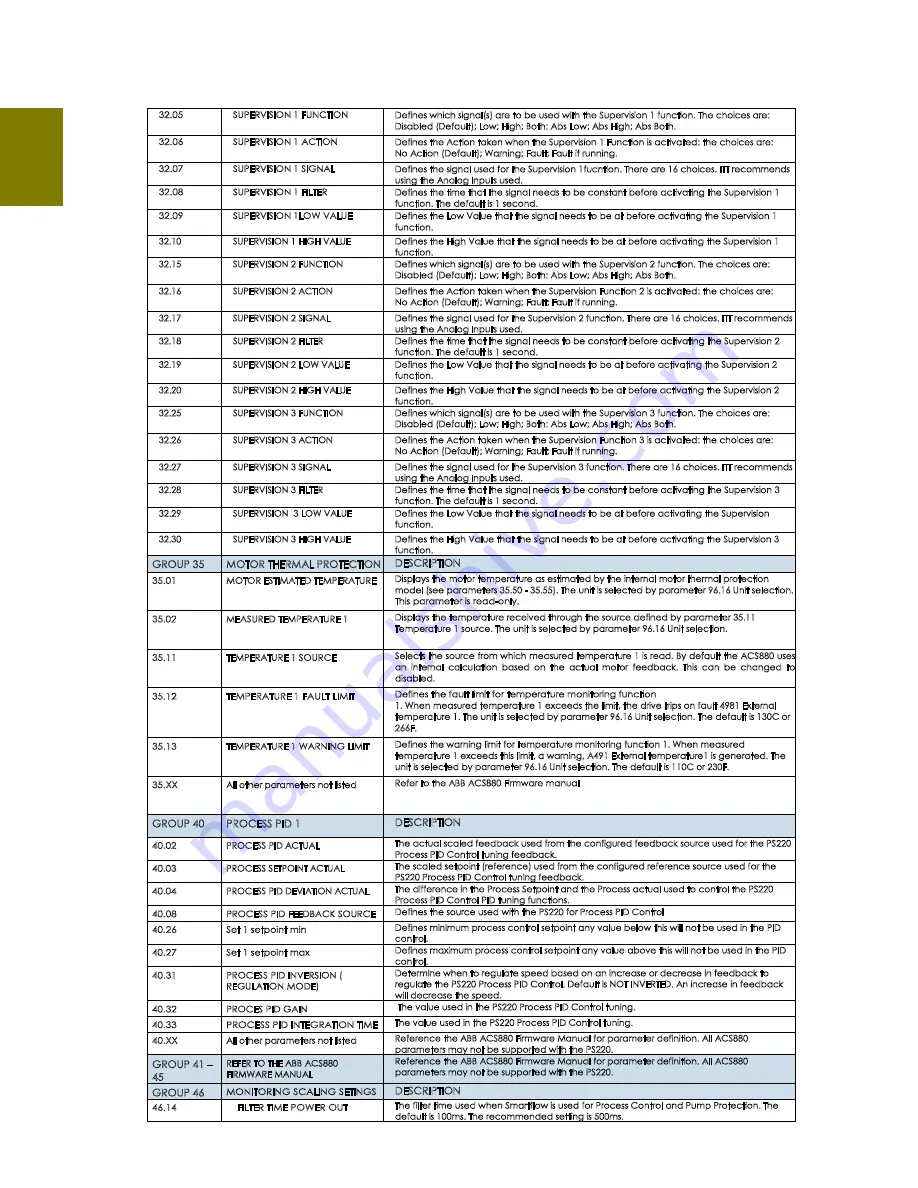
PS220 Configuration & Operation Guide
269 PS220
Parameter
Listing
32.05
SUPERVISION 1 FUNCTION
Defines which signal(s) are to be used with the Supervision 1 function. The choices are:
Disabled (Default); Low; High; Both: Abs Low; Abs High; Abs Both.
32.06
SUPERVISION 1 ACTION
Defines the Action taken when the Supervision 1 Function is activated: the choices are:
No Action (Default); Warning; Fault; Fault if running.
32.07
SUPERVISION 1 SIGNAL
Defines the signal used for the Supervision 1fucntion. There are 16 choices. ITT recommends
using the Analog Inputs used.
32.08
SUPERVISION 1 FILTER
Defines the time that the signal needs to be constant before activating the Supervision 1
function. The default is 1 second.
32.09
SUPERVISION 1LOW VALUE
Defines the Low Value that the signal needs to be at before activating the Supervision 1
function.
32.10
SUPERVISION 1 HIGH VALUE
Defines the High Value that the signal needs to be at before activating the Supervision 1
function.
32.15
SUPERVISION 2 FUNCTION
Defines which signal(s) are to be used with the Supervision 2 function. The choices are:
Disabled (Default); Low; High; Both: Abs Low; Abs High; Abs Both.
32.16
SUPERVISION 2 ACTION
Defines the Action taken when the Supervision Function 2 is activated: the choices are:
No Action (Default); Warning; Fault; Fault if running.
32.17
SUPERVISION 2 SIGNAL
Defines the signal used for the Supervision 2 function. There are 16 choices. ITT recommends
using the Analog Inputs used.
32.18
SUPERVISION 2 FILTER
Defines the time that the signal needs to be constant before activating the Supervision 2
function. The default is 1 second.
32.19
SUPERVISION 2 LOW VALUE
Defines the Low Value that the signal needs to be at before activating the Supervision 2
function.
32.20
SUPERVISION 2 HIGH VALUE
Defines the High Value that the signal needs to be at before activating the Supervision 2
function.
32.25
SUPERVISION 3 FUNCTION
Defines which signal(s) are to be used with the Supervision 3 function. The choices are:
Disabled (Default); Low; High; Both: Abs Low; Abs High; Abs Both.
32.26
SUPERVISION 3 ACTION
Defines the Action taken when the Supervision Function 3 is activated: the choices are:
No Action (Default); Warning; Fault; Fault if running.
32.27
SUPERVISION 3 SIGNAL
Defines the signal used for the Supervision 3 function. There are 16 choices. ITT recommends
using the Analog Inputs used.
32.28
SUPERVISION 3 FILTER
Defines the time that the signal needs to be constant before activating the Supervision 3
function. The default is 1 second.
32.29
SUPERVISION 3 LOW VALUE
Defines the Low Value that the signal needs to be at before activating the Supervision
function.
32.30
SUPERVISION 3 HIGH VALUE
Defines the High Value that the signal needs to be at before activating the Supervision 3
function.
GROUP 35
MOTOR THERMAL PROTECTION DESCRIPTION
35.01
MOTOR ESTIMATED TEMPERATURE
Displays the motor temperature as estimated by the internal motor thermal protection
model (see parameters 35.50 - 35.55). The unit is selected by parameter 96.16 Unit selection.
This parameter is read-only.
35.02
MEASURED TEMPERATURE 1
Displays the temperature received through the source defined by parameter 35.11
Temperature 1 source. The unit is selected by parameter 96.16 Unit selection.
35.11
TEMPERATURE 1 SOURCE
Selects the source from which measured temperature 1 is read. By default the ACS880 uses
an internal calculation based on the actual motor feedback. This can be changed to
disabled.
35.12
TEMPERATURE 1 FAULT LIMIT
Defines the fault limit for temperature monitoring function
1. When measured temperature 1 exceeds the limit, the drive trips on fault 4981 External
temperature 1. The unit is selected by parameter 96.16 Unit selection. The default is 130C or
266F.
35.13
TEMPERATURE 1 WARNING LIMIT
Defines the warning limit for temperature monitoring function 1. When measured
temperature 1 exceeds this limit, a warning, A491 External temperature1 is generated. The
unit is selected by parameter 96.16 Unit selection. The default is 110C or 230F.
35.XX
All other parameters not listed
Refer to the ABB ACS880 Firmware manual
GROUP 40
PROCESS PID 1
DESCRIPTION
40.02
PROCESS PID ACTUAL
The actual scaled feedback used from the configured feedback source used for the PS220
Process PID Control tuning feedback.
40.03
PROCESS SETPOINT ACTUAL
The scaled setpoint (reference) used from the configured reference source used for the
PS220 Process PID Control tuning feedback.
40.04
PROCESS PID DEVIATION ACTUAL
The difference in the Process Setpoint and the Process actual used to control the PS220
Process PID Control PID tuning functions.
40.08
PROCESS PID FEEDBACK SOURCE
Defines the source used with the PS220 for Process PID Control
40.26
Set 1 setpoint min
Defines minimum process control setpoint any value below this will not be used in the PID
control.
40.27
Set 1 setpoint max
Defines maximum process control setpoint any value above this will not be used in the PID
control.
40.31
PROCESS PID INVERSION (
REGULATION MODE)
Determine when to regulate speed based on an increase or decrease in feedback to
regulate the PS220 Process PID Control. Default is NOT INVERTED. An increase in feedback
will decrease the speed.
40.32
PROCES PID GAIN
The value used in the PS220 Process PID Control tuning.
40.33
PROCESS PID INTEGRATION TIME
The value used in the PS220 Process PID Control tuning.
40.XX
All other parameters not listed
Reference the ABB ACS880 Firmware Manual for parameter definition. All ACS880
parameters may not be supported with the PS220.
GROUP 41 –
45
REFER TO THE ABB ACS880
FIRMWARE MANUAL
Reference the ABB ACS880 Firmware Manual for parameter definition. All ACS880
parameters may not be supported with the PS220.
GROUP 46
MONITORING SCALING SETINGS
DESCRIPTION
46.14
FILTER TIME POWER OUT
The filter time used when Smartflow is used for Process Control and Pump Protection. The
default is 100ms. The recommended setting is 500ms.
Содержание PumpSmart PS220
Страница 1: ...Configuration Operation Manual PumpSmart Control Solutions PS220 v6 05...
Страница 5: ...PS220 Configuration Operation Guide PS220 4 Getting Started THIS PAGE IS INTENTIONALLY LEFT BLANK...
Страница 9: ...PS220 Configuration Operation Guide PS220 8 Basic Startup THIS PAGE IS INTENTIONALLY LEFT BLANK...
Страница 22: ...PS220 Configuration Operation Guide 21 PS220 SmartFlow...
Страница 40: ...PS220 Configuration Operation Guide 39 PS220 Process Control THIS PAGE IS INTENTIONALLY LEFT BLANK...
Страница 217: ...PS220 Configuration Operation Guide PS220 216 Functions Features This is an example of a typical Pump Performance Curve...
Страница 261: ...PS220 Configuration Operation Guide PS220 260 THIS PAGE IS INTENTIONALLY LEFT BLANK...
Страница 283: ...PS220 Configuration Operation Guide PS220 282 THIS PAGE IS INTENTIONALLY LEFT BLANK...
Страница 289: ...PS220 Configuration Operation Guide PS220 288 Ecodesign Regulation...
Страница 292: ...PS220 Configuration Operation Guide 291 PS220 Fuses heat dissipation chart...