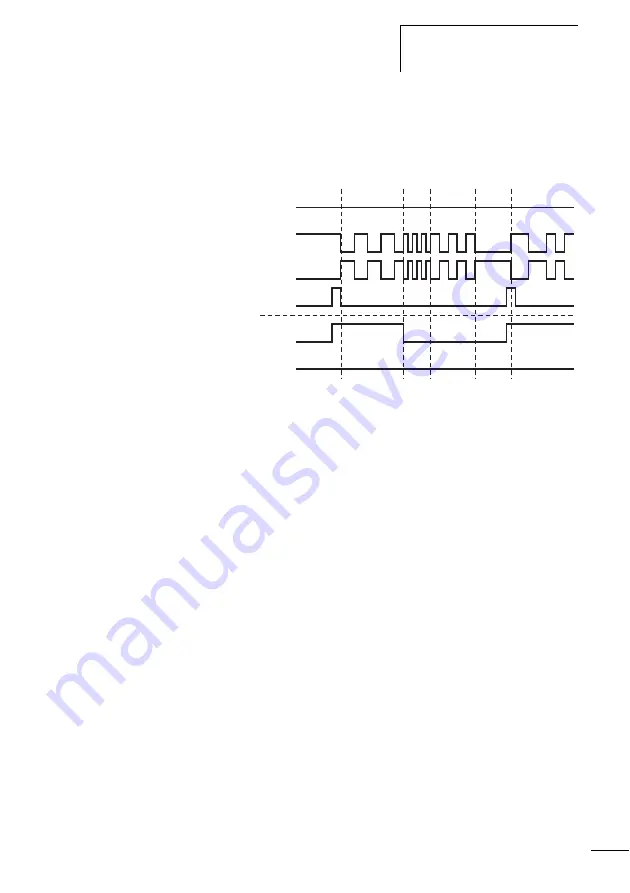
OM, Maximum speed moni-
toring
447
02/16 MN05013001Z EN
The signal diagram of the function block for this application
shows the dependence of the enable contact OM01QS on
the measured frequency at the function block coils I1 and I2:
Figure 226:
Example of overspeed monitoring: signal diagram
a
The overspeed monitoring function block OM01 is activated via
OM01SA, speed monitoring is started via the Reset input
OM01RE. As the motor is standing still, the function block
issues the enable via OM01QS (OM01QS = 1).
b
The motor rotates below the parameterized limit frequency of
66 Hz.
c
The motor rotation exceeds the limit frequency. The OM01
function block removes its enable (OM01QS = 0).
d
.The motor gets slower and runs down.
e
The motor is at a standstill. The function block OM01 is reset
via the Reset input and issues its enable again, OM01QS closes.
f
The motor rotates below the maximum rotation frequency.
The following graph shows the time requirements for the
signals to IS1 and IS2 with the resulting valid and invalid
states at the maximum rotational frequency of 1000 Hz:
• Valid signal level and time interval for a start.
• Minimum time for the Low signal at IS1 and IS2.
• Minimum time interval between the edge changes at IS1
and IS2.
OM01SA
OM01QS
OM01ER
OM01RE
OM01I1
OM01I2
a
b
c
d
e
f
Summary of Contents for easySafety
Page 1: ...Manual Control relay suitable for safety circuits Safety ES4P 02 16 MN05013001Z EN ...
Page 4: ...2 ...
Page 42: ...38 02 16 MN05013001Z EN ...
Page 80: ...Installation 76 02 16 MN05013001Z EN ...
Page 112: ...108 02 16 MN05013001Z EN ...
Page 606: ...602 02 16 MN05013001Z EN ...