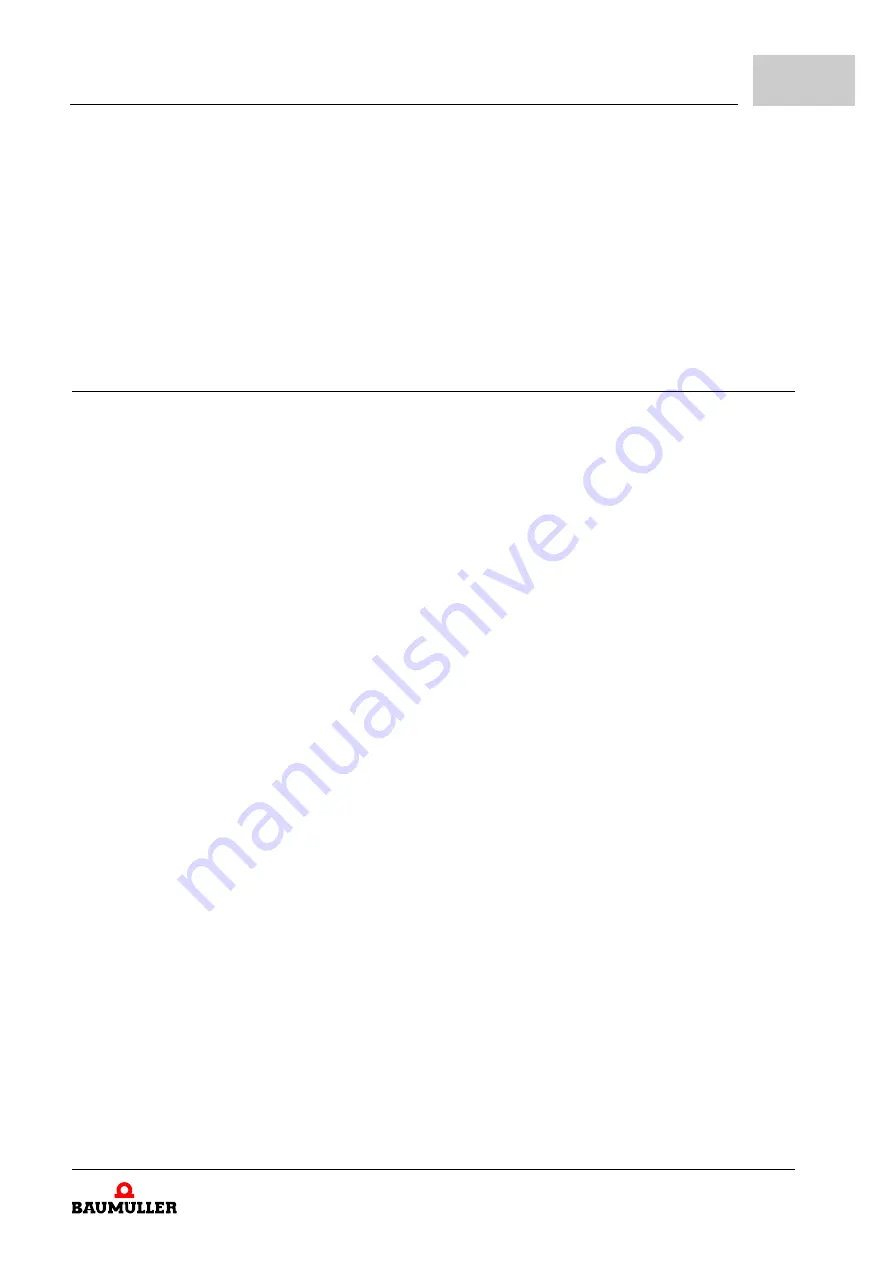
Description of the Software Modules and Parameters
Parameter manual
b maXX
BM5800
Document No.: 5.16029.03
151
3
In
the synchronization of the resolver is represented. Via bit 4 of parameter
the excitation frequency can be set to 8 kHz and activates the synchronization.
The Dsp interrupt is synchronized to the fieldbus and the resolver tracks (blue) are syn-
chronized to the first Dsp interrupt. The excitation (green) is shifted so that the maximum
of the resulting sine and cosine track is synchronous to the Dsp interrupt. The phase shift
between the Dsp interrupt and the accordant maximums are set via the parameter
and accepts values between 0 and 124 µs. Thereby, the excitation voltages of
the amplitude and the phase towards one another can deviate depending on the imped-
ance of the resolver.
3.4.6.9 Encoder angle via fieldbus
The encoder angle can be transferred via the fieldbus with the b maXX 5000. This is es-
pecially a benefit, when having motors with several windings with one encoder cabling, if
a splitting of the encoder cable is to be avoided. It must be considered during the appli-
cation, that there is a dead time due to the fieldbus transmission. This must be parame-
terized, so that all converters get the same electric angle. In order that all of the
participants observe the same current set value, a dead time in the current set value must
be additionally added at the master. Hereby, highly-dynamical applications with quick
changes of high electrical frequencies are not suited.
Setting
At a motor with several windings there is always a "Master converter" connected with the
encoder. The other converters are slaves obtaining their encoder angle via the fieldbus
(
= 9). The following parameters must be transmitted via the fieldbus:
Actual angle value of encoder
x2 actual speed value filtered
These parameters must be mapped to the following parameters:
Encoder angle fieldbus
Encoder angle speed
To minimize the dead time the control should be operated with by a cycle time which is
as low as possible. The lowest dead time results in a slave to slave communication. Here-
by, the master must be in position 1 of the fieldbus topology and the slaves in further po-
sitions. In this configuration the total dead time must be calculated as follows:
At a fieldbus cycle time of 1 ms and a speed controller cycle of 250 µs a dead time of
2.25 ms follows. This must be entered at the master in the
(delay current set val-
ue) and at the slave in the
(fieldbus dead time).
Because of the additional dead time in the speed control loop speed and position control
loops cannot be operated with the standard gains.
T
Deadtime,total
2
T
Fieldbus
T
RT0
+
=