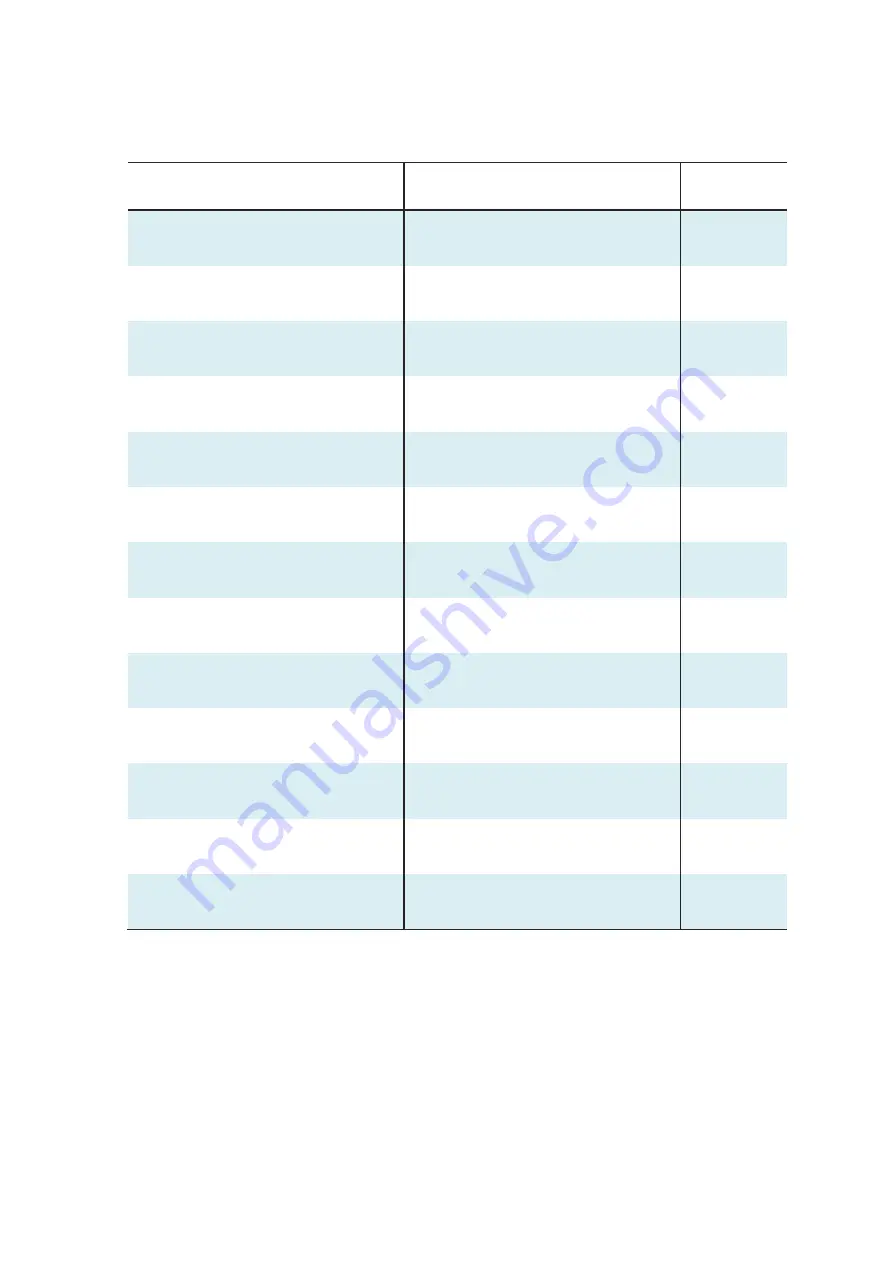
ME0384-4A
RCON System Instruction Manual Configuration
Product name
Instruction manual name
Control
number
RCON Gateway Unit
First Step Guide
ME0382
RCON 24V Driver Unit
First Step Guide
ME0383
RCON 200V
Power Supply / Driver Unit
First Step Guide
ME0397
REC
System
First Step Guide
ME0395
RCON System
Instruction Manual (this document)
ME0384
REC
System
REC-GW/RCON-EC
Instruction Manual
ME0394
SCON-CB Controller
SCON-CB/CGB/LC/LCG
Instruction Manual
ME0340
PC Software
RCM-101-MW/RCM-101-USB
Instruction Manual
ME0155
Touch Panel Teaching Pendant
TB-02/02D Instruction Manual
ME0355
Touch Panel Teaching Pendant
TB-03 Instruction Manual
ME0376
24V Power Supply Unit
PSA-24 Instruction Manual
ME0379
Calculator
Calculator Instruction Manual
ME0381
Network Startup Guide
Quick Start Guide
Download from IAI
homepage
Summary of Contents for Rcon
Page 12: ...ME0384 4A ...
Page 32: ...Actuator Coordinate System Intro 20 ME0384 4A ...
Page 42: ...1 3 General Specifications A1 9 ME0384 4A Specifications Section Chapter 1 RCON Overview ...
Page 45: ...ME0384 4A ...
Page 291: ...ME0384 4A ...
Page 323: ...ME0384 4A ...
Page 384: ...1 3 Startup Procedure B1 9 ME0384 4A Startup Section Chapter 1 Overview ...
Page 420: ...3 6 Precautions B3 15 ME0384 4A Startup Section Chapter 3 Absolute Reset ...
Page 588: ...6 2 Various Functions B6 81 ME0384 4A Startup Section ...
Page 837: ......
Page 838: ......