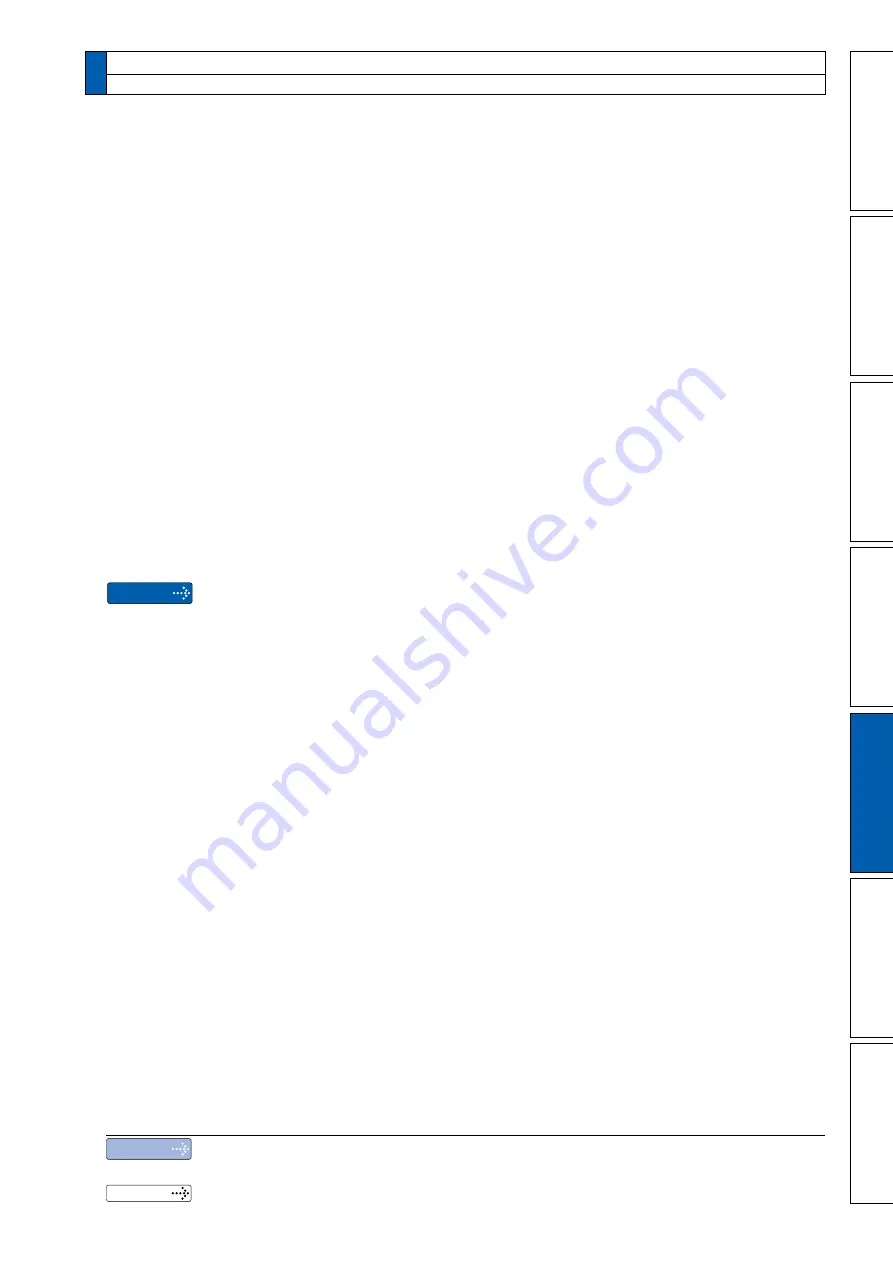
5-13
1
Before Using the Products
2
Preparation
3
Connection
4
Setup
5
Adjustment
6
When in T
rouble
7
Supplement
*
1 Velocity control is the same as in the quick response mode 2. Value of parameters,
Pr6.08 Forward torque compensation value, Pr6.09 Backward torque compensation
value and Pr6.50 Viscous friction compensation gain will be updated but not reflected
on operation.
3) When the servo is tuned on, input the action command.
4) As the load characteristics are correctly estimated, Pr0.04 Inertia ratio will be updated.
In a specific mode, the following parameters are changed.
Pr6.07 Torque command additional value
Pr6.08 Positive direction torque compensation value
Pr6.09 Negative direction torque compensation value
Pr6.50 Viscous friction compensation gain
Load characteristics estimation speed can be set by Pr6.31 Real time auto tuning esti-
mation speed.
5) When value of Pr0.03 Real-time auto-tuning stiffness setup is increased, the motor re-
sponsiveness will be improved.
Determine the most appropriate stiffness in relation to the positioning setup time and
vibration condition.
6) To save the result to memory, write the date to EEPROM.
If power is turned off within 30 minutes after the end of tuning process, the result of the
real-time auto-tuning is not saved. If the result is not saved, manually write parameters to
EEPROM and then turn off power.
2. Real-Time Auto-Gain Tuning
Two-degree-of-freedom control mode – Standard type
Note
Related page
• While the auto-tuning is valid, parameters that are to be automatically adjusted cannot be
changed.
• P.2-109 “EEPROM Writing Mode” • P.4-6 to P.4-85... “Details of parameter”
Caution
Buy: www.ValinOnline.com | Phone 844-385-3099 | Email: [email protected]