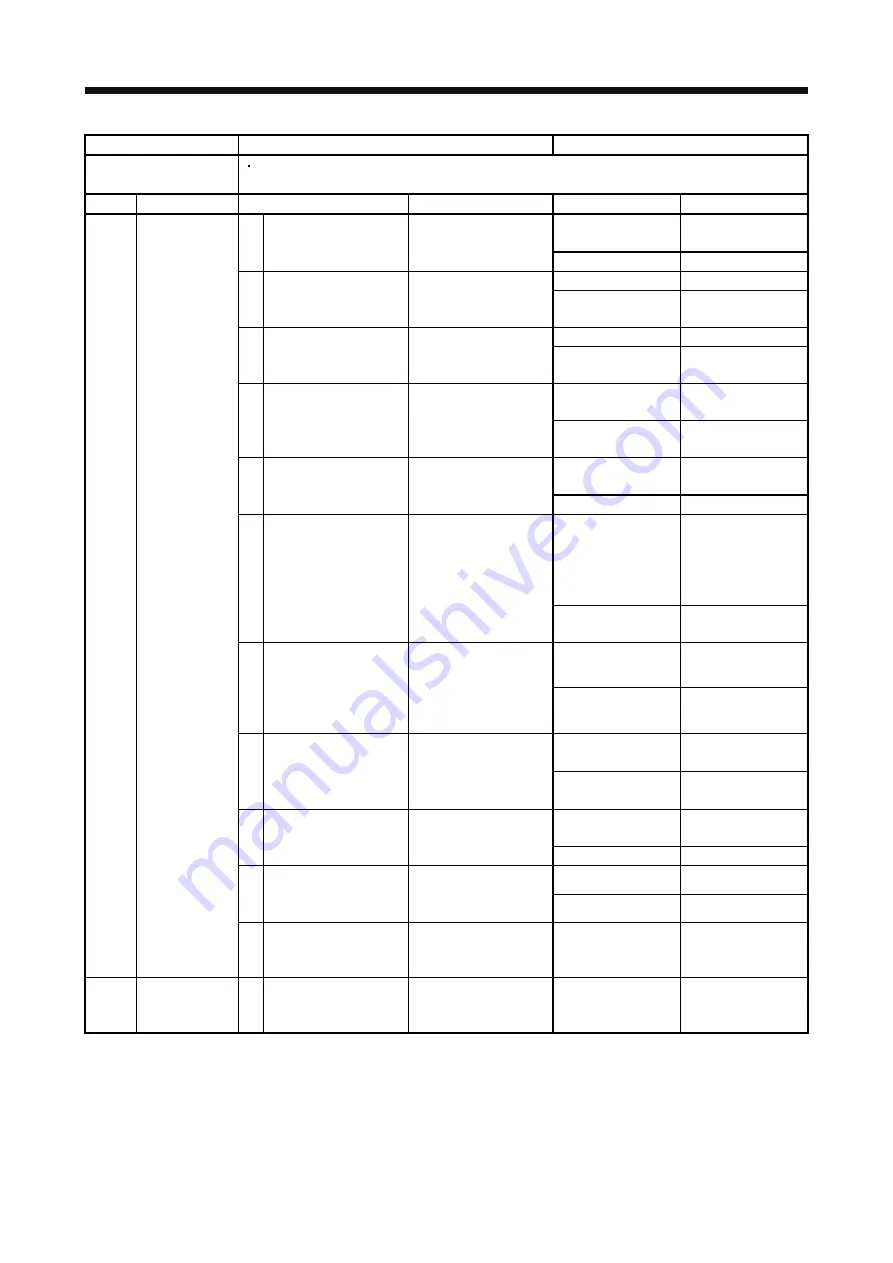
8. TROUBLESHOOTING
8 - 26
Alarm No.52
Name: Error excessive
Stop method: Corresponding axis stops
Alarm description
The droop pulses existing between the model position and the actual servo motor position exceeds the
alarm level.
Display Name
Cause
Checkpoint
Finding
Action
52.3 Excess
droop
pulse
(1) Power cable is cut.
Check the power cable.
No connection (open
phase).
Modify the wiring.
No problem found.
Check (2).
(2)
Misconnection found.
Modify the wiring.
Misconnection of the
servo motor.
Check the connection of
U, V and W phases.
Misconnection not
found.
Check (3).
(3)
Misconnection found.
Modify the wiring.
Misconnection of encoder
cable.
Check the axis where
encoder cable is
connected.
Misconnection not
found.
Check (4).
(4) Torque limit value is too
small.
Check the torque limit
value.
Torque limit value is
small.
Increase the torque
limit value.
Within the setting
range.
Check (5).
(5)
Machine
struck
something.
Check if the machine
struck something.
Struck.
Review the operation
pattern.
Did not strike.
Check (6).
(6) Torque shortage.
Check if the torque is
saturated.
Torque is saturated.
Reduce load.
Check operation
pattern.
Use servo motor that
provides larger output.
Torque is not
saturated.
Check (7).
(7)
Check the bus voltage
using MR Configurator .
Bus voltage is low.
Review the power
supply voltage.
Equipment cannot be
started because of torque
shortage caused by the
power supply voltage
drop.
Bus voltage is high.
Check (8).
(8)
Not reproduced.
Review the operation
pattern.
Acceleration/deceleration
time constant is too
small.
Set acceleration/
deceleration time longer,
and check the
reproducibility of the error.
Reproduced. Check
(9).
(9) Position loop gain is too
small.
Not reproduced.
Review the position
loop gain.
Change the position loop
gain, and check the
reproducibility of the error. Reproduced. Check
(10).
(10)
Motor moves.
Check the machine.
Servo motor shaft is
rotated by external force.
Measure the actual servo
motor position in the
servo lock status.
Does not move.
Check (11).
(11) Encoder is faulty.
Replace the servo motor
and check the
reproducibility of the error.
Alarm does not occur. Replace the servo
motor.
52.4 Maximum
deviation at 0
torque limit
(1) Torque limit is set to 0.
Check the torque limit
value.
Torque limit is 0.
Increase the torque
limit value.
Summary of Contents for MELSERVO-J3W Series
Page 17: ...8 MEMO ...
Page 27: ...1 FUNCTIONS AND CONFIGURATION 1 10 MEMO ...
Page 87: ...4 STARTUP 4 14 MEMO ...
Page 117: ...5 PARAMETERS 5 30 MEMO ...
Page 129: ...6 GENERAL GAIN ADJUSTMENT 6 12 MEMO ...
Page 185: ...10 CHARACTERISTICS 10 8 MEMO ...
Page 241: ...11 OPTIONS AND AUXILIARY EQUIPMENT 11 56 MEMO ...
Page 274: ...13 USING A LINEAR SERVO MOTOR 13 25 1 2 3 4 ...