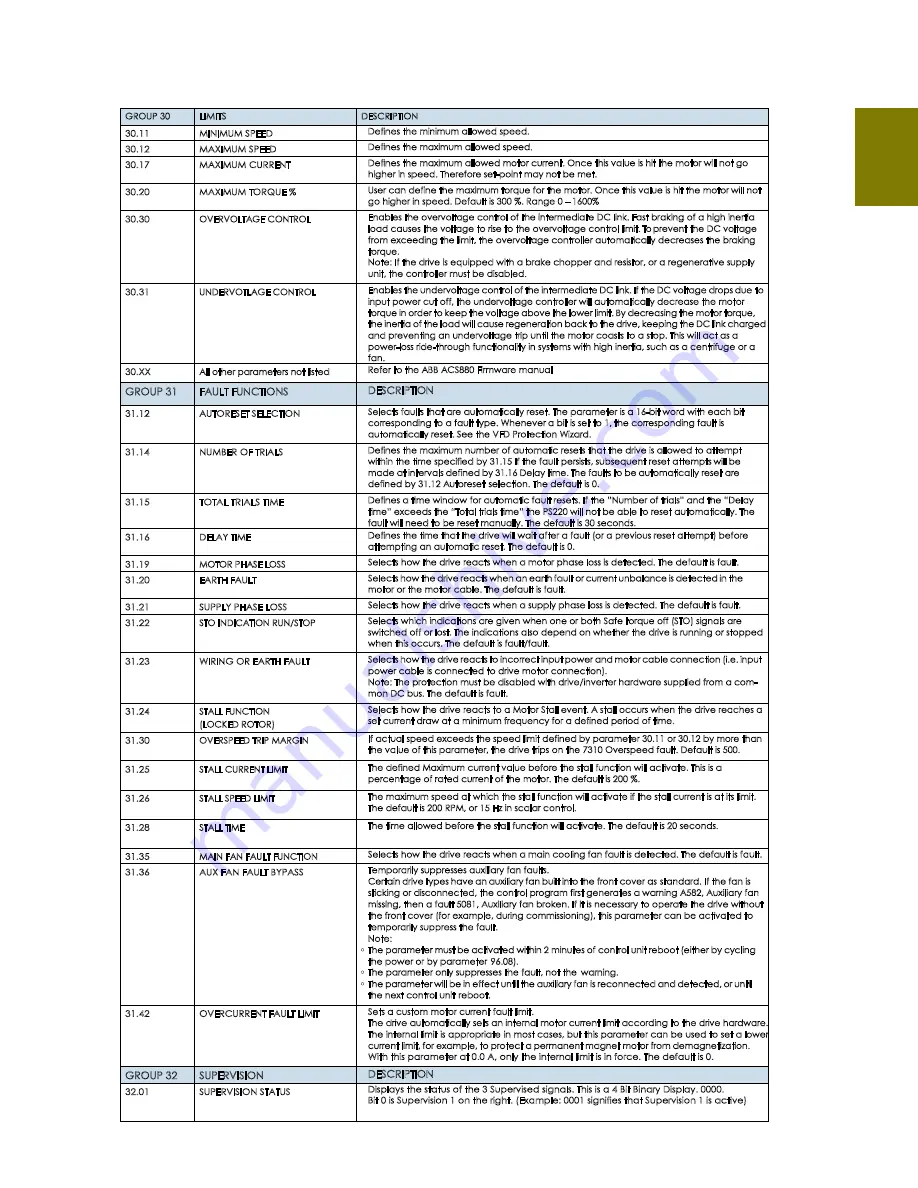
PS220 Configuration & Operation Guide
PS220 268
Parameter
Listing
GROUP 30
LIMITS
DESCRIPTION
30.11
MINIMUM SPEED
Defines the minimum allowed speed.
30.12
MAXIMUM SPEED
Defines the maximum allowed speed.
30.17
MAXIMUM CURRENT
Defines the maximum allowed motor current. Once this value is hit the motor will not go
higher in speed. Therefore set-point may not be met.
30.20
MAXIMUM TORQUE %
User can define the maximum torque for the motor. Once this value is hit the motor will not
go higher in speed. Default is 300 %. Range 0 – 1600%
30.30
OVERVOLTAGE CONTROL
Enables the overvoltage control of the intermediate DC link. Fast braking of a high inertia
load causes the voltage to rise to the overvoltage control limit. To prevent the DC voltage
from exceeding the limit, the overvoltage controller automatically decreases the braking
torque.
Note: If the drive is equipped with a brake chopper and resistor, or a regenerative supply
unit, the controller must be disabled.
30.31
UNDERVOTLAGE CONTROL
Enables the undervoltage control of the intermediate DC link. If the DC voltage drops due to
input power cut off, the undervoltage controller will automatically decrease the motor
torque in order to keep the voltage above the lower limit. By decreasing the motor torque,
the inertia of the load will cause regeneration back to the drive, keeping the DC link charged
and preventing an undervoltage trip until the motor coasts to a stop. This will act as a
power-loss ride-through functionality in systems with high inertia, such as a centrifuge or a
fan.
30.XX
All other parameters not listed
Refer to the ABB ACS880 Firmware manual
GROUP 31
FAULT FUNCTIONS
DESCRIPTION
31.12
AUTORESET SELECTION
Selects faults that are automatically reset. The parameter is a 16-bit word with each bit
corresponding to a fault type. Whenever a bit is set to 1, the corresponding fault is
automatically reset. See the VFD Protection Wizard.
31.14
NUMBER OF TRIALS
Defines the maximum number of automatic resets that the drive is allowed to attempt
within the time specified by 31.15 If the fault persists, subsequent reset attempts will be
made at intervals defined by 31.16 Delay time. The faults to be automatically reset are
defined by 31.12 Autoreset selection. The default is 0.
31.15
TOTAL TRIALS TIME
Defines a time window for automatic fault resets. If the “Number of trials” and the “Delay
time” exceeds the “Total trials time” the PS220 will not be able to reset automatically. The
fault will need to be reset manually. The default is 30 seconds.
31.16
DELAY TIME
Defines the time that the drive will wait after a fault (or a previous reset attempt) before
attempting an automatic reset. The default is 0.
31.19
MOTOR PHASE LOSS
Selects how the drive reacts when a motor phase loss is detected. The default is fault.
31.20
EARTH FAULT
Selects how the drive reacts when an earth fault or current unbalance is detected in the
motor or the motor cable. The default is fault.
31.21
SUPPLY PHASE LOSS
Selects how the drive reacts when a supply phase loss is detected. The default is fault.
31.22
STO INDICATION RUN/STOP
Selects which indications are given when one or both Safe torque off (STO) signals are
switched off or lost. The indications also depend on whether the drive is running or stopped
when this occurs. The default is fault/fault.
31.23
WIRING OR EARTH FAULT
Selects how the drive reacts to incorrect input power and motor cable connection (i.e. input
power cable is connected to drive motor connection).
Note: The protection must be disabled with drive/inverter hardware supplied from a com-
mon DC bus. The default is fault.
31.24
STALL FUNCTION
(LOCKED ROTOR)
Selects how the drive reacts to a Motor Stall event. A stall occurs when the drive reaches a
set current draw at a minimum frequency for a defined period of time.
31.30
OVERSPEED TRIP MARGIN
If actual speed exceeds the speed limit defined by parameter 30.11 or 30.12 by more than
the value of this parameter, the drive trips on the 7310 Overspeed fault. Default is 500.
31.25
STALL CURRENT LIMIT
The defined Maximum current value before the stall function will activate. This is a
percentage of rated current of the motor. The default is 200 %.
31.26
STALL SPEED LIMIT
The maximum speed at which the stall function will activate if the stall current is at its limit.
The default is 200 RPM, or 15 Hz in scalar control.
31.28
STALL TIME
The time allowed before the stall function will activate. The default is 20 seconds.
31.35
MAIN FAN FAULT FUNCTION
Selects how the drive reacts when a main cooling fan fault is detected. The default is fault.
31.36
AUX FAN FAULT BYPASS
Temporarily suppresses auxiliary fan faults.
Certain drive types have an auxiliary fan built into the front cover as standard. If the fan is
sticking or disconnected, the control program first generates a warning A582, Auxiliary fan
missing, then a fault 5081, Auxiliary fan broken. If it is necessary to operate the drive without
the front cover (for example, during commissioning), this parameter can be activated to
temporarily suppress the fault.
Note:
•
The parameter must be activated within 2 minutes of control unit reboot (either by cycling
the power or by parameter 96.08).
•
The parameter only suppresses the fault, not the warning.
•
The parameter will be in effect until the auxiliary fan is reconnected and detected, or until
the next control unit reboot.
31.42
OVERCURRENT FAULT LIMIT
Sets a custom motor current fault limit.
The drive automatically sets an internal motor current limit according to the drive hardware.
The internal limit is appropriate in most cases, but this parameter can be used to set a lower
current limit, for example, to protect a permanent magnet motor from demagnetization.
With this parameter at 0.0 A, only the internal limit is in force. The default is 0.
GROUP 32
SUPERVISION
DESCRIPTION
32.01
SUPERVISION STATUS
Displays the status of the 3 Supervised signals. This is a 4 Bit Binary Display. 0000.
Bit 0 is Supervision 1 on the right. (Example: 0001 signifies that Supervision 1 is active)
Содержание PumpSmart PS220
Страница 1: ...Configuration Operation Manual PumpSmart Control Solutions PS220 v6 05...
Страница 5: ...PS220 Configuration Operation Guide PS220 4 Getting Started THIS PAGE IS INTENTIONALLY LEFT BLANK...
Страница 9: ...PS220 Configuration Operation Guide PS220 8 Basic Startup THIS PAGE IS INTENTIONALLY LEFT BLANK...
Страница 22: ...PS220 Configuration Operation Guide 21 PS220 SmartFlow...
Страница 40: ...PS220 Configuration Operation Guide 39 PS220 Process Control THIS PAGE IS INTENTIONALLY LEFT BLANK...
Страница 217: ...PS220 Configuration Operation Guide PS220 216 Functions Features This is an example of a typical Pump Performance Curve...
Страница 261: ...PS220 Configuration Operation Guide PS220 260 THIS PAGE IS INTENTIONALLY LEFT BLANK...
Страница 283: ...PS220 Configuration Operation Guide PS220 282 THIS PAGE IS INTENTIONALLY LEFT BLANK...
Страница 289: ...PS220 Configuration Operation Guide PS220 288 Ecodesign Regulation...
Страница 292: ...PS220 Configuration Operation Guide 291 PS220 Fuses heat dissipation chart...