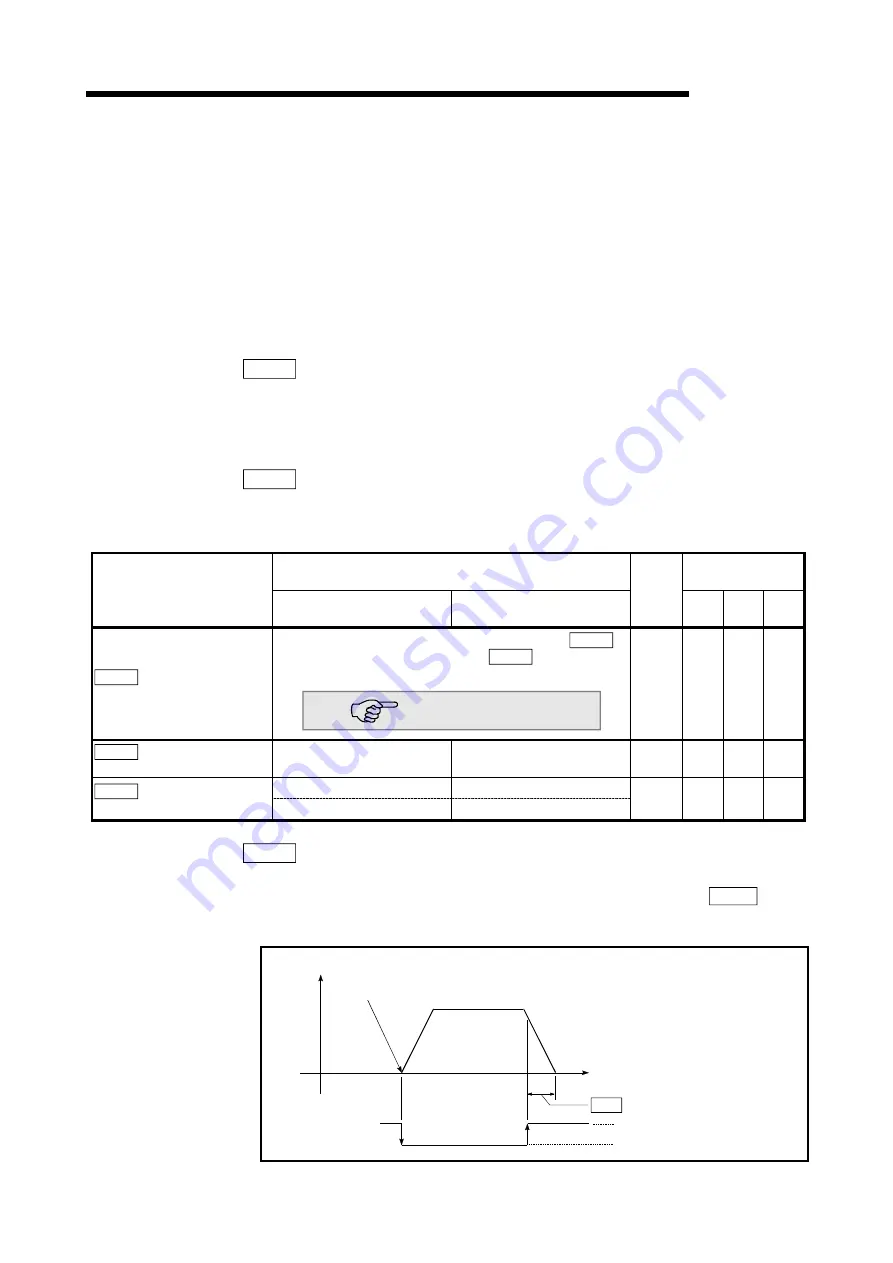
5 - 30
MELSEC-A
5 DATA USED FOR POSITIONING CONTROL
1) Generally, the zero point is set at the lower limit or upper limit of the stroke
limit.
2) By setting the upper limit value or lower limit value of the software stroke limit,
overrun can be prevented in the software. However, an emergency stop limit
switch must be installed nearby outside the range.
3) To invalidate the software stroke limit, set the setting value to "upper limit
value = lower limit value". (The setting value can be anything.)
4) When the unit is "degree", the software stroke limit check is invalid during
speed control (including speed/position chageover control) or during manual
control.
Pr.15 Software stroke limit selection
Set whether to apply the software stroke limit on the "current feed value" or the
"machine feed value". The software stroke limit will be validated according to the
set value.
Pr.16 Software stroke limit valid/invalid setting
Set whether to validate the software stroke limit during JOG operation and manual
pulse generator operation.
Setting value, setting range
Setting value buffer
memory address
Item
Value set with peripheral
device
Value set with sequence
program
Default
value
Axis 1 Axis 2 Axis 3
Pr.17 Command in-position
width
The setting value range differs depending on the " Pr.11
Stepping motor mode selection" or " Pr.1 Unit setting".
Here, the value within the [Table 1] range is set.
[Table 1] on right page
100
22
23
172
173
322
323
Pr.18 Torque limit setting
value
1 to 500 (%)
1 to 500 (%)
300
24
174
324
0 : WITH mode
0
Pr.19 M code ON signal
output timing
1 : AFTER mode
1
0 25
175
325
Pr.17 Command in-position width
Set the remaining distance that turns the command in-position ON. When
positioning control is started, the "command in-position flag" (b2) in " Md.40
Status" turns OFF, and the "command in-position flag" turns ON in the range of the
command in-position.
ON
OFF
Pr.17
Command in-position width
Speed
Position control start
Command
in-position flag
Artisan Technology Group - Quality Instrumentation ... Guaranteed | (888) 88-SOURCE | www.artisantg.com
Summary of Contents for A1SD75P1-S3
Page 2: ...Artisan Technology Group Quality Instrumentation Guaranteed 888 88 SOURCE www artisantg com...
Page 3: ...Artisan Technology Group Quality Instrumentation Guaranteed 888 88 SOURCE www artisantg com...
Page 620: ...Artisan Technology Group Quality Instrumentation Guaranteed 888 88 SOURCE www artisantg com...
Page 621: ...Artisan Technology Group Quality Instrumentation Guaranteed 888 88 SOURCE www artisantg com...