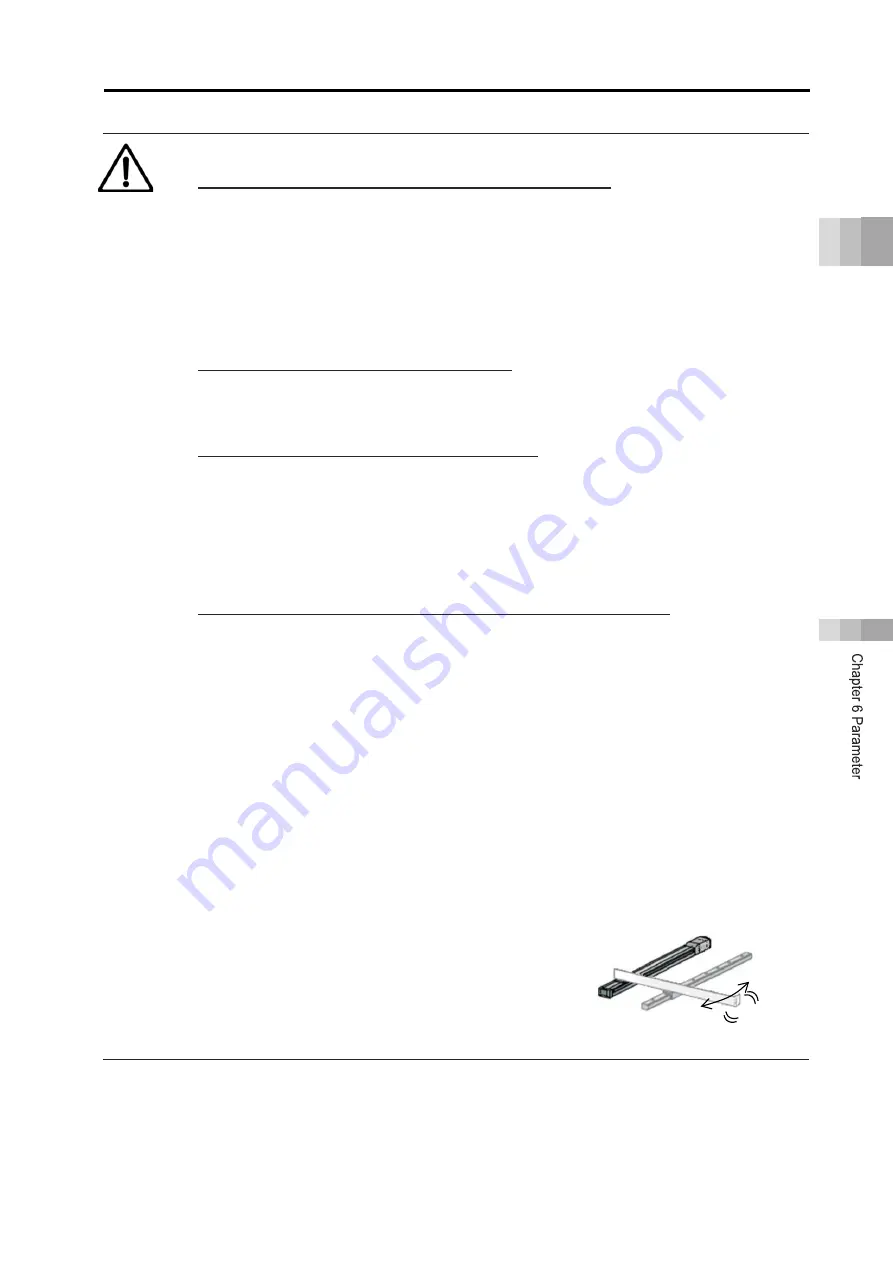
6.2 Various Functions
B6-66
ME0384-4A
St
art
up
Se
ctio
n
Caution
●
Use of frequency analysis tool for vibration damping control
To use the frequency analysis tool for vibration damping control built into the PC
software, it is necessary to acquire the key file (Fam.dll) and copy it into the folder
containing the file to execute the PC software (RcPc.exe). Consult with IAI about the
key file.
For operation method, refer to "Chapter 14 Frequency Analysis Function for Vibration
Damping Control" in the instruction manual for the PC software.
●
Vibration subject to vibration damping control
The vibration is caused by an IAI actuator, in the same direction as the travel direction
of the actuator.
●
Vibration not subject to vibration damping control
1) The vibration source is other than operation of the actuator
2) The vibration source is in a direction different from the travel direction of the actuator
3) Vibration of vibrating objects (This function is to move objects that are susceptible to
vibration without vibrating, and it cannot control vibrations which have already
started)
●
Conditions when vibration damping control is unlikely to be effective
1) When the vibration frequency desired to be controlled matches the frequency of the
motor mechanical angle (motor rotation speed), or frequency of the motor electrical
angle
Frequency of motor mechanical angle (motor rotation speed): Operation speed
[mm/s]/lead length [mm]
Frequency of motor electrical angle: Frequency of the shaft with servo-motor is 4
times the mechanical angle
Example: Shaft with servo-motor
For lead length: 20mm, operation speed 100mm/s
Frequency of mechanical angle (motor rotation speed): 5Hz
Frequency of electrical angle (4 times frequency of mechanical angle): 20Hz
2) When the vibration damping requires higher speed response than the set speed
control response, speed response cannot catch
up with vibration control.
3) When the device is similar to the diagram at right,
as the actuator cannot directly control the
vibration, the effect may be reduced or
unachievable.
Linear Guide
Actuator
vibration
Summary of Contents for Rcon
Page 12: ...ME0384 4A ...
Page 32: ...Actuator Coordinate System Intro 20 ME0384 4A ...
Page 42: ...1 3 General Specifications A1 9 ME0384 4A Specifications Section Chapter 1 RCON Overview ...
Page 45: ...ME0384 4A ...
Page 291: ...ME0384 4A ...
Page 323: ...ME0384 4A ...
Page 384: ...1 3 Startup Procedure B1 9 ME0384 4A Startup Section Chapter 1 Overview ...
Page 420: ...3 6 Precautions B3 15 ME0384 4A Startup Section Chapter 3 Absolute Reset ...
Page 588: ...6 2 Various Functions B6 81 ME0384 4A Startup Section ...
Page 837: ......
Page 838: ......