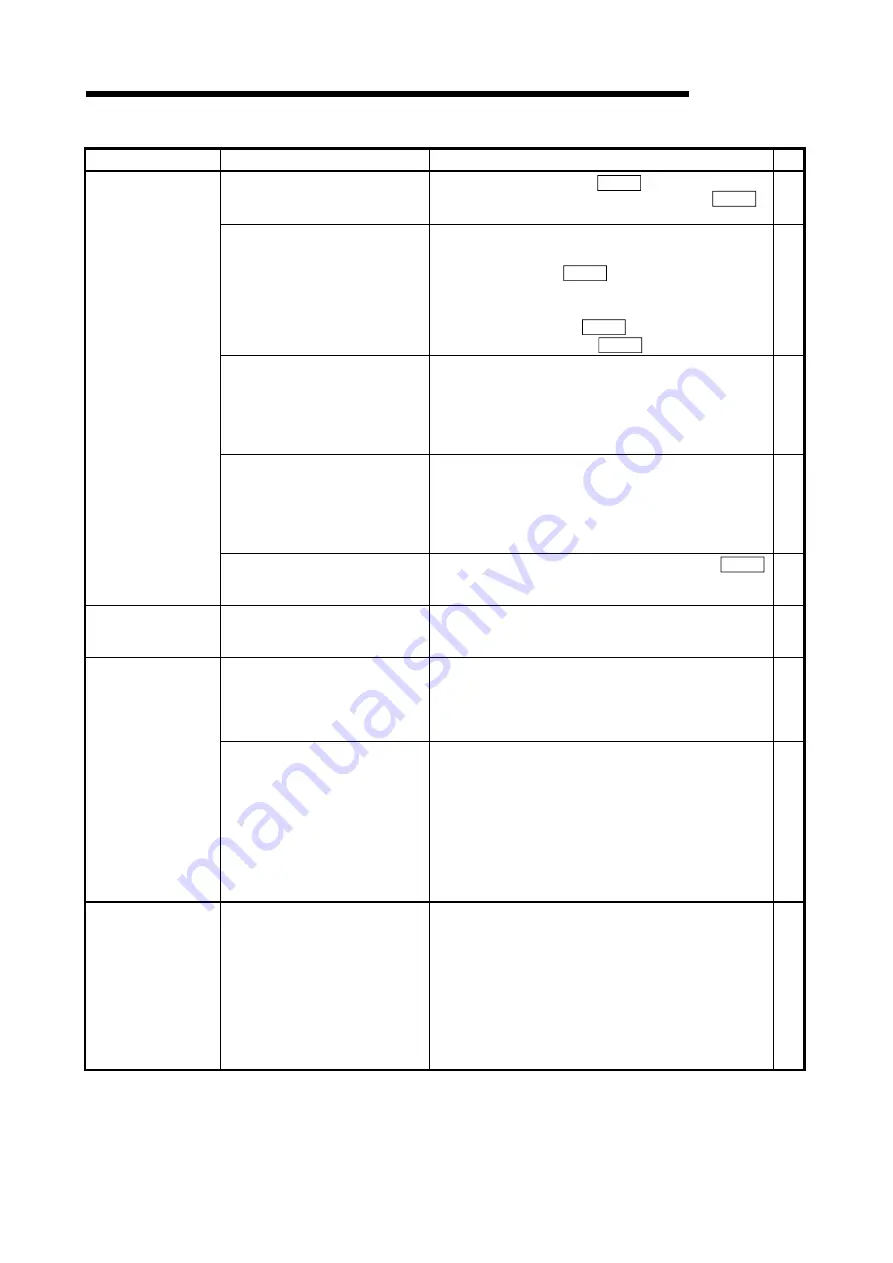
Appendix - 47
MELSEC-A
APPENDICES
Trouble type
Questions/Trouble
Remedy
No.
How can the deceleration stop
time during stopping be shortened
using the hardware stroke limit?
Set "1: Sudden stop" in the "
Pr.38 Stop group 1 sudden
stop selection", and reduce the setting value of " Pr.37
Sudden stop deceleration time".
11
The motor does not operate at
"60000ms" although the
acceleration/deceleration time is
set to "60000ms".
The value set for the acceleration/deceleration time is the
time required for the machine to accelerate from speed
"0" to the value set in " Pr.7 Speed limit value".
Because of that, the acceleration/deceleration time will
also be shorter than "60000ms" if the command speed
value is smaller than the " Pr.7 Speed limit value".
(Refer to the explanation for Pr.8 for details.)
12
Can each acceleration/
deceleration time be individually
set to trapezoidal or S-curve
acceleration/deceleration?
The trapezoidal and S-curve acceleration/deceleration
processing is a common setting for all
acceleration/deceleration times, so individual setting is not
possible.
(Refer to the section "12.6.7 Acceleration/deceleration
process function".)
13
The machine starts and stops
suddenly when carrying out JOG
operations and positioning
operations.
(Using an MR-J2S servo
amplifier.)
Review the parameter settings for acceleration/
deceleration time, speed limit value, JOG speed limit
value, JOG acceleration/deceleration time, etc.
14
Acceleration/decelerat
ion time
How can a value higher than
"65536ms" be set in the
acceleration/deceleration time?
A value up to "8388608ms" can be set when the " Pr.25
Size selection for acceleration/deceleration time" is set to
"1".
15
Simplified absolute
position detection
system
Are simplified absolute position
detection system possible in the
A1SD75P and AD75P models?
They are possible if the models are used in combination
with a Mitsubishi "AC Servo".
(Refer to the "AC servo User's Manual" for details.)
16
The physical position deviates
from the commanded position,
although the positioning is
complete (and the monitored
current position is correct).
If the deviation counter value is not "0", the servo side is
still moving.
Increase the torque.
17
Positional deviation
When positioning to "6300mm" is
commanded with 1-axis direct
control (ABS type), the machine
position is "6299mm" when the
positioning is complete.
Depending on the "Movement amount per pulse" setting,
the positioning may be insufficient by the error amount
when positioning is attempted to an address for which the
No. of pulses was generated. This is because the
movement is controlled so as not to exceed the
designated address when the error amount movement
amount is generated to the AD75.
In this situation, adjust the "Movement amount per pulse"
setting so the positioning completes at the correct
position.
18
Electronic gear
A setting of "1
μ
m = 1pulse" is
required in the following system.
•
Ball screw pitch = 10mm
•
No. of feedback pulses =
8192 pulse
In this case, the following values will result.
•
No. of pulses per rotation = 8192
•
Movement amount per rotation = 10000
•
Unit
magnification = 10
Therefore, the "Movement amount per pulse" will become
"1.2207
μ
m".
This value is fixed by the machine system, so it cannot be
changed.
Thus, the setting "1
μ
m = 1 pulse" cannot be achieved.
19
Artisan Technology Group - Quality Instrumentation ... Guaranteed | (888) 88-SOURCE | www.artisantg.com
Summary of Contents for A1SD75P1-S3
Page 2: ...Artisan Technology Group Quality Instrumentation Guaranteed 888 88 SOURCE www artisantg com...
Page 3: ...Artisan Technology Group Quality Instrumentation Guaranteed 888 88 SOURCE www artisantg com...
Page 620: ...Artisan Technology Group Quality Instrumentation Guaranteed 888 88 SOURCE www artisantg com...
Page 621: ...Artisan Technology Group Quality Instrumentation Guaranteed 888 88 SOURCE www artisantg com...