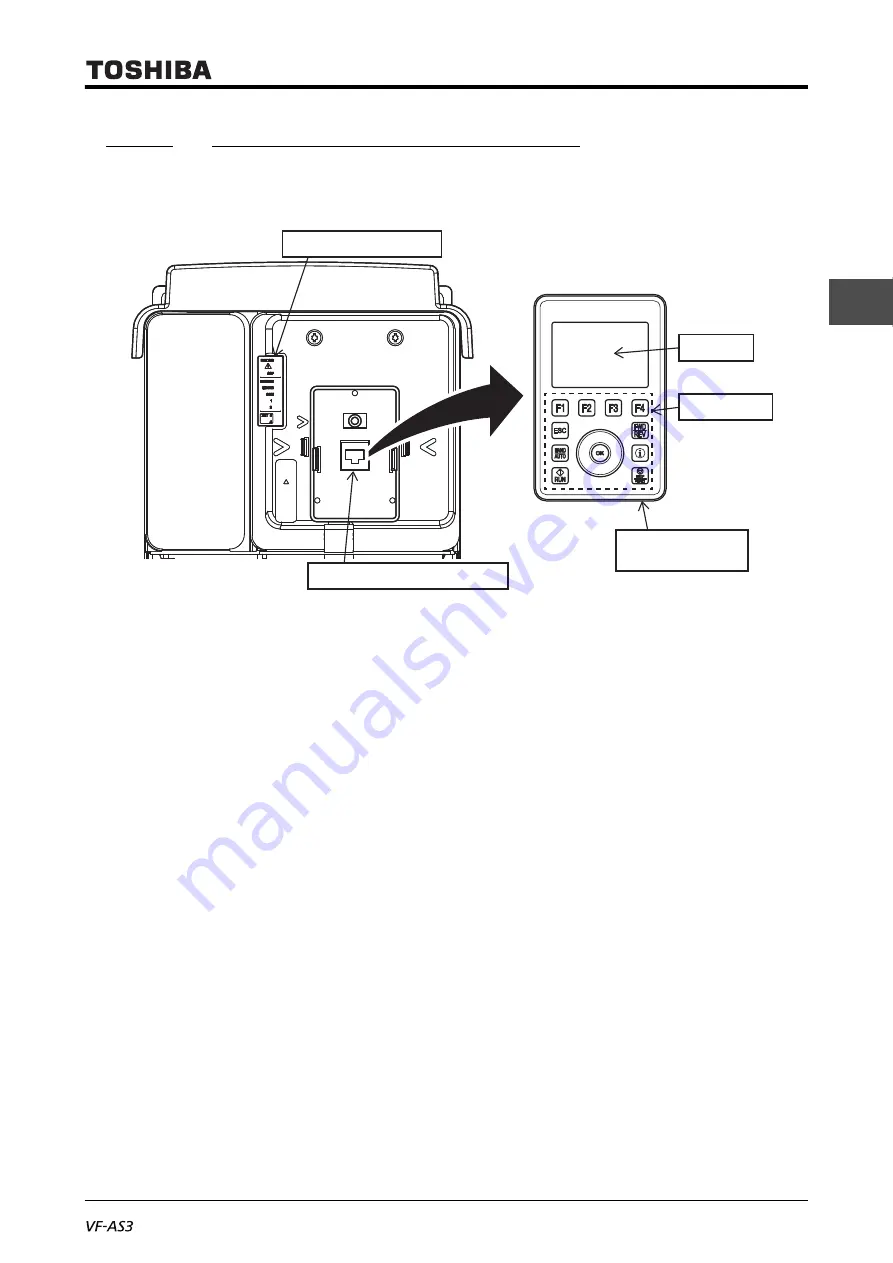
E6582062
1-9
1. Read first
1
3
9
10
1. 4. 2
Operation panel and peripherals
The operation panel of the inverter is directly connected to RS485 communication connector 1.
It is equipped with some indicators for inverter status on the left side of the operation panel.
■
Operation panel
The operation panel is equipped with a LCD screen and operation keys on the front side and two
types of connectors (operation panel female connector and USB-miniB connector) on the bottom
surface.
It is directly connected to the unit with the operation panel male connector on the back side but can
be removed. It can be also used for remote control with Door mounting kit (SBP010Z) and an
exclusive cable (optional), see [10. 3. 8] for detail.
• LCD screen
The operation panel is equipped with a multilingual (8 languages) LCD that displays the frequency,
parameters and their set values and the operation status according to the display mode of the
inverter. For details, refer to [3. 1. 1].
• Operation keys
There are an [ESC] key, [HAND/AUTO] key, [RUN] key, [FWD/REV] key, [i] key, [STOP/RESET] key,
[F1] to [F4] keys, touch wheel, and [OK] key.
The [F1] to [F4] keys execute functions according to the indication on the lower side of the LCD
screen.
With the touch wheel, you can change the menu items and values on the screen by touching it by
your finger to rotate to the right or left or touching its upper side or lower side lightly.
For details of the operation keys, refer to [3. 1. 1].
• Operation panel lower side cover
This cover protects two connectors on the right of the lower side of the operation panel and the slot for
battery on the left. The right side/left side of the cover can be opened respectively.
Indicator for inverter status
RS485 communication connector 1
LCD screen
Operation keys
Operation panel lower
side cover
Summary of Contents for TOSVERT VF-AS3
Page 2: ...1 9 ...
Page 14: ......
Page 17: ...E6582062 iii I 3 9 15 Warranty 15 1 16 Disposal 16 1 ...
Page 18: ......
Page 34: ......
Page 438: ......
Page 458: ......
Page 470: ......
Page 482: ......
Page 502: ......
Page 572: ......
Page 590: ......
Page 608: ......
Page 616: ......
Page 618: ......
Page 620: ......
Page 621: ...1 3 9 10 ...