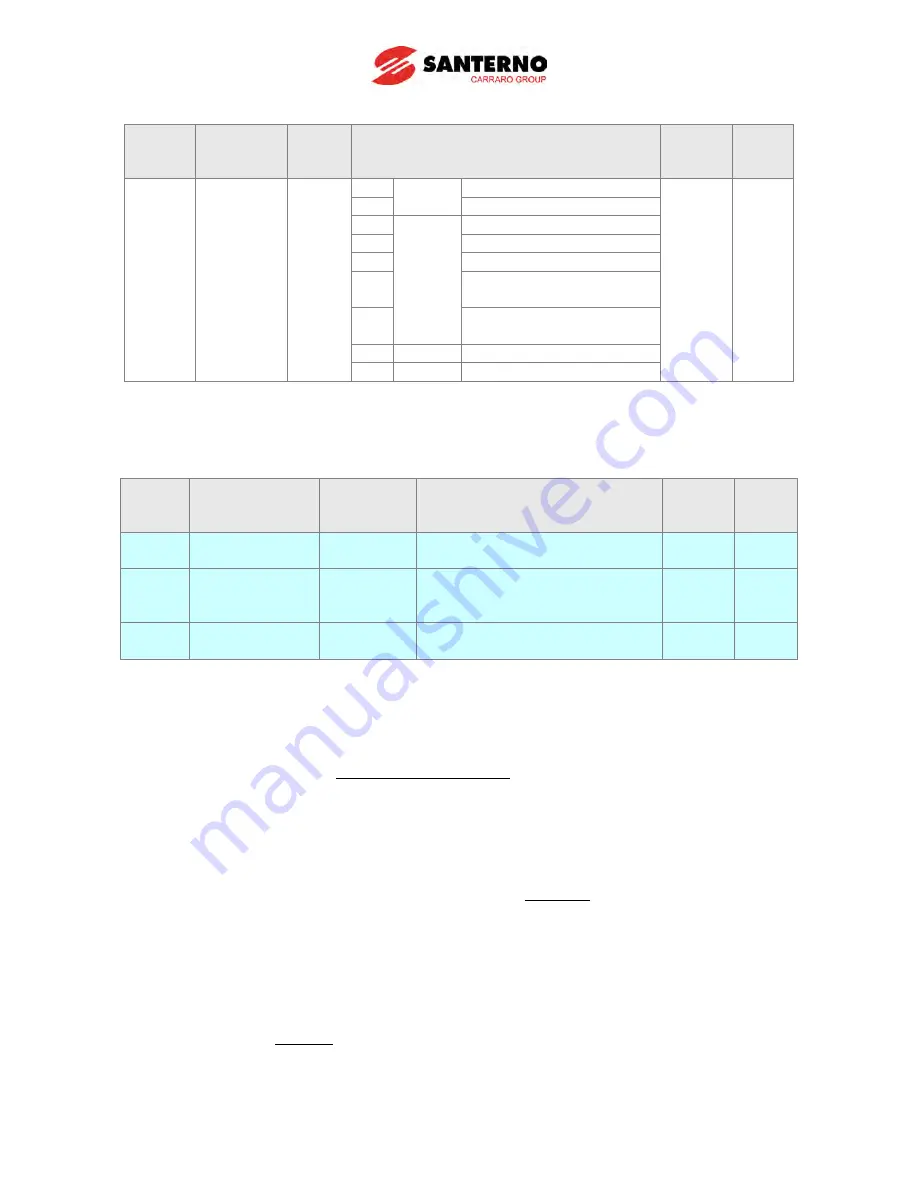
10-17
LED
display
Parameter
name
Setting
Range
Description
Factory
defaults
Adj.
During
run
Frq
Frequency
setting
method
0 ~ 7
0
Digital Keypad setting 1
0
X
1
Keypad setting 2
2
Analog
V1 1: –10 ~ +10 [V]
3
V1 2: 0 ~ +10 [V]
4
Terminal I: 0 ~ 20 [mA]
5
Terminal V1 setting 1+
Terminal I
6
Terminal V1 setting 2+
Terminal I
7
Comm. RS485
8
Digital Volume
-
The PID reference source can be selected in H57 code of function group2.
-
The PID REF value can be changed and checked in the “rEF” of DRV group.
-
PID value is basically created in ‘Hz’. ‘Hz’ is not a physical unit, so the internal PID reference is
calculated as a ‘%’ of Maximum frequency (F21).
LED
display
Parameter
name
Setting
Range
Description
Factory
defaults
Adj.
During
run
rEF
PID Reference -
PID control standard value
setting
-
-
I89
Minimum
Feedback
value
0.0~100.0
Minimum Feedback Scaling
factor
0.0
O
I90
Maximum
Feedback value 0.0~100.0
Maximum Feedback Scaling
factor
100.0
O
-
“REF” code of drive group is the additional function code of this version for real unit and the
display only code. Refer to the equation below.
min)
(
89
)
(
min)
(
89
max)
(
90
reference
physical
Real
Unit
I
Hz
ce
PIDreferen
Frequency
Max
Unit
I
Unit
I
+
×
−
=
-
If you want to display the real physical reference with %, set each I89 and I90 to 0.0 and 100.0
(Factory default). If the set value of F21 and the PID command are each 50Hz and 20Hz
respectively, then the PID reference should be like this:
0
40
0
0
0
20
0
50
0
0
0
100
.
.
.
.
.
.
=
+
×
−
.
-
You can display the physical value with Bar. For example, the pressure sensor has minimum
output 0V when 1.0 Bar and 10V when 20.0 bars. In this case, I89 and I90 should be set to 1.0
and 20.0 respectively.
-
If the max frequency and the PID command are 50Hz and 20Hz each, then the PID reference
should be like this.
6
8
0
1
0
20
0
50
0
1
0
20
.
.
.
.
.
.
=
+
×
−
Summary of Contents for Sinus M
Page 10: ......
Page 15: ...1 5 Notes...
Page 16: ......
Page 50: ...6 4 Notes...
Page 78: ...8 4 Notes...
Page 114: ...10 14 Normal PID block diagram H54 0...
Page 115: ...10 15 Process PID block diagram H54 1...
Page 150: ...10 50 Notes...
Page 174: ......
Page 192: ...13 18 Notes...
Page 204: ......
Page 219: ...17 1 CHAPTER 17 EC Declaration of Conformity...