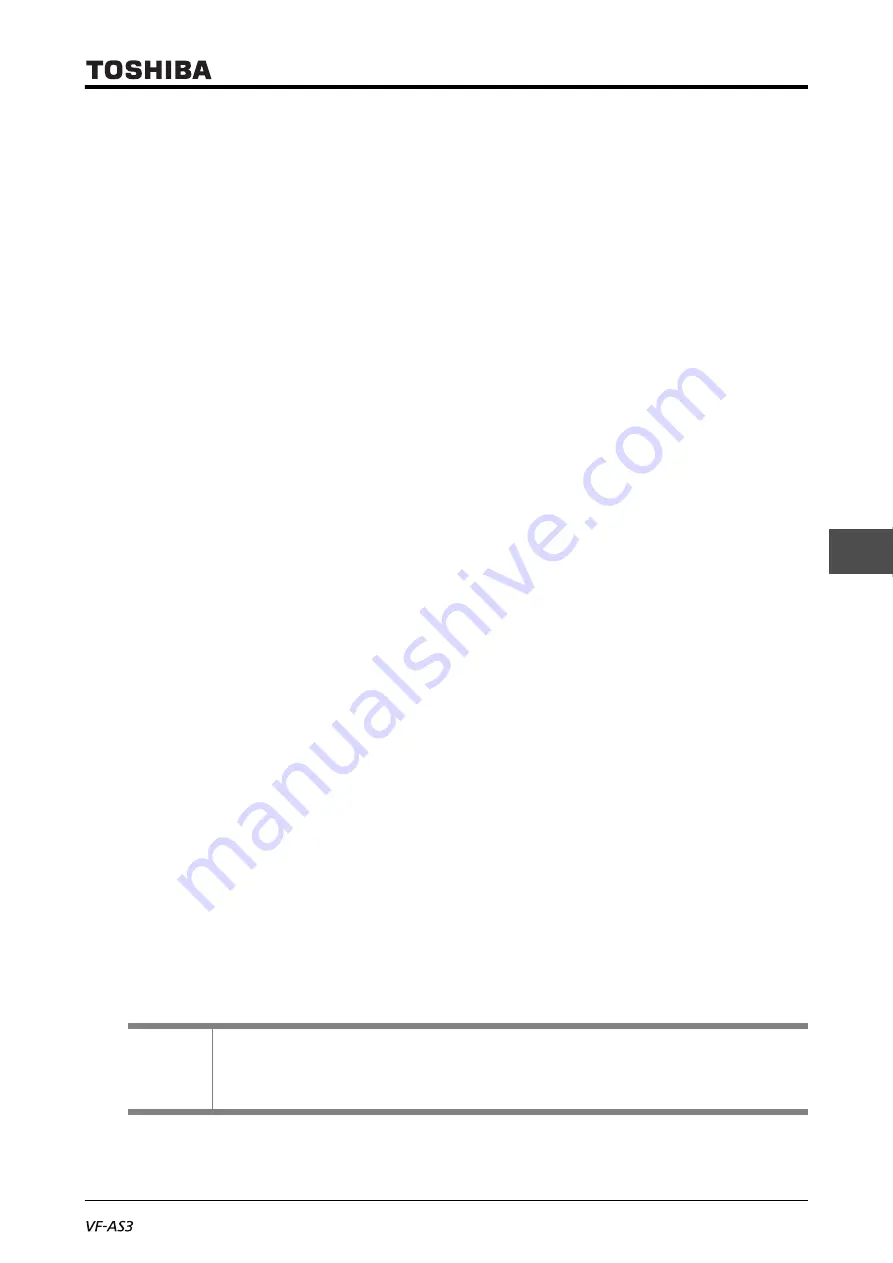
E6582062
6-87
6. [Advanced] How to use parameters
3
4
6
9
Increasing this value will increase the exciting current.
Keep in mind that setting a value too high will cause hunting in the motor.
<F417: Motor rated speed>
This parameter sets the motor rated speed.
Check the motor name plate or test report while setting.
6) Motor parameter setting method (Advanced)
• How to adjust the moment of inertia of the load
<F459: Load inertia ratio>
This parameter adjusts the excess response speed.
Increasing this value will reduce the overshoot at the acceleration/deceleration completion
point.
Default setting values are set so that the moment of inertia of the load (including the motor
shaft) value is set to be appropriate at 100% of the motor shaft. If the moment of inertia of the
load is not 100%, set a value appropriate for the actual inertia of the load.
<F460: Speed control response 1>
<F461: Speed control stabilization coefficient 1>
<F462: Speed reference filter coefficient 1>
<F463: Speed control response 2>
<F464: Speed control stabilization coefficient 2>
<F465: Speed reference filter coefficient 2>
<F466: Speed control response switching frequency>
This parameter adjusts the excess response speed.
Increasing this value will reduce the overshoot at the acceleration/deceleration completion
point. Set a value appropriate for the actual inertia of the load.
For details, refer to "Current and Speed Control Gain Adjustment Method" manual (E6582136).
• If the torque needs to be increased in low speed range (10Hz or less as a guide)
Perform the basic settings for the motor parameters. Then, if the torque needs to be
increased even further, increase <F413: Exciting current coefficient> to a maximum of 130%.
<F413> is a parameter that increases the magnetic flux of the motor at low speeds, so
specifying a higher value for <F413> increases the no-load current. If the no-load current
exceeds the rated current, do not adjust this parameter.
• If the motor stalls when operated at frequencies over the base frequency
Adjust <F414: Stall prevention coefficient>.
If a heavy load is applied momentarily (transiently), the motor may stall before the load
current reaches the stall prevention level (<F601>, etc.). In such a case, a motor stall may be
avoided by reducing the value of <F414> gradually.
Memo
• To use vector control, the motor capacity must be the same as the inverter rated capacity, or
you can use a general purpose squirrel-cage motor with capacity no less than one rank below.
Note that the minimum applicable motor capacity is 0.1 kW.
Summary of Contents for TOSVERT VF-AS3
Page 2: ...1 9 ...
Page 14: ......
Page 17: ...E6582062 iii I 3 9 15 Warranty 15 1 16 Disposal 16 1 ...
Page 18: ......
Page 34: ......
Page 438: ......
Page 458: ......
Page 470: ......
Page 482: ......
Page 502: ......
Page 572: ......
Page 590: ......
Page 608: ......
Page 616: ......
Page 618: ......
Page 620: ......
Page 621: ...1 3 9 10 ...