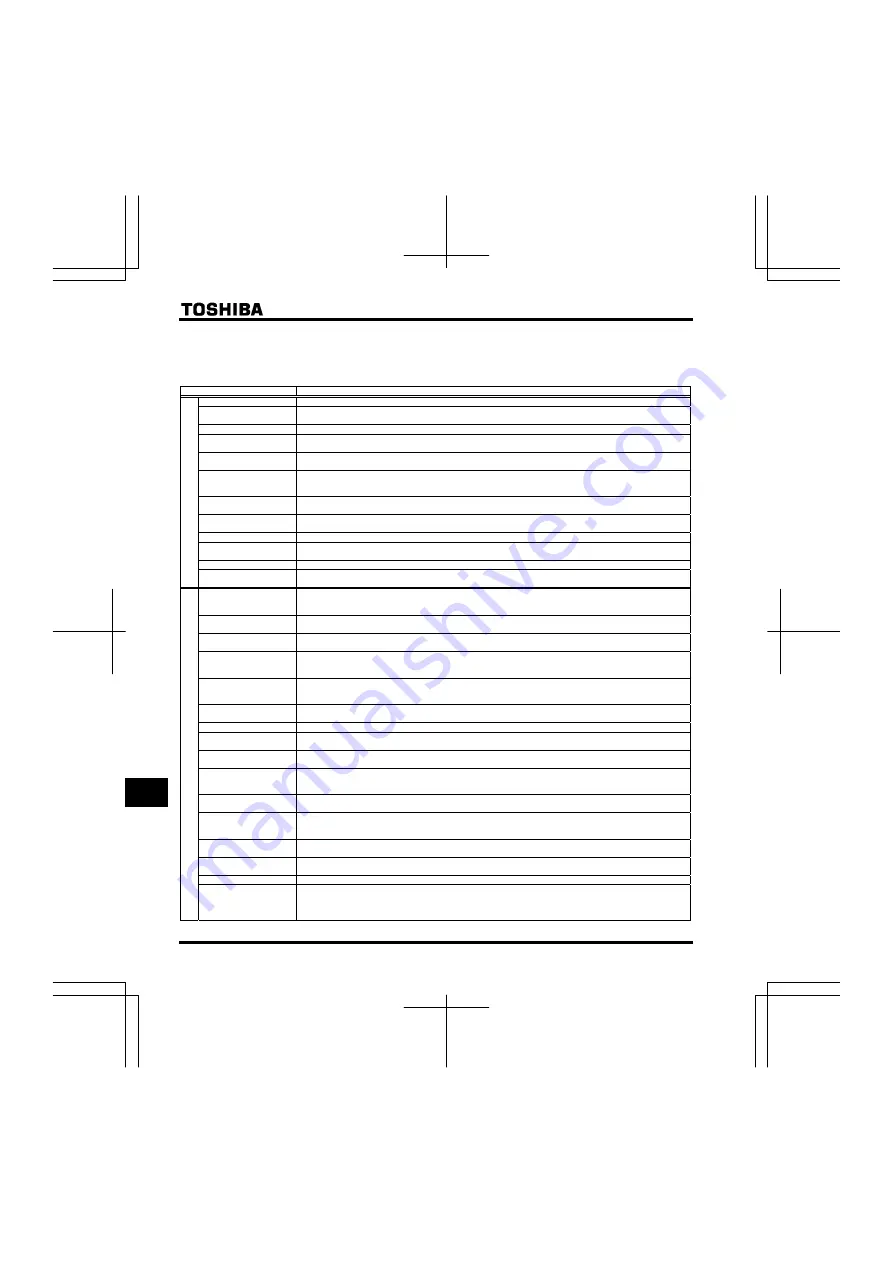
E6581611
L-2
12
Note 5. Required power supply capacity varies with the value of the power supply side inverter impedance (including those of
the input reactor and cables).
Common specification
Item Specification
Control system
Sinusoidal PWM control
Output voltage range
Note1)
Adjustable within the range of 50 to 330V (240V class) and 50 to 660V (500V class) by correcting the supply
voltage
Output frequency range
0.1 to 500.0Hz, default setting: 0.5 to 80Hz, maximum frequency: 30 to 500Hz
Minimum setting steps of
frequency
0.1Hz: analog input (when the max. frequency is 100Hz), 0.01Hz: Operation panel setting and communication
setting.
Frequency accuracy
Digital setting: within ±0.01% of the max. frequency (-10 to +60°C)
Analog setting: within ±0.5% of the max. frequency (25°C ±10°C)
Voltage/frequency
characteristics
V/f constant, variable torque, automatic torque boost, vector control, automatic energy-saving. dynamic automatic
energy-saving control (for fan and pump), PM motor control, V/F 5-point setting, Auto-tuning. Base frequency (20-
500Hz) adjusting to 1 & 2, torque boost (0-30%) adjusting to 1 & 2, adjusting frequency at start (0.1-10Hz)
Frequency setting signal
Setting dial on the front panel, external frequency potentiometer (connectable to a potentiometer with a rated
impedance of 1k-10k
Ω
), 0-10Vdc / -10-+10Vdc (input impedance: 30k
Ω
), 4-20mAdc (Input impedance: 250
Ω
).
Terminal block base
frequency
The characteristic can be set arbitrarily by two-point setting. Possible to set: analog input (VIA, VIB, VIC).
Frequency jump
Three frequencies can be set. Setting of the jump frequency and the range.
Upper- and lower-limit
frequencies
Upper-limit frequency: 0.5 to max. frequency, lower-limit frequency: 0 to upper-limit frequency
PWM carrier frequency
Adjustable range of 2.0k to 16.0kHz (default: 12.0kHz).
P
rinc
ip
al c
ont
ro
l f
unc
tions
PID control
Setting of proportional gain, integral gain, differential gain and control waiting time. Checking whether the amount of
processing amount and the amount of feedback agree.
Acceleration/deceleration
time
Selectable from among acceleration/deceleration times 1 & 2 & 3 (0.0 to 3600 sec.). Automatic
acceleration/deceleration function. S-pattern acceleration/deceleration 1 & 2 and S-pattern adjustable. Control of
forced rapid deceleration and dynamic rapid deceleration.
DC braking
Braking start-up frequency: 0 to maximum frequency, braking rate: 0 to 100%, braking time: 0 to 25.5 seconds,
emergency DC braking, motor shaft fixing control.
Dynamic Braking Drive
Circuit
Control and drive circuit is built in the inverter with the braking resistor outside (optional).
Input terminal function
(programmable)
Possible to select from among about 110 functions, such as forward/reverse run signal input, jog run signal input,
operation base signal input and reset signal input, to assign to 8 input terminals. Logic selectable between sink and
source.
Output terminal functions
(programmable)
Possible to select from among about 150 functions, such as upper/lower limit frequency signal output, low speed
detection signal output, specified speed reach signal output and failure signal output, to assign to FL relay output,
open collector output terminal, and RY output terminals.
Forward/reverse run
The RUN and STOP keys on the operation panel are used to start and stop operation, respectively.
Forward/reverse run possible through communication and logic inputs from the terminal block.
Jog run
Jog mode, if selected, allows jog operation from the terminal block and also from remote keypad.
Preset speed operation
Frequency refe 15-speed operation possible by changing the combination of 4 contacts on the terminal
block.
Retry operation
Capable of restarting automatically after a check of the main circuit elements in case the protective function is
activated. 10 times (Max.) (selectable with a parameter)
Various prohibition settings
/ Password setting
Possible to write-protect parameters and to prohibit the change of panel frequency settings and the use of operation
panel for operation, emergency stop or resetting. Possible to write-protect parameters by setting 4 digits password
and terminal input.
Regenerative power ride-
through control
Possible to keep the motor running using its regenerative energy in case of a momentary power failure (default:
OFF).
Auto-restart operation
In the event of a momentary power failure, the inverter reads the rotational speed of the coasting motor and outputs
a frequency appropriate to the rotational speed in order to restart the motor smoothly. This function can also be
used when switching to commercial power.
Light-load high-speed
operation
Increases the operating efficiency of the machine by increasing the rotational speed of the motor when it is operated
under light load.
Drooping function
When two or more inverters are used to operate a single load, this function prevents load from concentrating on one
inverter due to unbalance.
Override function
External input signal adjustment is possible to the operation frequency command value.
O
per
at
ion s
pec
ific
at
ions
Relay output signal
1c- contact output and 1a- contact output Note2)
Maximum switching capacity : 250Vac-2A , 30Vdc-2A (At resistive load cos
Φ
=1),
250Vac-1A (cos
Φ
=0.4) , 30Vdc-1A (L/R=7ms)
Minimum permissible load : 5Vdc-100mA, 24Vdc-5mA
<Continued overleaf>
Summary of Contents for Q9 Plus ASD
Page 5: ...TM Q9 Plus Bypass ASD Bypass Box INSTALLATION OPERATION MANUAL June 2013 DN 68251 000 ...
Page 61: ...Q9 PLUS ASD LOW VOLTAGE DRIVE ...
Page 65: ...S15 ASD LOW VOLTAGE DRIVE ...
Page 80: ...E6581611 iv 15 Warranty O 1 16 Disposal of the inverter P 1 ...
Page 429: ......
Page 430: ......