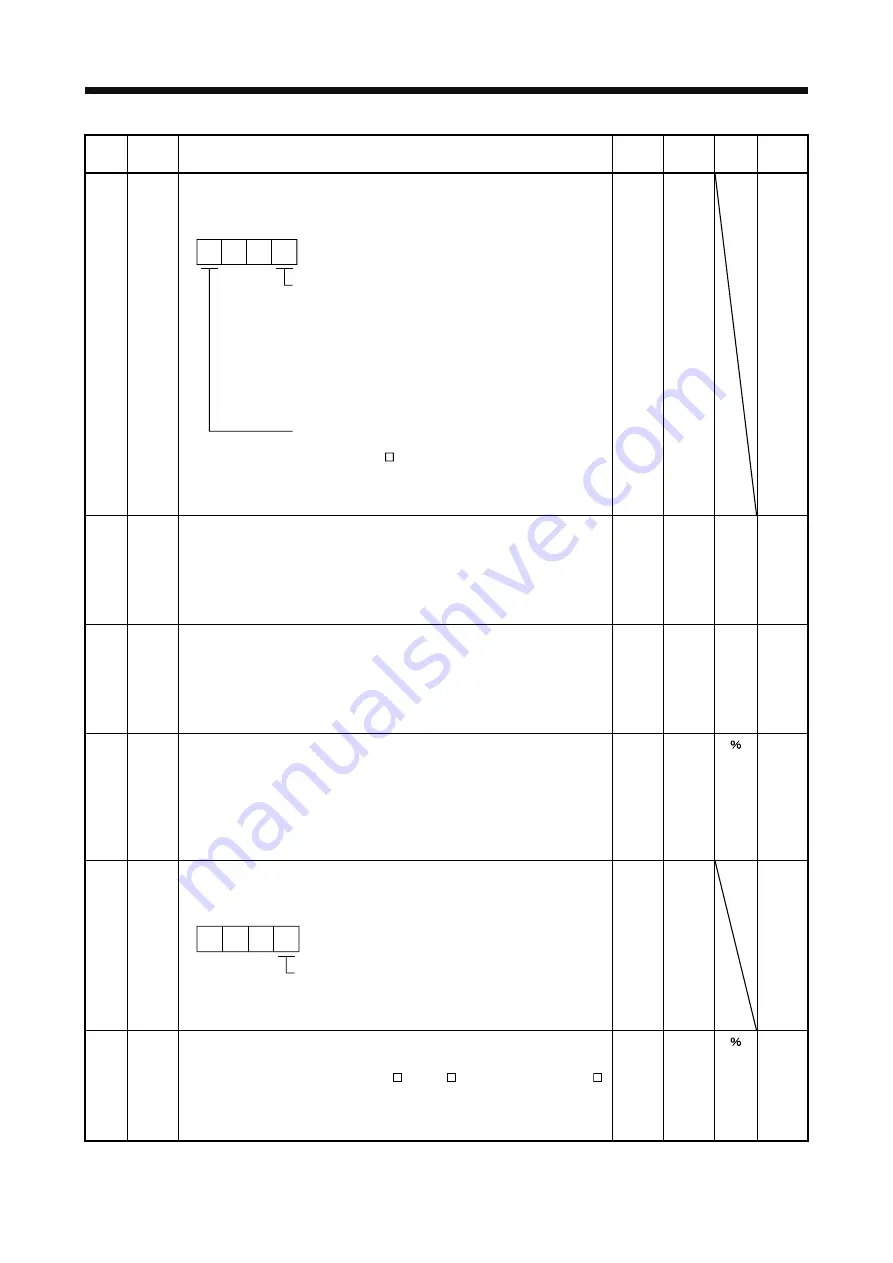
13. USING A LINEAR SERVO MOTOR
13 - 55
No. Symbol
Name
Setting
Factory
setting
Unit
Setting
range
PS04
*LIT2 Linear function selection 2
Linear servo motor control error detection function and linear servo motor control
error reset can be selected.
Linear servo motor control error detection function selection
(Refer to section 13.5.6 (1).)
0: Invalid
1: Position deviation error detection valid
2: Speed deviation error detection valid
3: Position/speed detection deviation error detection valid
4: Thrust deviation error detection valid
5: Position/thrust deviation error detection valid
6: Speed/thrust deviation error detection valid
7: Position/speed/thrust deviation error detection valid
Linear servo motor control error detection reset selection
Set the controller reset condition of the linear servo motor
control error (42. ).
0: Reset impossible (Reset by switching OFF is possible.)
1: Reset possible
0 0
Each
axis
0003h Refer
to
name
and
function
column.
PS05
LB1
Linear servo motor control position deviation error detection level
Used to set the position deviation error detection level of the linear servo motor
control error detection. When the difference between the model feedback position
and the feedback position is bigger than this setting value, the linear servo motor
control error (42.1). (Refer to section 13.5.6 (1).)
When "0" is set in this parameter, 50mm is set for detection level.
Each
axis
0 mm 0
to
1000
PS06
LB2
Linear servo motor control speed deviation error detection level
Used to set the speed deviation error detection level of the linear servo motor
control error detection. When the difference between the model feedback speed
and the feedback speed is bigger than this setting value, the linear servo motor
control error is detected (42.2). (Refer to section 13.5.6 (1).)
When "0" is set in this parameter, 1000mm/s is set for detection level.
Each
axis
0 mm/s
0
to
5000
PS07
LB3
Linear servo motor control thrust deviation error detection level
Used to set the thrust deviation error detection level of the linear servo motor
control error detection. When the difference between the command thrust and the
feedback thrust is bigger than this setting value, the linear servo motor control
error is detected (42.3). (Refer to section 13.5.6 (1).)
When "0" is set in this parameter, the factory setting is applied in the servo
amplifier.
Each
axis
100
0
to
1000
PS08
*LIT3 Linear function selection 3
The magnetic pole detection method can be selected. (Refer to section 13.5.2
(6).)
Selection of magnetic pole
0: Detection method
4: Minute position detection method
0 1
0
Each
axis
0010h Refer
to
name
and
function
column.
PS09 LPWM Magnetic pole detection voltage level
Used to set the direct current exciting voltage level during the magnetic pole
detection. When the overload alarm (50. and 51. ) or overcurrent alarm (32. )
occurs, set the smaller value. When the initial magnetic pole detection error
occurs during the magnetic pole detection, set the bigger value. (Refer to section
13.5.2 (3).)
Each
axis
30
0
to
100
Summary of Contents for MELSERVO-J3W Series
Page 17: ...8 MEMO ...
Page 27: ...1 FUNCTIONS AND CONFIGURATION 1 10 MEMO ...
Page 87: ...4 STARTUP 4 14 MEMO ...
Page 117: ...5 PARAMETERS 5 30 MEMO ...
Page 129: ...6 GENERAL GAIN ADJUSTMENT 6 12 MEMO ...
Page 185: ...10 CHARACTERISTICS 10 8 MEMO ...
Page 241: ...11 OPTIONS AND AUXILIARY EQUIPMENT 11 56 MEMO ...
Page 274: ...13 USING A LINEAR SERVO MOTOR 13 25 1 2 3 4 ...