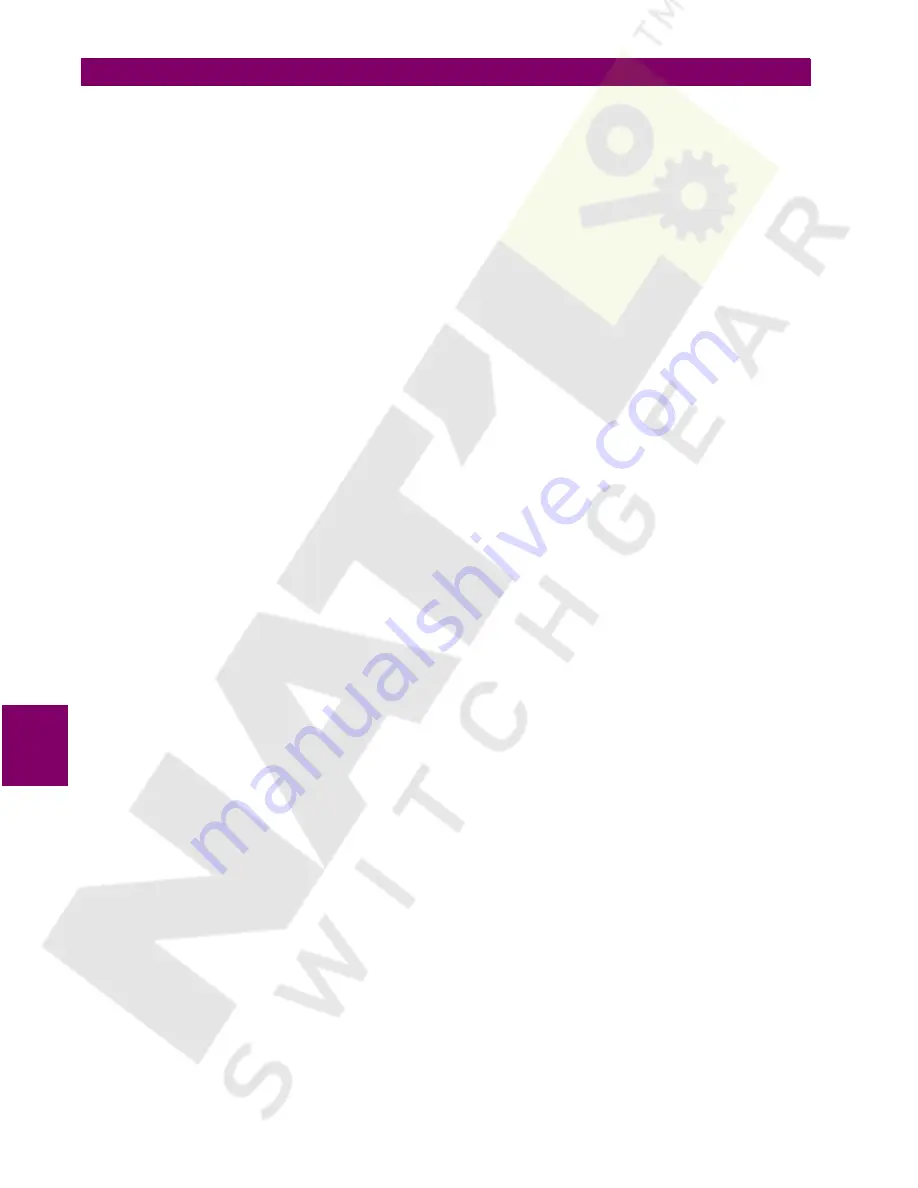
17-
72
750/760 Feeder Management Relay
GE Power Management
17.9 CONTROL SCHEMES
17 COMMISSIONING
17
16. Set a current level above the pickup threshold of any time overcurrent element and turn the current off.
17. Repeat step 12. Assert a Close command, either locally or remotely, and turn the current on. Check that
lockout is not reset at the end of the manual close blocking time interval, and the breaker eventually trips.
Turn the current off.
If Breaker Operation Failure, and/or Breaker Failure features are Operational:
Open test switch SW9 to prevent a trip command from the relay from operating the breaker. Enable one of the
O/C elements which is to be programmed for a function of Trip + AR. Inject a current above the pickup level of
both the operational O/C feature and the Breaker Failure Current into the relay, until the feature sends a trip,
which will also initiate reclosure. After the failure delay time a breaker failure condition will be determined,
which should immediately set the reclose scheme to the Lockout state, turning the RECLOSURE LOCKOUT
indicator on. Turn the injected current off and Reset the relay. Disable the O/C element and close both the
breaker and SW9.
Current Supervision:
1.
Note that the number of reclosure shots programmed controls the messages in this group. If 4 shots are
programmed, all messages are available. If 3 shots are programmed, setpoint
3 SHOTS FOR CURRENT ABOVE
is not available on the relay. If 2 shots are programmed, setpoints
3 SHOTS FOR CURRENT ABOVE
and
2
SHOTS FOR CURRENT ABOVE
are not available on the relay. The following procedure assumes 4 shots are
programmed.
2.
Close the breaker and wait until reclosure is enabled.
3.
Display
A1 STATUS \ AUTORECLOSE \ AUTORECLOSE SHOTS REMAINING
– the value displayed should be 4.
4.
Open SW9 so the breaker cannot trip. Inject current and slowly ramp higher until an instantaneous feature
sends a trip, which also initiates reclosure. The value displayed should be 4 (it has not yet decremented).
5.
Continue to very slowly increase the current until the value displayed becomes 3. Continue to very slowly
increase the current, until the value displayed sequentially becomes 2 and then 1, at the currents pro-
grammed. Very slowly increase the current, at the current programmed, until the relay goes to Lockout.
Zone Coordination:
1.
Select the
MAXIMUM NUMBER OF RECLOSURE SHOTS
to be 4. Set the test set to a current level above the set-
ting of the
PHASE CURRENT INCREASE
setpoint, and ensure that the neutral current is below the
NEUTRAL
CURRENT INCREASE
setpoint by making this setting a large value. Turn on the current. Then, before the
MAX
FAULT CLEARING TIME
has elapsed, turn off the current. The
SHOT NUMBER IN EFFECT
should have been
incremented. Reset the relay. Turn on the current. Then, after the
MAX FAULT CLEARING TIME
has elapsed,
turn off the current. The
SHOT NUMBER IN EFFECT
should not have been incremented. Reset the relay.
2.
Set the current level below the setting of the
PHASE CURRENT INCREASE
setpoint. Turn the current on and
then off. The
SHOT NUMBER IN EFFECT
should not change.
3.
Set the current level above the setting of the
PHASE CURRENT INCREASE
setpoint, but below the Neutral Cur-
rent Increase setpoint. Turn the current on and then off. The
SHOT NUMBER IN EFFECT
should increment.
Repeatedly turning the current on and then off should continue to increment the Shot in Effect to the
MAXI-
MUM NUMBER OF RECLOSURE SHOTS
, and the Autoreclose scheme will go into lockout.
4.
Set the current level such that the neutral current is below the
NEUTRAL CURRENT INCREASE
setpoint and the
phase current is below the
PHASE CURRENT INCREASE
setpoint. Turn the current on and then off. The
SHOT
NUMBER IN EFFECT
should not change.
5.
Set the current level such that the neutral current is above the
NEUTRAL CURRENT INCREASE
setpoint and the
phase current is below the
PHASE CURRENT INCREASE
setpoint. Turn the current on and then off. The
SHOT
IN EFFECT
should increment as in step 3.
Содержание 750
Страница 2: ......
Страница 4: ......
Страница 124: ...8 14 750 760 Feeder Management Relay GE Power Management 8 12 INSTALLATION 8 S1 RELAY SETUP 8 ...
Страница 144: ...10 14 750 760 Feeder Management Relay GE Power Management 10 10 MISCELLANEOUS FUNCTIONS 10 S3 LOGIC INPUTS 10 ...
Страница 152: ...11 8 750 760 Feeder Management Relay GE Power Management 11 3 OUTPUT RELAYS 3 7 AUXILIARY 11 S4 OUTPUT RELAYS 11 ...
Страница 216: ...12 64 750 760 Feeder Management Relay GE Power Management 12 9 BREAKER FAILURE 12 S5 PROTECTION 12 ...
Страница 484: ...17 78 750 760 Feeder Management Relay GE Power Management 17 10 PLACING THE RELAY IN SERVICE 17 COMMISSIONING 17 ...
Страница 488: ...A 4 750 760 Feeder Management Relay GE Power Management A 1 FIGURES AND TABLES APPENDIXA A ...
Страница 490: ...B 2 750 760 Feeder Management Relay GE Power Management B 1 EU DECLARATION OF CONFORMITY APPENDIXB B ...
Страница 492: ...C 2 750 760 Feeder Management Relay GE Power Management C 1 WARRANTY INFORMATION APPENDIXC C ...
Страница 502: ...x 750 760 Feeder Management Relay GE Power Management INDEX ...
Страница 503: ...GE Power Management 750 760 Feeder Management Relay NOTES ...