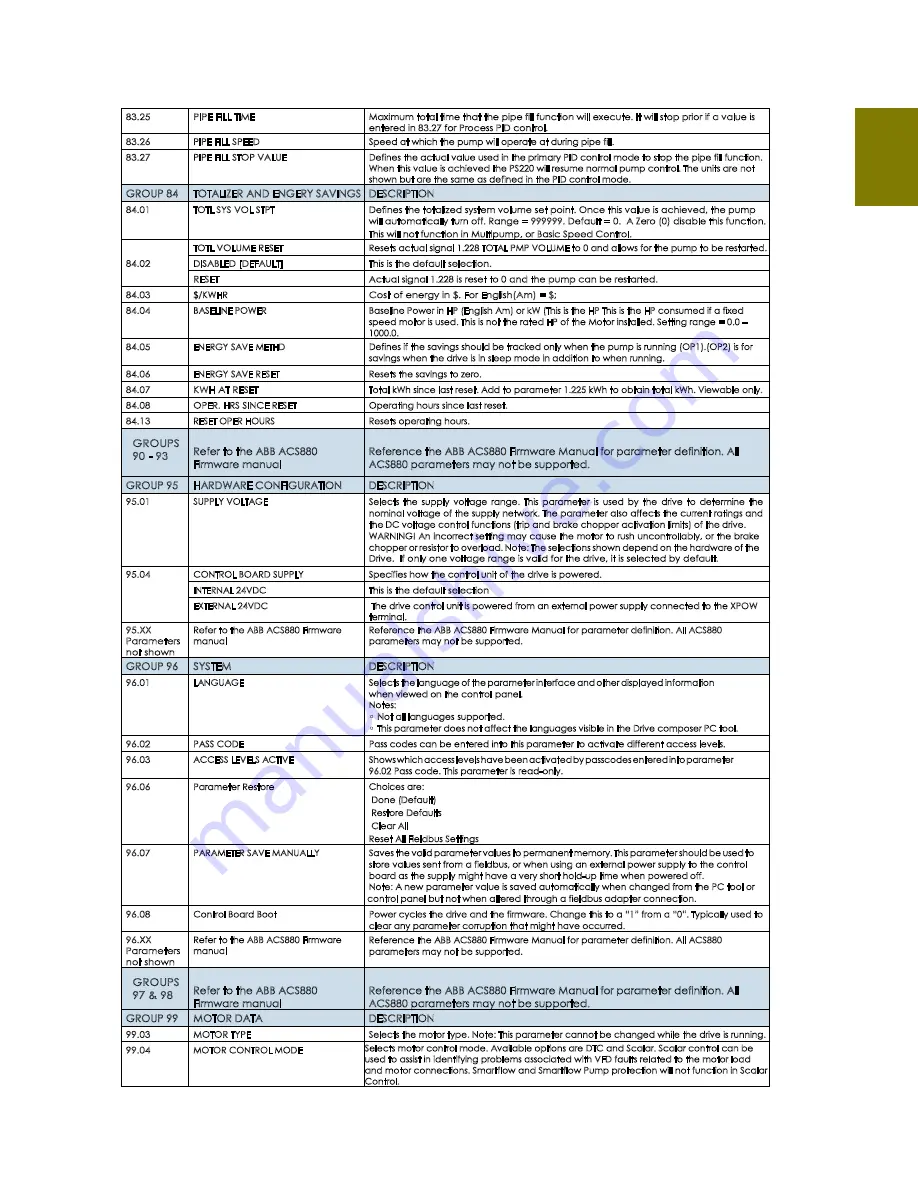
PS220 Configuration & Operation Guide
PS220 280
Parameter
Listing
83.25
PIPE FILL TIME
Maximum total time that the pipe fill function will execute. It will stop prior if a value is
entered in 83.27 for Process PID control.
83.26
PIPE FILL SPEED
Speed at which the pump will operate at during pipe fill.
83.27
PIPE FILL STOP VALUE
Defines the actual value used in the primary PID control mode to stop the pipe fill function.
When this value is achieved the PS220 will resume normal pump control. The units are not
shown but are the same as defined in the PID control mode.
GROUP 84 TOTALIZER AND ENGERY SAVINGS DESCRIPTION
84.01
TOTL SYS VOL STPT
Defines the totalized system volume set point. Once this value is achieved, the pump
will automatically turn off. Range = 999999. Default = 0. A Zero (0) disable this function.
This will not function in Multipump, or Basic Speed Control.
84.02
TOTL VOLUME RESET
Resets actual signal 1.228 TOTAL PMP VOLUME to 0 and allows for the pump to be restarted.
DISABLED [DEFAULT]
This is the default selection.
RESET
Actual signal 1.228 is reset to 0 and the pump can be restarted.
84.03
$/KWHR
Cost of energy in $. For English(Am) = $;
84.04
BASELINE POWER
Baseline Power in HP (English Am) or kW (This is the HP This is the HP consumed if a fixed
speed motor is used. This is not the rated HP of the Motor installed. Setting range = 0.0 –
1000.0.
84.05
ENERGY SAVE METHD
Defines if the savings should be tracked only when the pump is running (OP1).(OP2) is for
savings when the drive is in sleep mode in addition to when running.
84.06
ENERGY SAVE RESET
Resets the savings to zero.
84.07
KWH AT RESET
Total kWh since last reset. Add to parameter 1.225 kWh to obtain total kWh. Viewable only.
84.08
OPER. HRS SINCE RESET
Operating hours since last reset.
84.13
RESET OPER HOURS
Resets operating hours.
GROUPS
90 - 93
Refer to the ABB ACS880
Firmware manual
Reference the ABB ACS880 Firmware Manual for parameter definition. All
ACS880 parameters may not be supported.
GROUP 95 HARDWARE CONFIGURATION
DESCRIPTION
95.01
SUPPLY VOLTAGE
Selects the supply voltage range. This parameter is used by the drive to determine the
nominal voltage of the supply network. The parameter also affects the current ratings and
the DC voltage control functions (trip and brake chopper activation limits) of the drive.
WARNING! An incorrect setting may cause the motor to rush uncontrollably, or the brake
chopper or resistor to overload. Note: The selections shown depend on the hardware of the
Drive. If only one voltage range is valid for the drive, it is selected by default.
95.04
CONTROL BOARD SUPPLY
Specifies how the control unit of the drive is powered.
INTERNAL 24VDC
This is the default selection
EXTERNAL 24VDC
The drive control unit is powered from an external power supply connected to the XPOW
terminal.
95.XX
Parameters
not shown
Refer to the ABB ACS880 Firmware
manual
Reference the ABB ACS880 Firmware Manual for parameter definition. All ACS880
parameters may not be supported.
GROUP 96 SYSTEM
DESCRIPTION
96.01
LANGUAGE
Selects the language of the parameter interface and other displayed information
when viewed on the control panel.
Notes:
•
Not all languages supported.
•
This parameter does not affect the languages visible in the Drive composer PC tool.
96.02
PASS CODE
Pass codes can be entered into this parameter to activate different access levels.
96.03
ACCESS LEVELS ACTIVE
Shows which access levels have been activated by passcodes entered into parameter
96.02 Pass code. This parameter is read-only.
96.06
Parameter Restore
Choices are:
Done (Default)
Restore Defaults
Clear All
Reset All Fieldbus Settings
96.07
PARAMETER SAVE MANUALLY
Saves the valid parameter values to permanent memory. This parameter should be used to
store values sent from a fieldbus, or when using an external power supply to the control
board as the supply might have a very short hold-up time when powered off.
Note: A new parameter value is saved automatically when changed from the PC tool or
control panel but not when altered through a fieldbus adapter connection.
96.08
Control Board Boot
Power cycles the drive and the firmware. Change this to a “1” from a “0”. Typically used to
clear any parameter corruption that might have occurred.
96.XX
Parameters
not shown
Refer to the ABB ACS880 Firmware
manual
Reference the ABB ACS880 Firmware Manual for parameter definition. All ACS880
parameters may not be supported.
GROUPS
97 & 98
Refer to the ABB ACS880
Firmware manual
Reference the ABB ACS880 Firmware Manual for parameter definition. All
ACS880 parameters may not be supported.
GROUP 99 MOTOR DATA
DESCRIPTION
99.03
MOTOR TYPE
Selects the motor type. Note: This parameter cannot be changed while the drive is running.
99.04
MOTOR CONTROL MODE
Selects motor control mode. Available options are DTC and Scalar. Scalar control can be
used to assist in identifying problems associated with VFD faults related to the motor load
and motor connections. Smartflow and Smartflow Pump protection will not function in Scalar
Control.
Содержание PumpSmart PS220
Страница 1: ...Configuration Operation Manual PumpSmart Control Solutions PS220 v6 05...
Страница 5: ...PS220 Configuration Operation Guide PS220 4 Getting Started THIS PAGE IS INTENTIONALLY LEFT BLANK...
Страница 9: ...PS220 Configuration Operation Guide PS220 8 Basic Startup THIS PAGE IS INTENTIONALLY LEFT BLANK...
Страница 22: ...PS220 Configuration Operation Guide 21 PS220 SmartFlow...
Страница 40: ...PS220 Configuration Operation Guide 39 PS220 Process Control THIS PAGE IS INTENTIONALLY LEFT BLANK...
Страница 217: ...PS220 Configuration Operation Guide PS220 216 Functions Features This is an example of a typical Pump Performance Curve...
Страница 261: ...PS220 Configuration Operation Guide PS220 260 THIS PAGE IS INTENTIONALLY LEFT BLANK...
Страница 283: ...PS220 Configuration Operation Guide PS220 282 THIS PAGE IS INTENTIONALLY LEFT BLANK...
Страница 289: ...PS220 Configuration Operation Guide PS220 288 Ecodesign Regulation...
Страница 292: ...PS220 Configuration Operation Guide 291 PS220 Fuses heat dissipation chart...