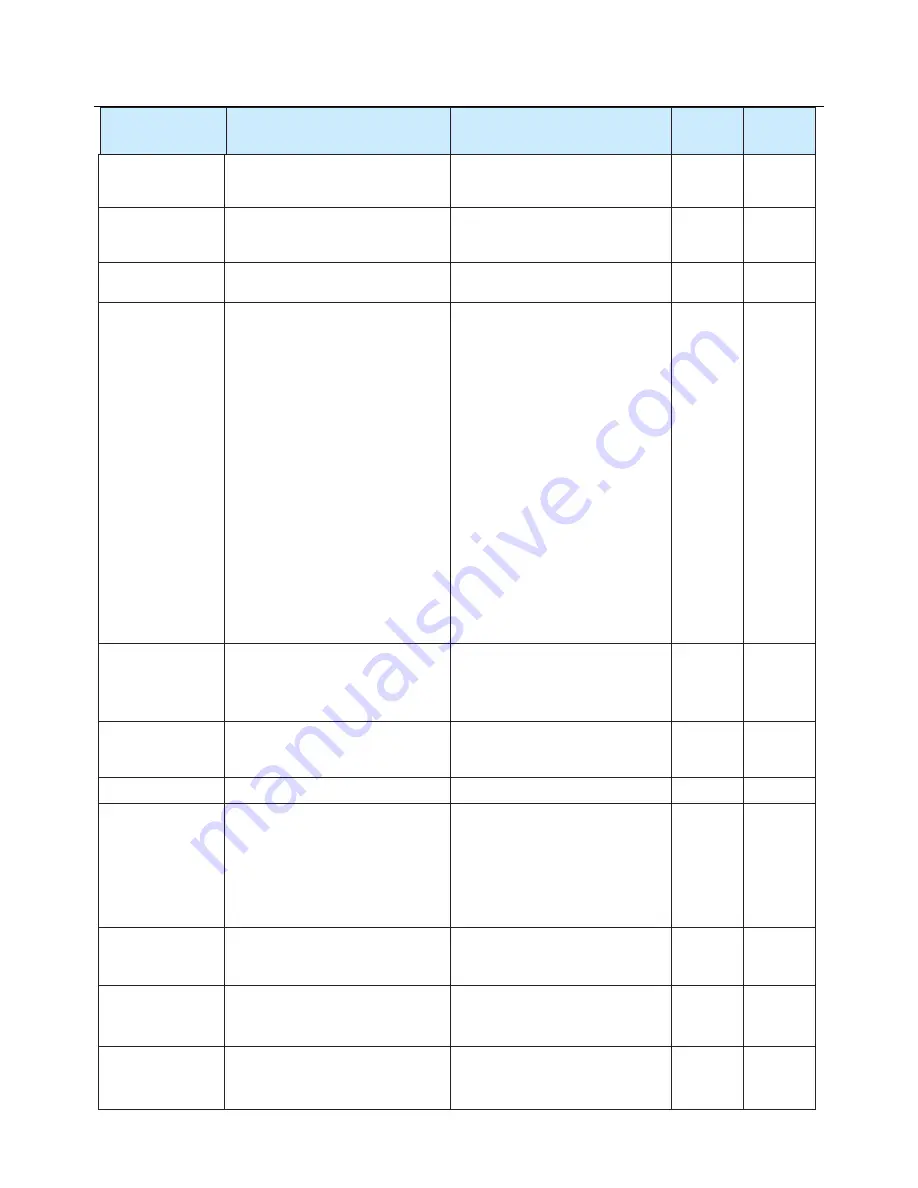
HV580L Series Frequency Inverter
32
Function
Code
Parameter Name
Setting Range
Default
Property
P0-04
Auxiliary frequency source Y
selection
The same as P0-03 (Main
frequency source X selection)
0
★
P0-05
Range of auxiliary frequency
Y for X and Y operation
0: Relative to maximum
frequency
1: Relative to main frequency X
0
☆
P0-06
Range of auxiliary frequency
Y for X and Y operation
0%
~
150%
100%
☆
P0-07
Frequency source selection
Unit's digit (Frequency source
selection)
0: Main frequency source X
1: X and Y operation
(operation relationship
determined by ten's digit)
2: Switchover between X and Y
3: Switchover between X and "X
and Y operation"
4: Switchover between Y and "X
and Y operation"
Ten's digit (X and Y operation
relationship)
0: X+Y 1: X-Y
2: Maximum
3: Minimum
00
☆
P0-08
Preset frequency
0.00 to maximum frequency
(valid when frequency source is
digital setting)
50.00Hz
☆
P0-09
Rotation direction
0: Same direction
1: Reverse direction
1: Reverse direction
0
☆
P0-10
Maximum frequency
50.00Hz
~
320.00Hz
50.00Hz
★
P0-11
Source of frequency upper limit
0: Set by F0-12
1: VS 1 2: AS 3: VS2
4: Pulse setting
5: Communication setting
0
★
P0-12
Frequency upper limit
Frequency lower limit (P0-14) to
maximum frequency (P0-10)
50.00Hz
☆
P0-13
Frequency upper limit offset
0.00 Hz to maximum frequency
(P0-10)
0.00Hz
☆
P0-14
Frequency lower limit
0.00 Hz to frequency upper limit
(P0-12)
0.00Hz
☆