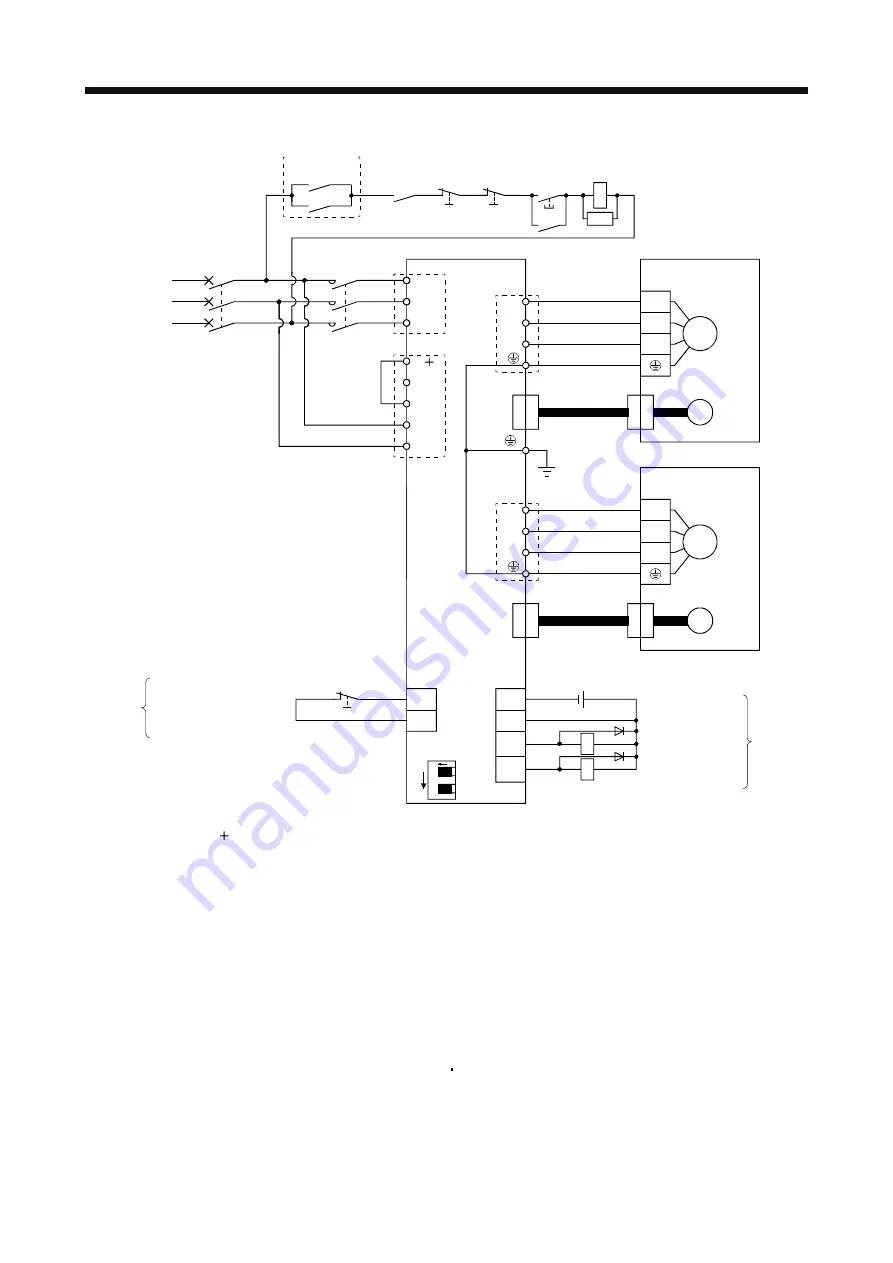
3. SIGNALS AND WIRING
3 - 3
(Note 5)
Servo amplifier
(Note 9)
Power
supply
CNP1
CNP2
(Note 5)
CN2A
CNP3B
CN2B
CN3
CN3
CNP3A
PE( )
24VDC
(Note 4)
A-axis malfunction
(Note 3)
B-axis malfunction
(Note 3)
L
1
L
2
L
3
P
L
11
L
21
D
C
(Note 1)
A-axis servo motor
U
V
W
M
Motor
Encoder
(Note 2)
Encoder cable
EM1
DOCOM
(Note 4)
ALM-A
DICOM
DOCOM
U
V
W
M
Motor
ALM-B
RA1
RA2
MC
MCCB
OFF
MC
ON
RA3
RA1(A-axis)
RA2(B-axis)
Controller
forced stop
Forced stop
(Note 6)
Malfunction
SK
SW3 (Note 7)
ON
A-axis
B-axis
2
1
Fro
n
t s
ide
(Note 8)
B-axis servo motor
(Note 2)
Encoder cable
Encoder
U
V
W
U
V
W
(Note 3)
MC
(Note 6) Forced stop
(Note 10)
(Note 10)
Note 1. Always connect P and D. When using the regenerative option, refer to section 11.2.
2. For the encoder cable, use of the option cable is recommended. Refer to section 11.1 for selection of the cable.
3. If deactivating output of malfunction (ALM-A/ALM-B) with parameter change, configure up the power supply circuit which switches
off the magnetic contactor after detection of alarm occurrence on the controller side. In this connection example, the operation
continues in the other axis when an alarm occurs in the A-axis or the B-axis. To stop both axes in an alarm occurrence, connect
RA1 and RA2 in series.
4. For the sink I/O interface. For the source I/O interface, refer to section 3.7.3.
5. For the power line connection, refer to section 3.10.
6. Configure the circuit to shut down the main circuit power supply simultaneously with the turn off of forced stop (EM1) using the
external sequence.
7. This connection example is a connection using a rotary servo motor. Turn SW3 off (factory setting). (Refer to section 3.14.)
8. Be sure to use a magnetic contactor with an operation delay time of 80ms or less. The operation delay time is the time interval
between current being applied to the coil until closure of contacts.
9. For 1-phase 200V to 230VAC, connect the power supply to L
1
L
2
and leave L
3
open. Refer to section 1.3 for the power supply
specification.
10. Connecting a servo motor for different axis to the CNP3A or CNP3B connector may cause a malfunction.
Summary of Contents for MELSERVO-J3W Series
Page 17: ...8 MEMO ...
Page 27: ...1 FUNCTIONS AND CONFIGURATION 1 10 MEMO ...
Page 87: ...4 STARTUP 4 14 MEMO ...
Page 117: ...5 PARAMETERS 5 30 MEMO ...
Page 129: ...6 GENERAL GAIN ADJUSTMENT 6 12 MEMO ...
Page 185: ...10 CHARACTERISTICS 10 8 MEMO ...
Page 241: ...11 OPTIONS AND AUXILIARY EQUIPMENT 11 56 MEMO ...
Page 274: ...13 USING A LINEAR SERVO MOTOR 13 25 1 2 3 4 ...