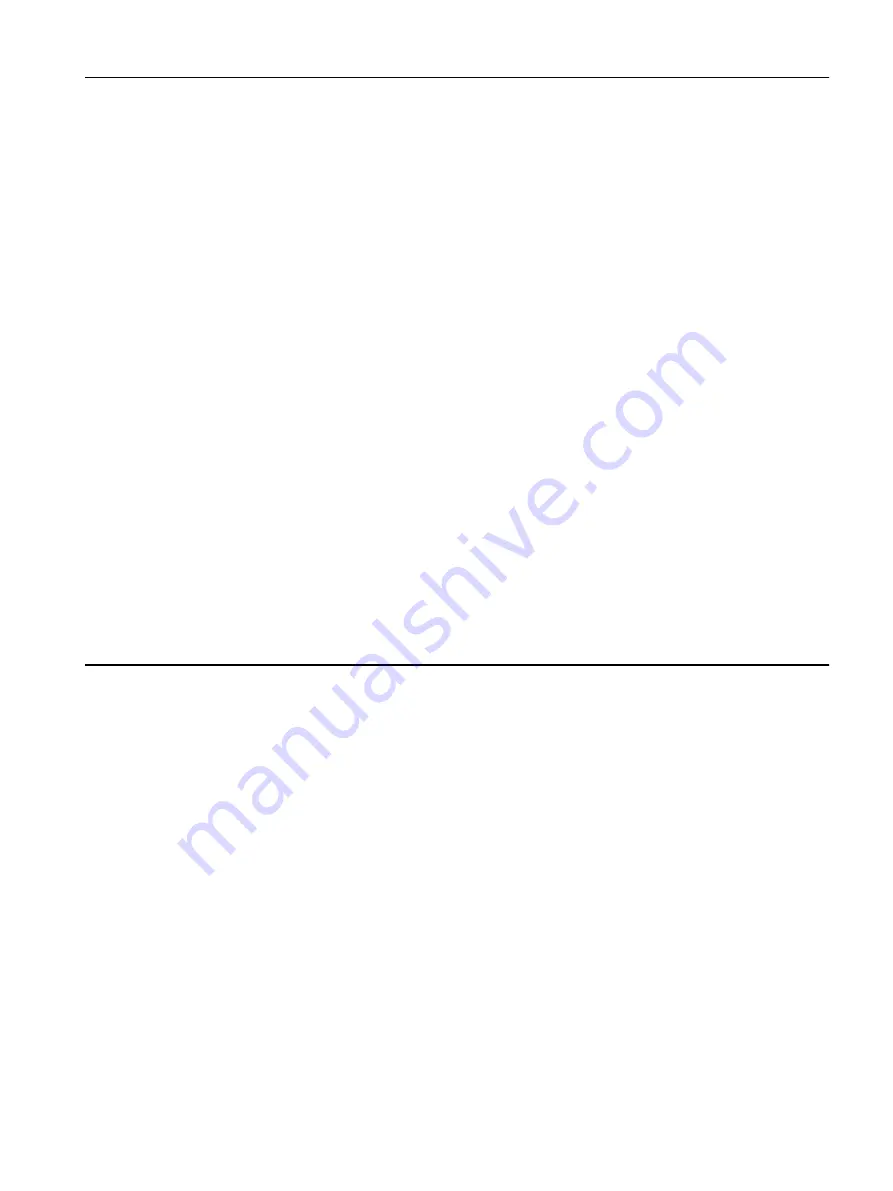
Cause:
The safe brake test was canceled as a result of a fault.
Alarm value (r2124, interpret binary):
Bit 17 = 1: fault in the brake test sequence (cause, see bits 0 ... 10).
Bit 20 = 1: the brake is not opened (p10202).
Bit 21 = 1: axis position during the brake test not valid due to parking axis.
Bit 22 = 1: internal software error.
Bit 23 = 1: the permissible position range of the axis was violated with the brake closed (p10212/p10222).
Bit 24 = 1: the tested internal brake was opened while the brake test was active.
Bit 26 = 1: during the active brake test, the test torque left its tolerance bandwidth (20 %).
Cause for alarm value bit 17:
Bit 0 = 1: operation when selecting the brake test not enabled (r0899.2 = 0).
Bit 1 = 1: external fault occurred (e.g. the brake test that has already started is canceled by the user).
Bit 2 = 1: when selecting the brake test a brake is closed.
Bit 3 = 1: when determining the load torque a brake is closed.
Bit 4 = 1: a fault with a stop response has occurred (e.g. OFF1, OFF2 or OFF3) - or pulse enable was withdrawn (e.g.
STO selected or operation no longer enabled).
Bit 5 = 1: when selecting the brake test the axis speed setpoint is too high.
Bit 6 = 1: the actual speed (r0063) of the axis is too high (e.g. brake does not hold during the brake test).
Bit 8 = 1: closed-loop control not enabled or function generator active.
Bit 9 = 1: control does not switch over to the brake test (e.g. because PI speed control has not been parameterized).
Bit 10 = 1: torque limit reached (r1407.7, r1408.8).
Note:
SBT: Safe Brake Test
Remedy:
- remove the fault cause.
- carry out a safe acknowledgment.
- if required, restart the brake test.
For bit 17 = 1 with bit 6 = 1 or bit 23 = 1:
If the brake closing time of the motor holding brake (p1217) has been set too low, then at the start of the brake test, the
brake is closed too late. The brake closing time should be adapted (p1217).
A01785
SBT brake test configuration error
Message value:
%1
Drive object:
All objects
Reaction:
NONE
Acknowledge:
NONE
Cause:
Error when parameterizing the brake test.
In this configuration, the brake test cannot be started or cannot be started without error.
Alarm value (r2124, interpret decimal):
1:
No motion monitoring functions have been enabled.
4:
No brake was configured (p10202).
8:
The brake test is configured for an internal brake, however the safety brake control is not enabled (p9602).
16:
The safe brake test and Safety without encoder are simultaneously enabled (p9306/p9506). This is not permissible.
Note:
SBT: Safe Brake Test
Remedy:
Check parameterization of the brake test.
Faults and alarms
13.2 List of faults and alarms
SINAMICS S210 servo drive system
Operating Instructions, 12/2017, A5E41702836B AA
391
Summary of Contents for SIMOTICS S-1FK2
Page 2: ......
Page 766: ...Index SINAMICS S210 servo drive system 764 Operating Instructions 12 2017 A5E41702836B AA ...
Page 767: ......