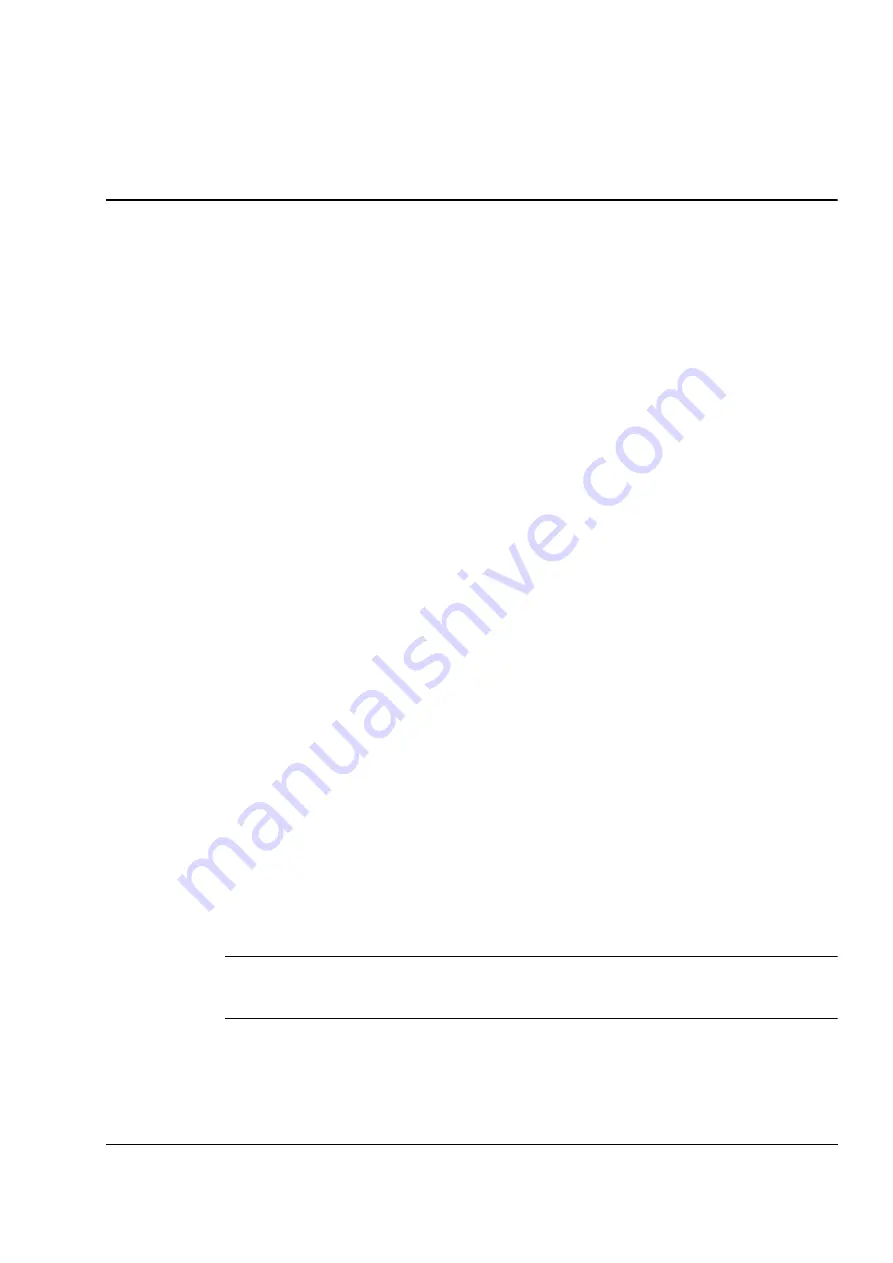
Appendix B – Drive-to-drive link
431
Appendix B – Drive-to-drive link
What this chapter contains
This chapter describes the wiring of, and available communication methods on the
drive-to-drive link. Examples of using standard function blocks in the communication
are also given starting on page
.
General
The drive-to-drive link is a daisy-chained RS-485 transmission line, constructed by
connecting the X5 terminal blocks of the JCU Control Units of several drives. It is
also possible to use an FMBA Modbus extension module installed into an option slot
on the JCU. The firmware supports up to 63 nodes on the link.
The link has one master drive; the rest of the drives are followers. By default, the
master broadcasts control commands as well as speed and torque references for all
followers. The master can also be configured to send a position reference as either
target position or synchronization reference. The master can send 8 messages per
millisecond at 100/150-microsecond intervals. Sending one message takes
approximately 15 microseconds, which results in a theoretical link capacity of
roughly 6 messages per 100 microseconds.
Multicasting the control data and reference 1 to a pre-defined group of drives is
possible, as is chained multicast messaging. Reference 2 is always broadcast by the
master to all followers. See parameters
…
.
Wiring
Shielded twisted-pair cable (~100 ohm, eg, PROFIBUS-compatible cable) must be
used for the wiring. The maximum length of the link is 50 metres (164 ft).
The JCU Control Unit has a jumper (J3, “T”) next to the X5 terminal block for bus
termination. Termination must be ON on the drives at the ends of the drive-to-drive
link; on intermediate drives, termination must be OFF.
Instead of the X5 connector, an FMBA Modbus extension module can be used.
For best immunity, high quality cable is recommended. The cable should be kept as
short as possible. Unnecessary loops and running the cable near power cables
(such as motor cables) must be avoided.
Note:
The cable shields are to be grounded to the control cable clamp plate on the
drive. Follow the instructions given in the
Hardware Manual
of the drive.
Summary of Contents for ACSM1 Series
Page 1: ...ABB motion control drives Firmware manual ACSM1 motion control program ...
Page 4: ......
Page 34: ...Drive programming using PC tools 34 ...
Page 86: ...Drive control and features 86 ...
Page 265: ...Parameters and firmware blocks 265 1 100 us 100 µs 2 1 ms 1 ms 3 50 ms 50 ms ...
Page 302: ...Parameter data 302 ...
Page 422: ...Application program template 422 ...
Page 430: ...Appendix A Fieldbus control 430 ...
Page 500: ...Appendix D Application examples 500 ...
Page 508: ...Appendix E Control chain and drive logic diagrams 508 ...
Page 510: ...3AFE68848270 REV H EN 2015 06 26 Contact us www abb com drives www abb com drivespartners ...