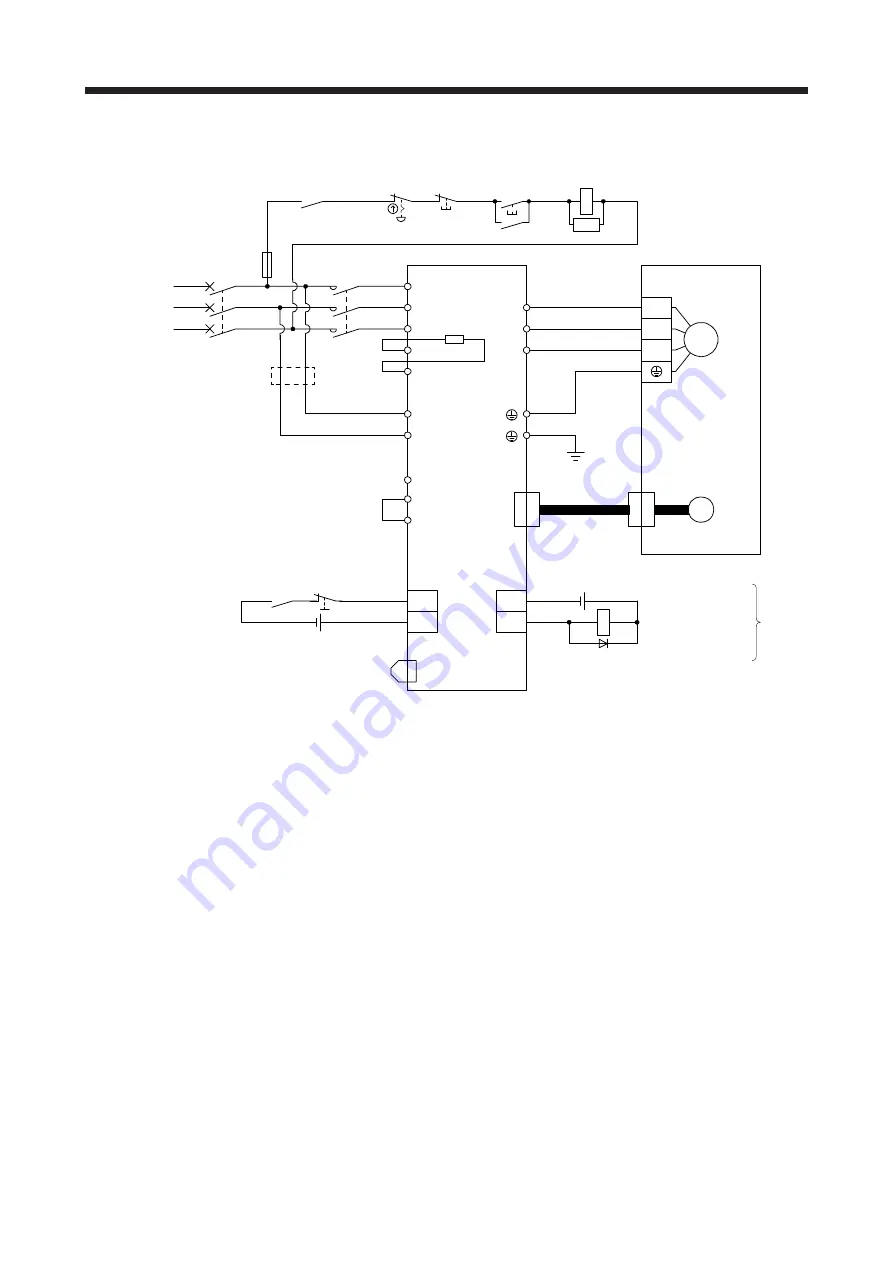
3. SIGNALS AND WIRING
3 - 7
(4) MR-J4-700TM
C
P+
L11
L21
P3
P4
N-
L1
L2
L3
U
V
W
U
V
W
M
CN2
MC
MC
SK
CN8
MCCB
ALM
DOCOM
CN3
RA1
CN3
EM2
DICOM
Built-in
regenerative
resistor
MC
(Note 7)
(Note 5)
24 V DC (Note 12)
Malfunction (Note 4)
3-phase
200 V AC to
240 V AC
Servo amplifier
(Note 1)
(Note 10)
(Note 2)
Servo motor
Motor
Encoder
(Note 3)
Encoder
cable
(Note 6)
(Note 4)
Malfunction
RA1
OFF
ON
Emergency stop switch
(Note 5) Forced stop 2
(Note 9)
Short-circuit connector
(Packed with the servo amplifier)
(Note 8)
Main circuit power supply
(Note 11)
(Note 11)
24 V DC (Note 12)
Note 1. Between P3 and P4 is connected by default. When using the power factor improving DC reactor, remove the short bar
between P3 and P4. Refer to section 11.11 for details. Additionally, a power factor improving DC reactor and power factor
improving AC reactor cannot be used simultaneously.
2. When using the regenerative option, refer to section 11.2.
3. For the encoder cable, use of the option cable is recommended. For selecting cables, refer to "Servo Motor Instruction Manual
(Vol. 3)".
4. If disabling ALM (Malfunction) output with the parameter, configure up the power supply circuit which switches off the magnetic
contactor after detection of alarm occurrence on the controller side.
5. This diagram is for sink I/O interface. For source I/O interface, refer to section 3.8.3.
6. For connecting servo motor power wires, refer to "Servo Motor Instruction Manual (Vol. 3)".
7. Use a magnetic contactor with an operation delay time (interval between current being applied to the coil until closure of
contacts) of 80 ms or less. Depending on the main circuit voltage and operation pattern, bus voltage decreases, and that may
cause the forced stop deceleration to shift to the dynamic brake deceleration. When dynamic brake deceleration is not
required, slow the time to turn off the magnetic contactor.
8. Configure a circuit to turn off EM2 when the main circuit power is turned off to prevent an unexpected restart of the servo
amplifier.
9. When not using the STO function, attach the short-circuit connector came with a servo amplifier.
10. When wires used for L11 and L21 are thinner than wires used for L1, L2, and L3, use a molded-case circuit breaker. (Refer to
section 11.10.)
11. Connecting a servo motor of the wrong axis to U, V, W, or CN2 of the servo amplifier may cause a malfunction.
12. The illustration of the 24 V DC power supply is divided between input signal and output signal for convenience. However, they
can be configured by one.
Содержание MR-J4 TM Series
Страница 9: ...A 8 MEMO ...
Страница 17: ...8 MEMO ...
Страница 225: ...5 PARAMETERS 5 86 MEMO ...
Страница 295: ...8 TROUBLESHOOTING 8 14 MEMO ...
Страница 439: ...12 ABSOLUTE POSITION DETECTION SYSTEM 12 6 MEMO ...
Страница 521: ...16 FULLY CLOSED LOOP SYSTEM 16 20 MEMO ...
Страница 578: ...APPENDIX App 41 ...