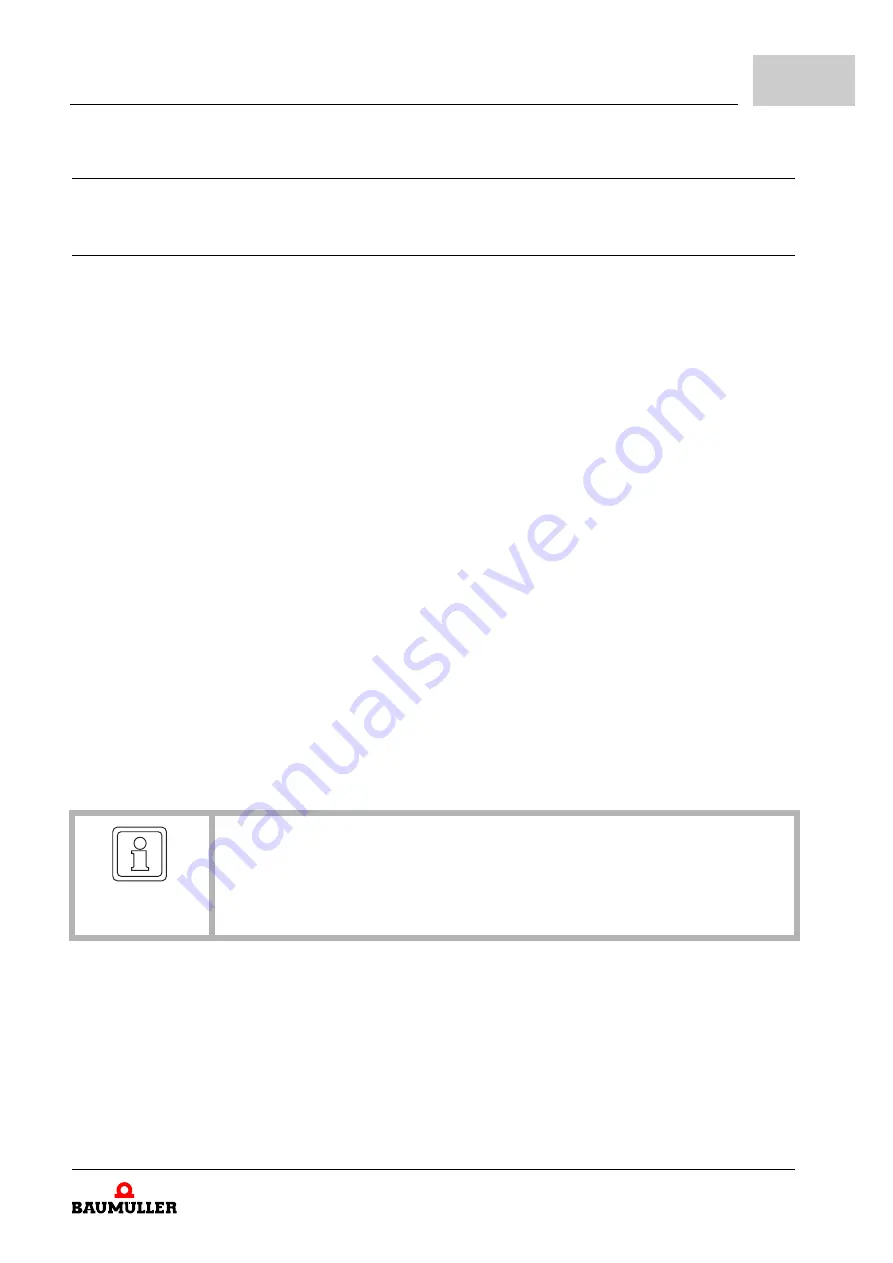
Description of the Software Modules and Parameters
Parameter manual
b maXX
BM5800
Document No.: 5.16029.03
329
3
3.5.3
Brake management
3.5.3.1 Description of the Brake Management System
On drives with a motor holding brake, the brake can be operated manually or automati-
cally depending on the state of the drive.
The triggering is effected by means of a separate digital output. A separate digital input
is available to detect the brake state. The brake state can be monitored. When monitoring
is active, an error message is transmitted in the event of an error (brake could not be en-
abled/applied).
Adaptation to the differing reaction times of holding brakes is possible by means of con-
figurable response times and delay times.
Manual Brake Triggering (
Bit 0 = 0)
The brake can be applied and enabled independently of the state of the drive.(
Bit 0).
Automatic Brake Triggering (
In the Automatic mode, the brake is actuated depending on the state of the device con-
troller (see
from page 289). In states 0 ("Not Ready to Switch On")
to 3 ("Switched On"), the brake is applied. The brake is enabled on the transition to State
4 ("Operation Enabled").
For commissioning purposes (
Bit 1 = 1), the brake can also be applied and en-
abled manually in the Automatic mode (Service mode).
Enabling the
Brake
When the drive is started, power is applied to the motor in state transition 3
4
("Switched On"
"Operation Enabled") before the brake is enabled. This prevents a sus-
pended axis from sagging. The requirement for this is at least a speed-controlled operat-
ing mode.
NOTE!
A suspended axis will
NOT
be prevented from sagging in the following cases:
m
The drive is working in one of the modes "Find Notch Position", "Autotuning",
"Current Control", "Current Setting" or "Voltage Setting".
m
The drive is being operated without encoders.