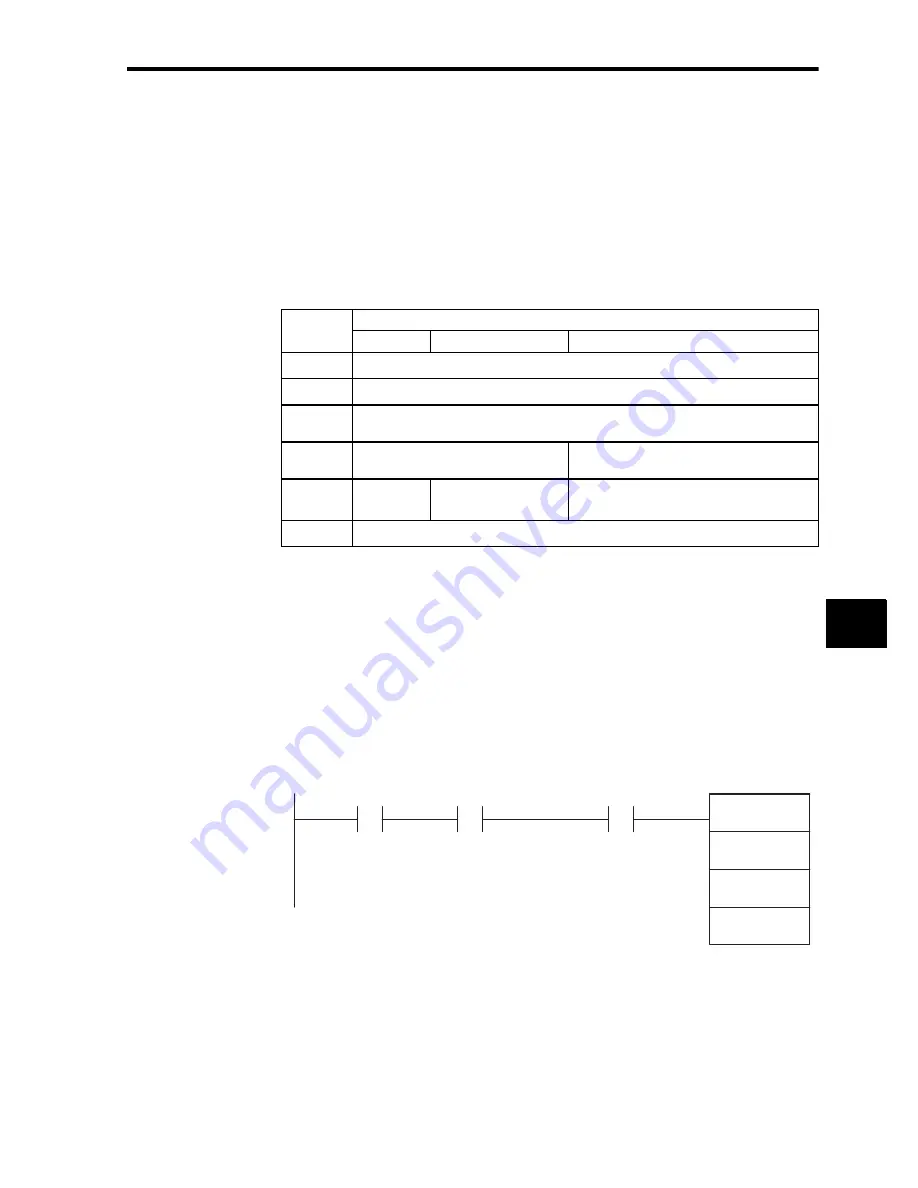
6.8 Communications Using Explicit Messages
6-69
6
D: First Response Word at Local Node
Specify the beginning word of the area for storing responses to messages.
C: First Control Data Word
Specify the beginning word for storing the control data required for message communica-
tions. Preset in consecutive words the required data, as shown below. This data is required
by the DeviceNet Master Unit.
* 1. Set the number of words from the beginning word S.
* 2. Set the number of words from the beginning word D.
* 3. Set the number of retries when there is an error response.
* 4. For Explicit Messages, this must be set to at least 2 s.
* 5. Set bit 15 of word C+4 to 0 (response returned) or 1 (response). For
Explicit Messages, this bit must be set to 0 (response returned).
Message Timing
When executing CMND, an AND condition must be set for the ON status of the SYSMAC’s
Network Communications Enabled Flag (A20200 to A20207) and the Master Unit’s Mes-
sage Communications Enabled Flag [bit 12 of word (25
×
unit 1542)].
Word
Bits
15
14 to 8
7 to 0
C
Number of command data bytes
∗
1
: 0000 to 021E Hex (0 to 542 bytes)
C+1
Number of response data bytes
∗
2
: 0000 to 021E Hex (0 to 542 bytes)
C+2
Destination network address: 0000 to 007F Hex (0 to 127), 0000 Hex
(local network)
C+3
Destination node address: 00 to 3F Hex
(0 to 63)
Destination unit address:
10 to 1F Hex
C+4
Response
∗
5
Communications port
No.: 00 to 07
Number of retries
∗
3
: 00 to 0F Hex
(0 to 15 times)
C+5
Response monitor time
∗
4
: 0000 Hex (2 s), 0001 to FFFF Hex (0.1 to 6,553.5 s (Unit: 0.1 s)
(@)CMND
S
D
C
Message Communications
Enabled Flag
Execution
condition
Network Communications
Enabled Flag
Summary of Contents for OMNUC W R88A-NCW152-DRT
Page 1: ...Cat No I538 E3 1 DeviceNet Option Unit OMNUC W Series Model R88A NCW152 DRT...
Page 53: ...4 Connectors 4 5 3 DeviceNet Network Configuration Restrictions 4 22 4...
Page 97: ...5 Parameter Settings 5 3 8 Notch Signal Output Positioning 5 44 5...
Page 211: ...8 Servo Driver Settings 8 5 3 Absolute Encoder Multi turn Limit Setting 8 24 8...
Page 257: ...9 Troubleshooting 9 46 9...