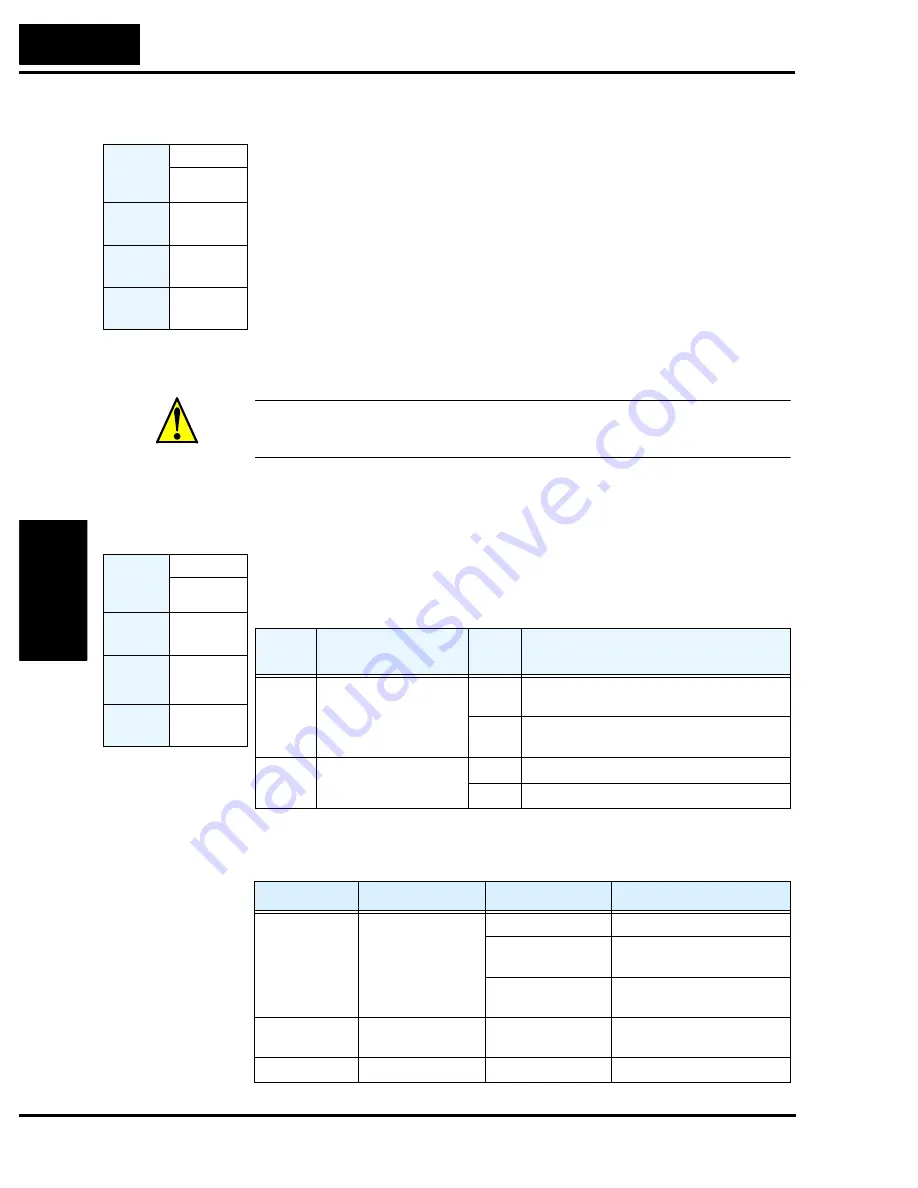
Using Intelligent Input Terminals
Oper
ations
a
nd Moni
tor
ing
4–26
PID Disable
and PID Clear
The PID loop function is useful for controlling motor speed to achieve constant flow, pressure,
temperature, etc. in many process applications.
PID Disable –
This function temporarily suspends PID loop execution via an intelligent input
terminal. It overrides the parameter A071 (PID Enable) to stop PID execution and return to
normal motor frequency output characteristics. the use of PID Disable on an intelligent input
terminal is optional. Of course, any use of the PID loop control requires setting PID Enable
function A071=01.
PID Clear –
This function forces the PID loop integrator sum = 0. So, when you turn ON an
intelligent input configured as [PIDC], the integrator sum is reset to zero. This is useful when
switching from manual control to PID loop control and the motor is stopped.
Note the following:
• The use of [PID] and [PIDC] terminals are optional. Use A071=01 if you want PID loop
control enabled all the time.
• Do not enable/disable PID control while the motor is running (inverter is in Run Mode).
• Do not turn ON the [PIDC] input while the motor is running (inverter is in Run Mode).
CAUTION:
Be careful not to turn PID Clear ON and reset the integrator sum when the inverter
is in Run Mode (output to motor is ON). Otherwise, this could cause the motor to decelerate
rapidly, resulting in a trip.
Internal Speed
Loop Gain
Settings
When sensorless vector control, 0Hz sensorless vector control, or vector control with sensor is
selected for the control method, the Control Gain Switching function selects between two sets
of gains in the internal speed loop. These gains are used in proportional and integral compensa-
tion. When Control Gain Switching is not selected for an intelligent input terminal, the default
gains in effect correspond to the OFF state of [CAS].
Use [PPI] P/PI Control Switching to select between proportional and proportional-integral
control.
The table below lists the functions and parameter settings related to internal speed loop gains.
Opt. Code
and
Symbol
23=[PID]
24=[PIDC]
Valid for
Inputs
[1] to [8]
Required
Settings
A071
Default
terminal
Requires
config.
Opt. Code
and
Symbol
26=[CAS]
43=[PPI]
Valid for
Inputs
[1] to [8]
Required
Settings
A044 / A244
/ A344 = 03,
04, or 05
Default
terminal
Requires
config.
Symbol
Function Name
Input
State
Description
CAS
Control Gain Switching
ON
Gains in parameters H070, H071, and H072
are selected
OFF
Gains in parameters H050, H051, H052; or,
H250, H251, H252 (2nd motor) are selected
PPI
P / PI Control Switching
ON
Selects Proportional control (P)
OFF
Selects Proportional-Integral control (PI)
Function Code
Parameter
Setting Range
Description
A044 / A244 /
A344
Control method
selection
03
SLV (does not use A344)
04
0-Hz Domain SLV (does not
use A344)
05
V2 (does not use A244 or
A344)
C001 - C008
Intelligent input
selection
43
PPI : P/I switching
H005 / H205
Speed response
0.001 to 65.53
No dimension