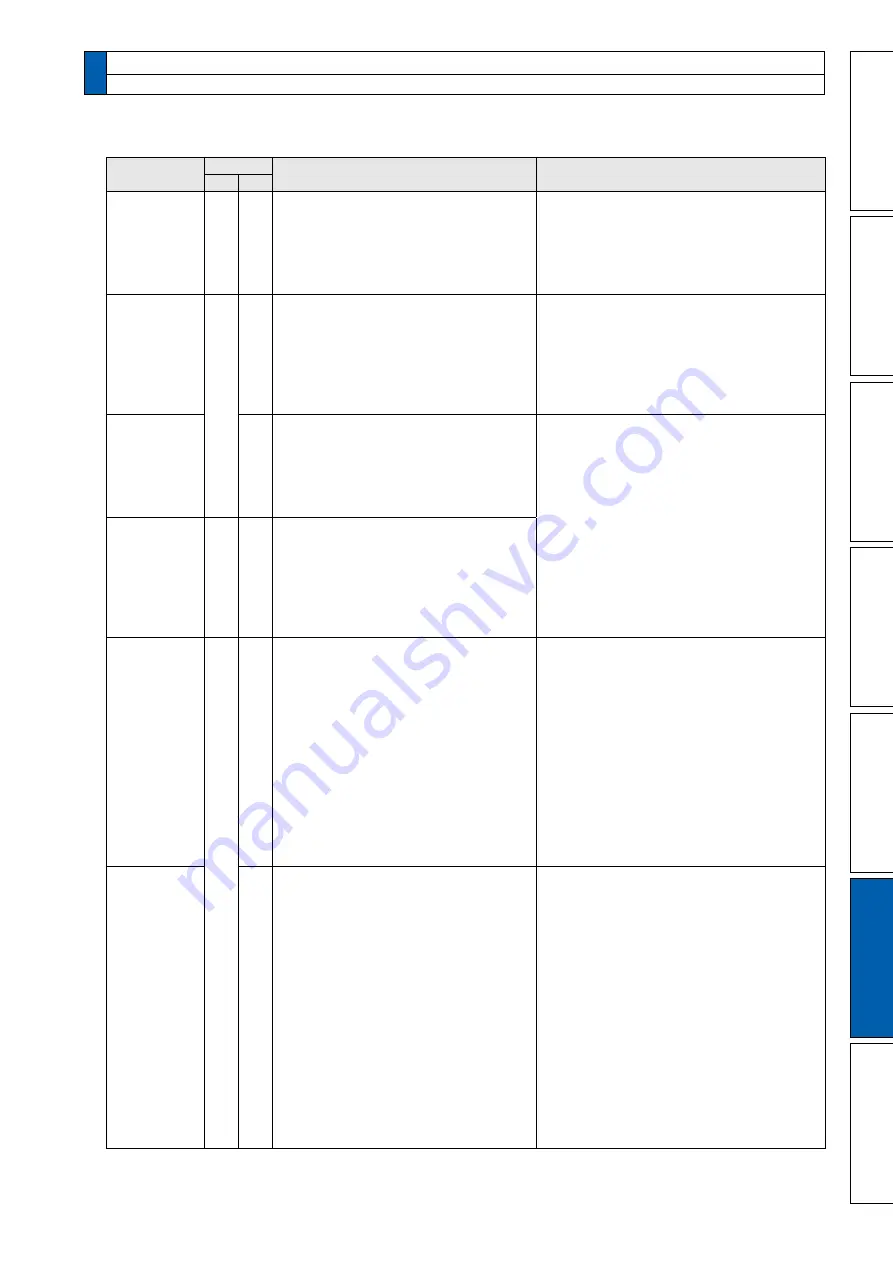
Protective
function
Error code No.
Causes
Measures
Main Sub
6-7
1. When in Trouble
Protective function (Detail of error code)
1
Before Using the Products
2
Preparation
3
Connection
4
Setup
5
Adjustment
6
When in T
rouble
7
Supplement
*
Regenerative
transistor
error
protection
18
1
Regenerative driver transistor on the
servo driver is defective.
Replace the driver.
*
Encoder
communication
disconnection
error
protection
21
0
Communication between the encoder
and the driver has been interrupted
in certain times, and disconnection
detecting function has been triggered.
Make a wiring connection of the encoder as
per the wiring diagram. Correct the miswiring
of the connector pins.
*
Encoder
communication
error
protection
1
Communication error has occurred in
data from the encoder. Mainly data
error due to noise. Encoder cables are
connected, but communication data has
some errors.
• Secure the power supply for the encoder
of DC4.90 V to 5.25 V)...pay an attention
especially when the encoder cables are
long.
• Separate the encoder cable and the motor
cable if they are bound together.
• Connect the shield to FG.
*
Encoder
communication
data error
protection
23
0
Data communication between the
encoder is normal, but contents of data
are not correct.
Mainly data error due to noise. Encoder
cables are connected, but communication
data has some errors.
Position
deviation
excess
protection
24
0
Deviation pulses have exceeded the
setup of Pr0.14.
1) The motor movement has not followed
the command.
2) Setup value of Pr0.14 (Position
deviation excess setup) is small.
1) Check that the motor follows to the position
command pulses. Check that the output
toque has not saturated in torque monitor.
Make a gain adjustment. Set up maximum
value to Pr0.13 and Pr5.22. Make a
encoder wiring as per the wiring diagram.
Set up the longer acceleration/deceleration
time. Lower the load and speed.
2) Set up a larger value to Pr0.14.
Speed
deviation
excess
protection
1
The difference between the internal
positional command speed and actual
speed (speed deviation) exceeds the
setup vale of Pr6.02.
Note) If the internal positional command
speed is forcibly set to 0 due to
instantaneous stop caused by the
command pulse inhibit input (INH) or
CW/CCW over-travel inhibit input, the
speed deviation rapidly increases at this
moment. Pr6.02 setup value should have
sufficient margin because the speed
deviation also largely increases on the
rising edge of the internal positional
command speed.
• Increase the setup value of Pr6.02.
• Lengthen the acceleration/deceleration
time of internal positional command speed,
or improve the follow-up characteristic by
adjusting the gain.
• Disable the excess speed deviation
detection (Pr6.02 = 0).
Buy: www.ValinOnline.com | Phone 844-385-3099 | Email: [email protected]