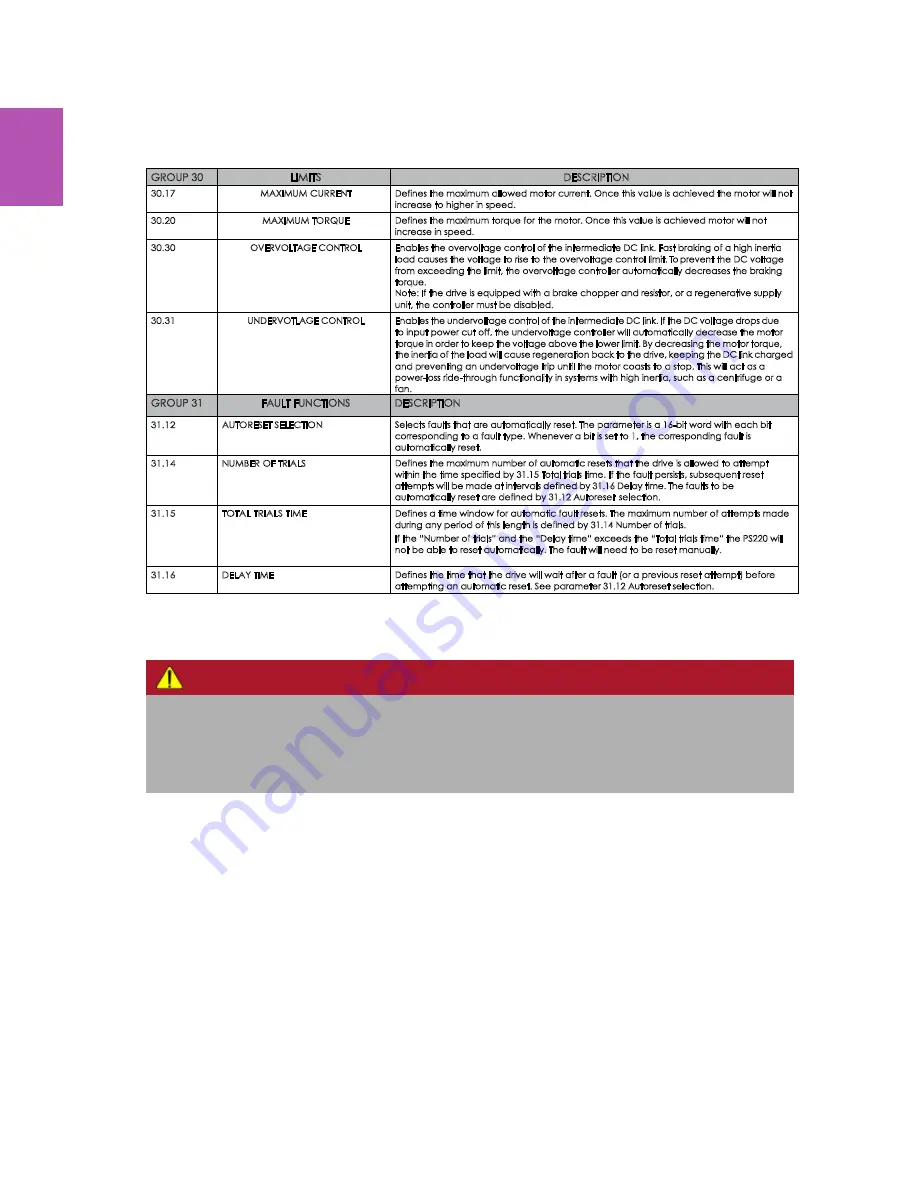
PS220 Configuration & Operation Guide
233 PS220
Function & F
eatures
The table below shows all of the parameters used for the VFD protection. Additional Motor limits and
protection parameters are described in the index under the Parameter Listing for the Groups 30 and 31.
GROUP 30
LIMITS
DESCRIPTION
30.17
MAXIMUM CURRENT
Defines the maximum allowed motor current. Once this value is achieved the motor will not
increase to higher in speed.
30.20
MAXIMUM TORQUE
Defines the maximum torque for the motor. Once this value is achieved motor will not
increase in speed.
30.30
OVERVOLTAGE CONTROL
Enables the overvoltage control of the intermediate DC link. Fast braking of a high inertia
load causes the voltage to rise to the overvoltage control limit. To prevent the DC voltage
from exceeding the limit, the overvoltage controller automatically decreases the braking
torque.
Note: If the drive is equipped with a brake chopper and resistor, or a regenerative supply
unit, the controller must be disabled.
30.31
UNDERVOTLAGE CONTROL
Enables the undervoltage control of the intermediate DC link. If the DC voltage drops due
to input power cut off, the undervoltage controller will automatically decrease the motor
torque in order to keep the voltage above the lower limit. By decreasing the motor torque,
the inertia of the load will cause regeneration back to the drive, keeping the DC link charged
and preventing an undervoltage trip until the motor coasts to a stop. This will act as a
power-loss ride-through functionality in systems with high inertia, such as a centrifuge or a
fan.
GROUP 31
FAULT FUNCTIONS
DESCRIPTION
31.12
AUTORESET SELECTION
Selects faults that are automatically reset. The parameter is a 16-bit word with each bit
corresponding to a fault type. Whenever a bit is set to 1, the corresponding fault is
automatically reset.
31.14
NUMBER OF TRIALS
Defines the maximum number of automatic resets that the drive is allowed to attempt
within the time specified by 31.15 Total trials time. If the fault persists, subsequent reset
attempts will be made at intervals defined by 31.16 Delay time. The faults to be
automatically reset are defined by 31.12 Autoreset selection.
31.15
TOTAL TRIALS TIME
Defines a time window for automatic fault resets. The maximum number of attempts made
during any period of this length is defined by 31.14 Number of trials.
If the “Number of trials” and the “Delay time” exceeds the “Total trials time” the PS220 will
not be able to reset automatically. The fault will need to be reset manually.
31.16
DELAY TIME
Defines the time that the drive will wait after a fault (or a previous reset attempt) before
attempting an automatic reset. See parameter 31.12 Autoreset selection.
Before you activate any part or parts of this function, proceed with extreme caution. This function
resets the drive automatically and continues automatic operation after a Fault. This may result in
severe equipment damage and/or physical injury and death.
DANGER
Содержание PumpSmart PS220
Страница 1: ...Configuration Operation Manual PumpSmart Control Solutions PS220 v6 05...
Страница 5: ...PS220 Configuration Operation Guide PS220 4 Getting Started THIS PAGE IS INTENTIONALLY LEFT BLANK...
Страница 9: ...PS220 Configuration Operation Guide PS220 8 Basic Startup THIS PAGE IS INTENTIONALLY LEFT BLANK...
Страница 22: ...PS220 Configuration Operation Guide 21 PS220 SmartFlow...
Страница 40: ...PS220 Configuration Operation Guide 39 PS220 Process Control THIS PAGE IS INTENTIONALLY LEFT BLANK...
Страница 217: ...PS220 Configuration Operation Guide PS220 216 Functions Features This is an example of a typical Pump Performance Curve...
Страница 261: ...PS220 Configuration Operation Guide PS220 260 THIS PAGE IS INTENTIONALLY LEFT BLANK...
Страница 283: ...PS220 Configuration Operation Guide PS220 282 THIS PAGE IS INTENTIONALLY LEFT BLANK...
Страница 289: ...PS220 Configuration Operation Guide PS220 288 Ecodesign Regulation...
Страница 292: ...PS220 Configuration Operation Guide 291 PS220 Fuses heat dissipation chart...