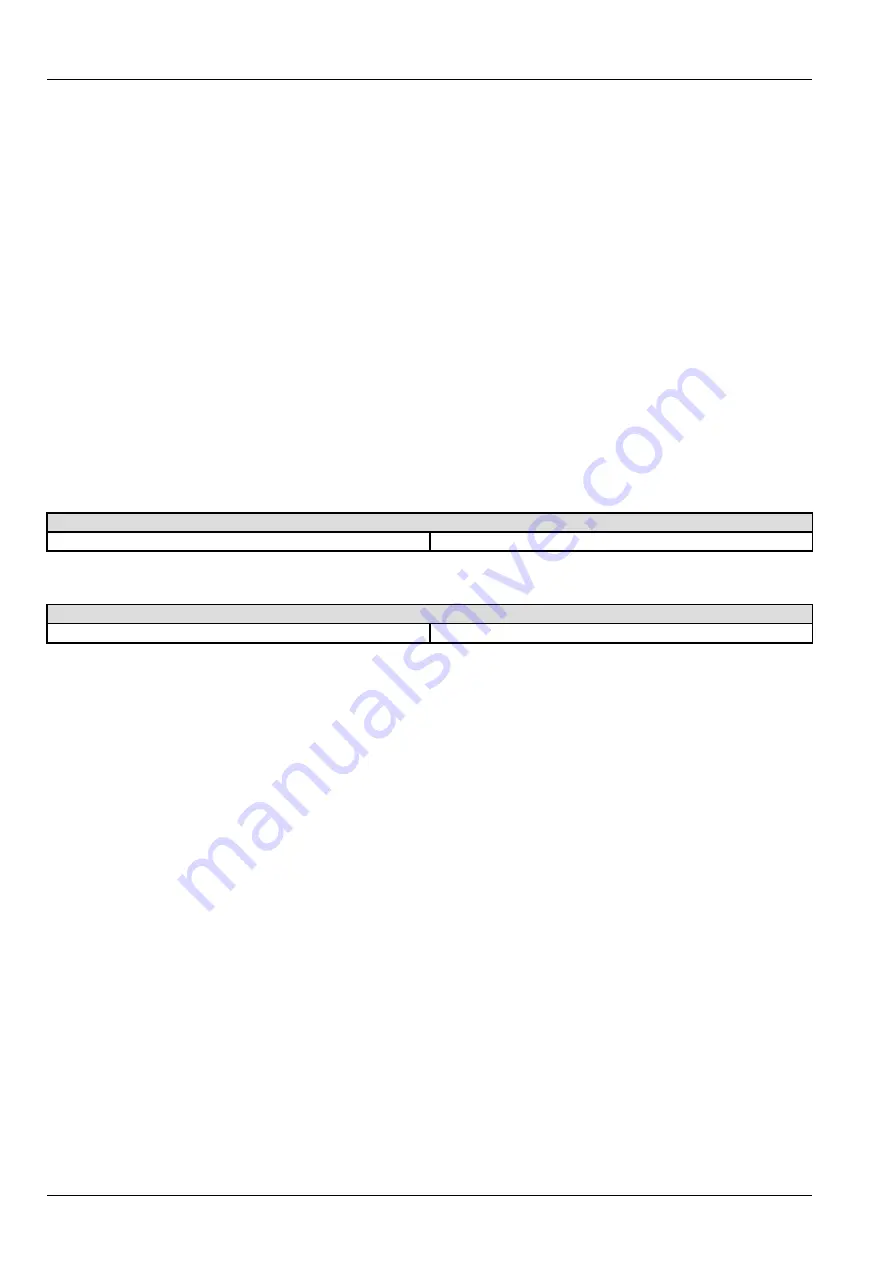
7 - MAINTENANCE
Cleaning the batteries
Check the batteries and battery compartment regularly
for dirt, corrosion and damage. Dirt mixed with elec-
trolyte or moisture on the top of the batteries can cause
a discharged condition in the batteries. Use one of the
following methods to clean the batteries.
• Use CASE CONSTRUCTION Battery Saver. Follow
the instructions on the container. This cleaner does
not need water.
If CASE CONSTRUCTION Battery Saver is unavail-
able, use other special cleaners to prevent corrosion
on the battery terminals.
Alternator and starter motor
Have your authorized dealer check the alternator and
starter motor.
Do not use steam cleaning equipment or a cleaning sol-
vent to clean these components.
Alternator
Service specification
Check
Every 1000 hours
Starter motor
Service specification
Check
Every 1000 hours
7-102
Содержание 2050M
Страница 22: ...1 GENERAL INFORMATION 1 16 ...
Страница 106: ...4 OPERATING INSTRUCTIONS 21 Check the controls for correct operation 4 4 ...
Страница 136: ...5 TRANSPORT OPERATIONS 5 14 ...
Страница 196: ...7 MAINTENANCE RAIL13DOZ1597GA 1 7 40 ...
Страница 197: ...7 MAINTENANCE RAIL13DOZ1598GA 2 7 41 ...
Страница 198: ...7 MAINTENANCE RAIL13DOZ0003GA 3 7 42 ...
Страница 242: ...7 MAINTENANCE 12 Close and lock the right hand side front access panel RAIL13DOZ0776AA 12 7 86 ...
Страница 264: ...7 MAINTENANCE RAIL12DOZ1024FA 2 7 108 ...
Страница 265: ...7 MAINTENANCE RAIL13DOZ1526GA 3 7 109 ...
Страница 267: ...7 MAINTENANCE Key Fuse function Amperage 7 Ignition 24V 50 A 8 Telematics 10 A 9 UCM 20 A 10 SCR 20 A 7 111 ...