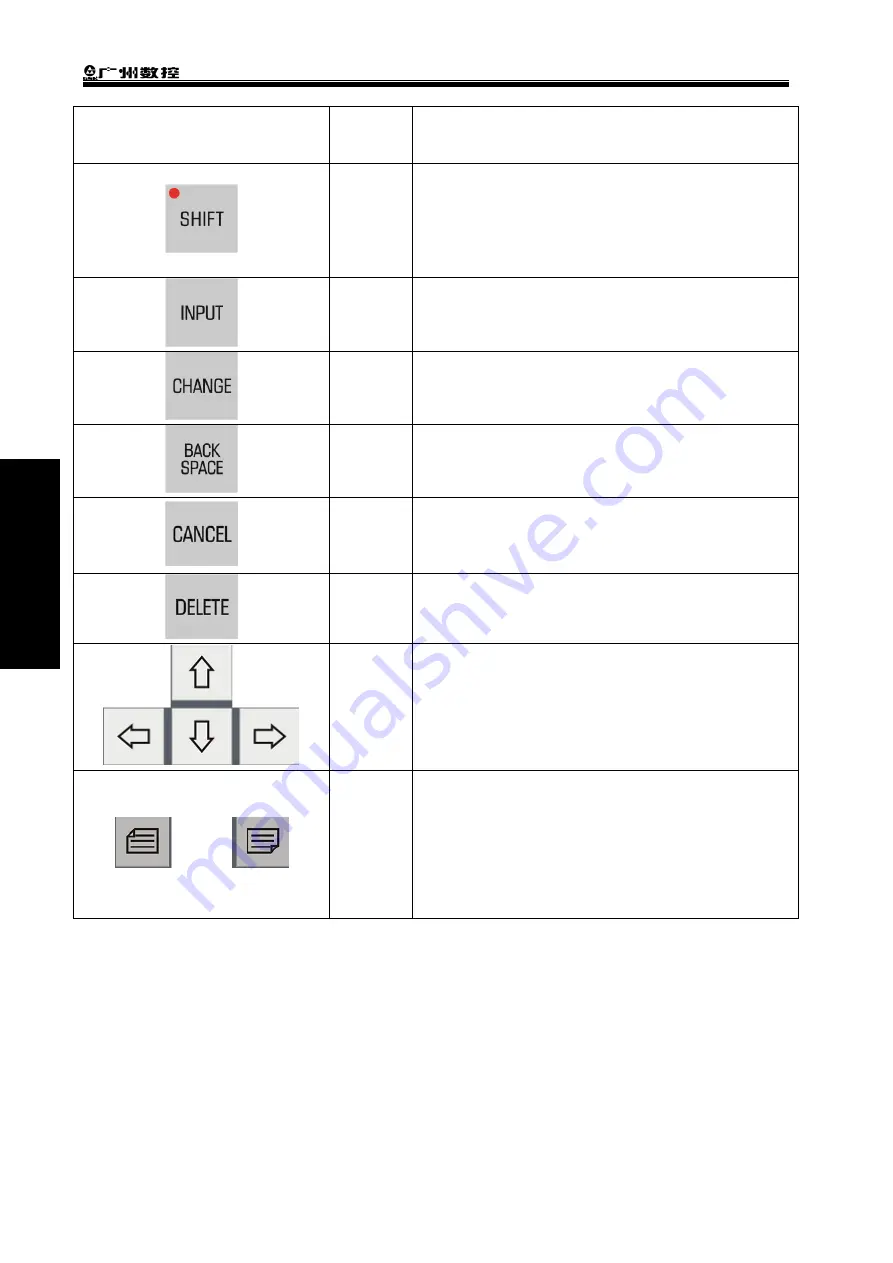
GSK988TA/GSK988TA1/GSK988TB Turning Center CNC System User Manual
【
Programming & Operation
】
216
Ⅱ
Operation
Button Name
Function
Shift key
Switch the double-address key, double-symbol key,
address symbol key and digit address key. Pressing
the shift key and it light is ON. Press the address
key and the input is the upward address; it
combined with the cursor key can select a block
Input key
Confirm the data input and line feed during editing
the program
Change
key
Switch message/display, Tab key function, fast
shortkey with other keys when editing programs
Backspa
ce key
Delete the characters before the cursor
Cancel
key
Cancel the current operation
Delete
key
Delete the character after the cursor
Cursor
move-
ment key
Control the cursor left/right/upward/downward
Page key Switch the page in the same display interface
Summary of Contents for GSK988TA
Page 6: ...GSK988TA GSK988TA1 GSK988TB Turning Center CNC System User Manual Programming Operation VI ...
Page 19: ...1 Ⅰ Programming PROGRAMMING ...
Page 227: ...209 Ⅱ Operation OPERATION ...
Page 369: ...Chater 10 Machining Example 351 Ⅱ Operation ...
Page 371: ...353 Appendix ...
Page 465: ...Appendix 1 Parameters 447 Appendix ...
Page 479: ...Appendix 3 Interface Explanation 461 Appendix ...
Page 527: ...Appendix 5 Installation Layout 509 Appendix ...