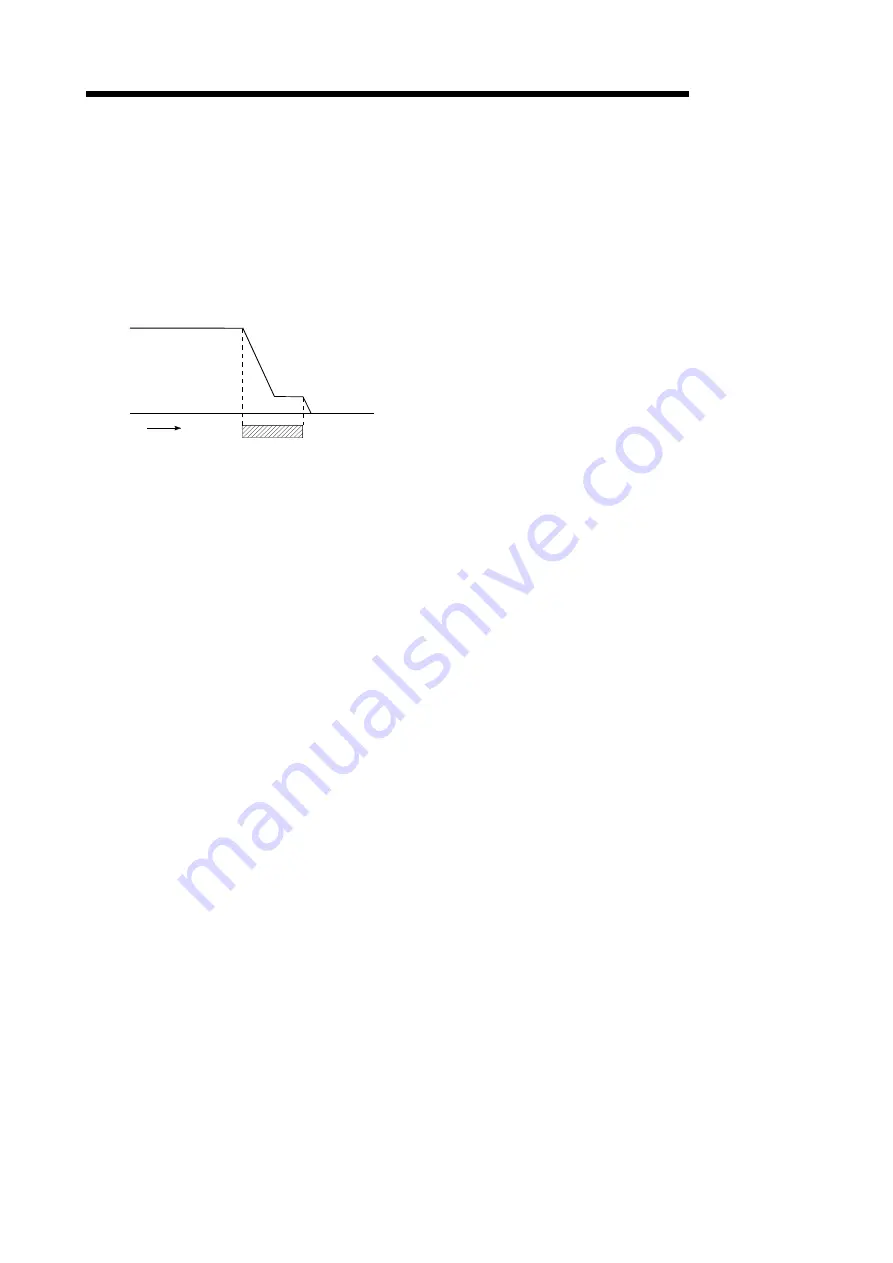
Appendix - 37
MELSEC-A
APPENDICES
NEAR-POINT DOG
This is a switch placed before the zero point.
When this switch turns ON, the feedrate is
changed to the creep speed. Because of that,
the time that this switch is ON must be long
enough to allow for the time required for
deceleration from the feedrate to the creep
speed.
ON
OFF
Feedrate
Creep speed
Time
Near-point dog
OPERATION PATTERN
The kind of operation to be carried out after
executing the positioning data is determined.
1) If "POSITIONING COMPLETE" is selected,
the operation will stop after the positioning
is complete.
2) If "CONTINUOUS POSITIONING
CONTROL" is selected, the next data No.
will be automatically executed after the
positioning is complete.
3) If "CONTINUOUS PATH CONTROL" is
selected, the positioning will not be
completed. Only the speed will be
automatically changed, and the next data
No. will be executed.
OUTPUT TERMINAL
This is a pin connector for outputting data from
the AD75 to an external source. It is connected
to the motor drive unit.
This terminal is used to output the following.
•
Feedback pulses for both forward run and
reverse run
•
Start
•
Deviation counter clear
The terminal Nos. are determined for each
axis.
The output No. Yn is not directly related to the
program, so it is not used.
OVERRIDE FUNCTION
With this function, the speed during positioning
operations (current speed) can be varied
between 1 and 300%.
The speed can also be changed by the same
variable rate for continuous positioning with
differing designated speeds.
P RATE (Pulse Rate)
A coefficient that magnifies the feedback
pulses per motor shaft rotation by 2-fold, 3-
fold, 1/2 or 1/3.
It is the ratio of the feed pulses and feedback
pulses.
For example, when the No. of pulses per
motor shaft rotation is set to 2400 pulses, and
the P rate is set to 2, the result will be
equivalent to 1200 pulses.
The rotation per pulse is 0.15° when 2400
pulses per rotation are set, but this becomes
0.3° when 1200 pulses. The positioning
accuracy drops as the P rate is increased.
PANCAKE MOTOR
The axial dimension of this motor is approx.
100mm shorter than that of a standard motor.
This type of motor is used when the
servomotor installation space is narrow.
PARAMETER
This is the basic data used in positioning.
Parameters are determined by the machine
side design, so subsequent changes of
parameters must be accompanied by changes
in the machine design.
Data cannot be written during positioning. The
initial parameter values are written by the
maker.
POSITION CONTROL
This is mainly the control of position and
dimension, such as in fixed-dimension feed,
positioning, numerical control, etc. This is
always controlled with feed pulses. There is
also speed control.
Drive units may differ, even when the same
motor is used.
Artisan Technology Group - Quality Instrumentation ... Guaranteed | (888) 88-SOURCE | www.artisantg.com
Summary of Contents for A1SD75P1-S3
Page 2: ...Artisan Technology Group Quality Instrumentation Guaranteed 888 88 SOURCE www artisantg com...
Page 3: ...Artisan Technology Group Quality Instrumentation Guaranteed 888 88 SOURCE www artisantg com...
Page 620: ...Artisan Technology Group Quality Instrumentation Guaranteed 888 88 SOURCE www artisantg com...
Page 621: ...Artisan Technology Group Quality Instrumentation Guaranteed 888 88 SOURCE www artisantg com...