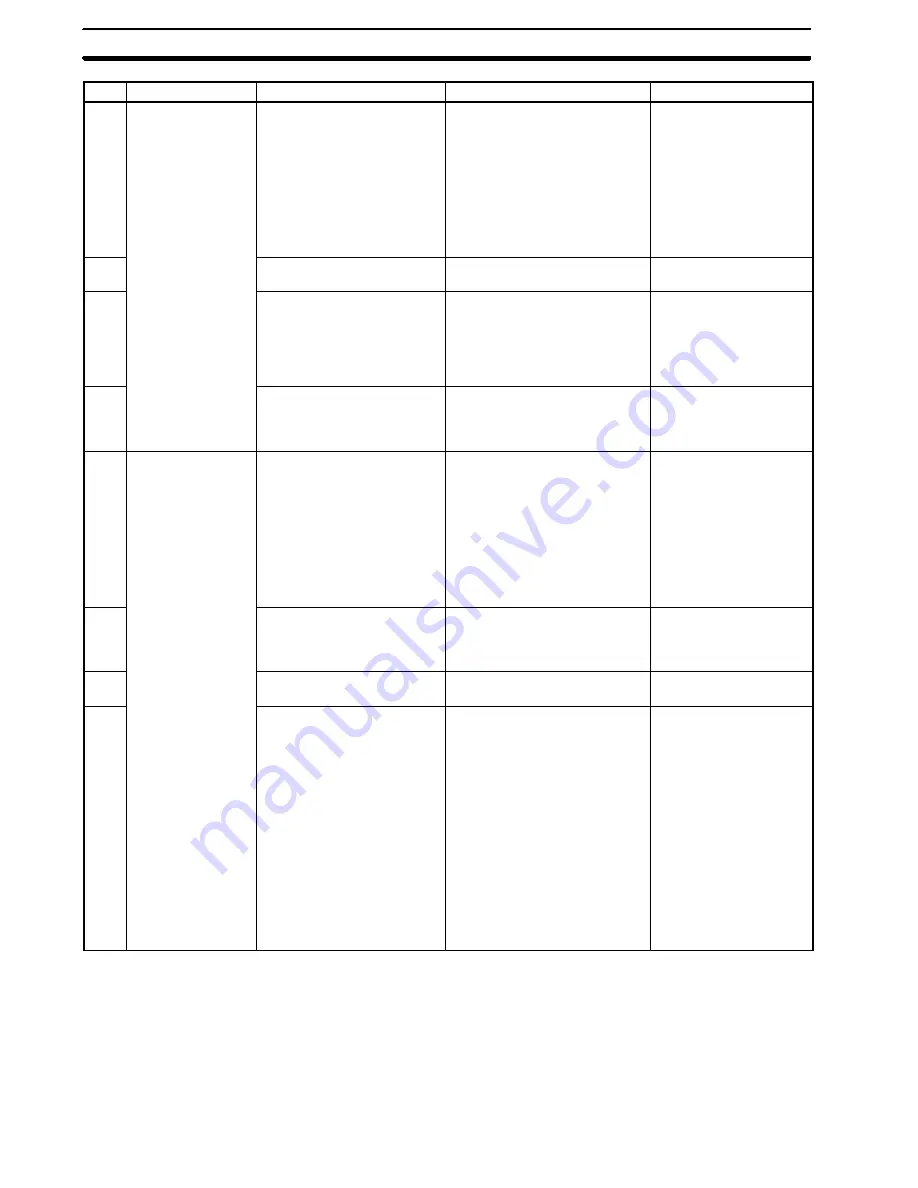
11-1
Section
Troubleshooting Tables
280
No.
Remedy
Items to check
Probable causes
Problem
33
Rotation is
reversed.
The Servo Drive is set for
reverse rotation.
If JOG operation is executed
and the direction is the opposite
of the JOG direction, check
whether the Servo Drive is set
for reverse rotation. Also, check
that the feedback signals
(A-phase/B-phase) are not
reversed and that operation is
not set for reverse in the
parameters.
Correct the setting for
the direction of Servo
Drive rotation.
34
The CW and CCW pulse
output signals are reversed.
Check the wiring for the CW
and CCW pulse output signals.
Correct the wiring.
35
During an origin search the
origin proximity sensor
polarity does not match the
parameter setting (in the
PCU) for the origin proximity
input polarity.
Check the parameter setting
and the sensor polarity.
Correct the parameter
setting.
36
During an origin search, the
origin proximity input wiring is
faulty.
Check the that the origin
proximity input signal in the
operating memory area is
turning ON and OFF.
Correct the origin
proximity input wiring.
37
The positioning
completed signal is
not output or is
delayed. (The next
operation cannot
be started.)
The Servo Drive’s in-position
width set in the PCU
parameters is too narrow,
and the axis is not in the
in-position range. (If it is not
in the in-position range, the
next operation cannot be
started because the
preceding operation is not
completed.)
---
Increase the in-position
width set in the PCU
parameters.
38
The wiring for the Servo
Drive’s positioning completed
signal is faulty.
Check the that the positioning
completed signal in the
operating memory area is
turning ON and OFF.
Correct the wiring for the
positioning completed
signal.
39
The servo speed reference is
incorrect.
---
Adjust the Servo Drive’s
gain.
40
The axis is not in the
in-position range due to
external pressure applied
when positioning stopped.
Using the Servo Drive’s
monitoring functions, monitor
the error counter and check
whether the axis is in the
in-position range.
If positioning is stopped
outside of the in-position
range due to external
pressure, it is possible to
forcibly position in the
in-position range using
error counter reset
output. Doing this,
however, will result in an
unestablished origin
state and so it is
necessary to
re-establish the origin by
repeating origin search
or by performing present
position preset.
Summary of Contents for CS1W-NC113 - REV 02-2008
Page 1: ...CS1W NC113 213 413 133 233 433 Position Control Units ...
Page 2: ...iv ...
Page 4: ...vi ...