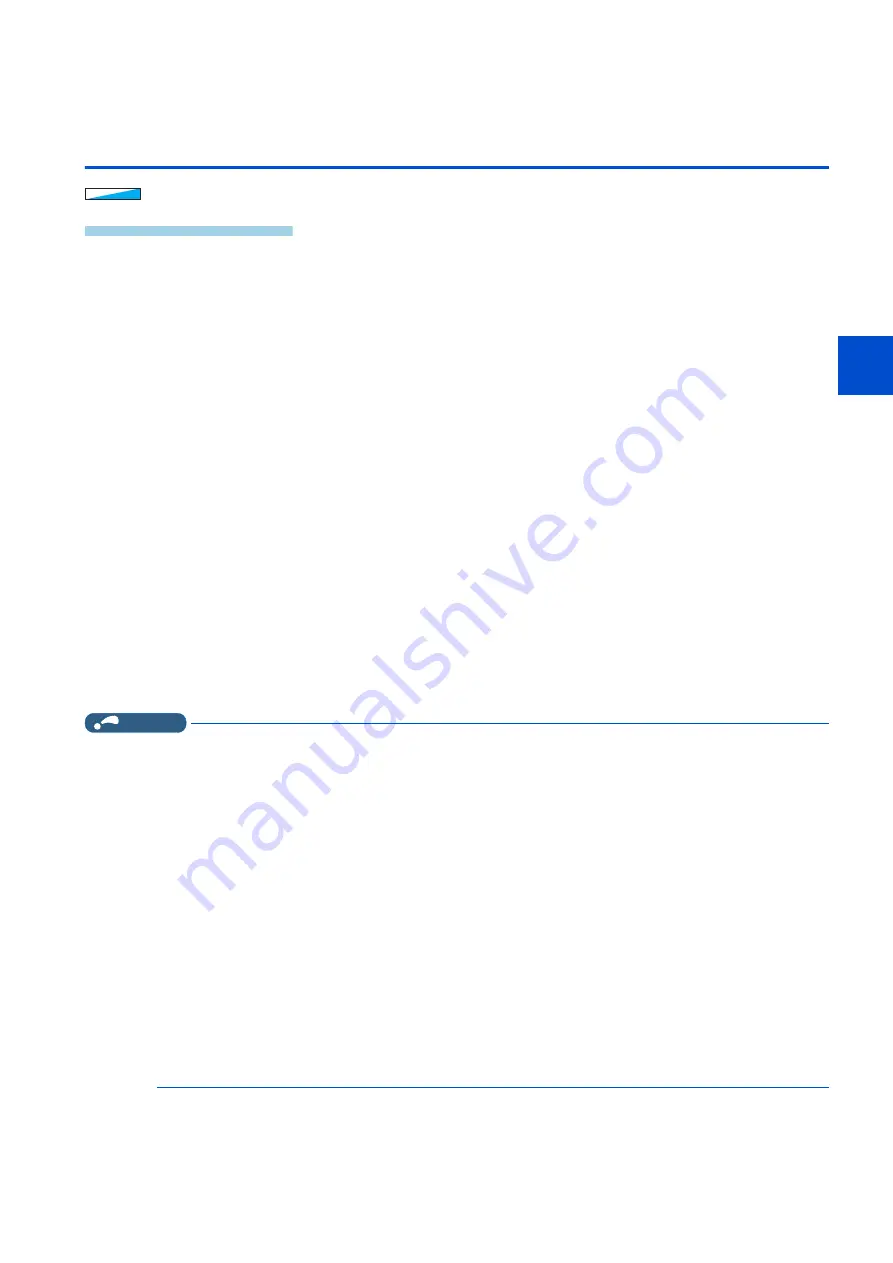
111
5. Speed Control
5.1 Setting procedure of Real sensorless vector control (speed control)
1
2
3
4
5
6
7
8
9
10
5.1
Setting procedure of Real sensorless vector
control (speed control)
Operating procedure
1.
Perform wiring properly. (Refer to the Instruction Manual (Connection).)
2.
Set the applied motor (
Pr.71
). (Refer to
Set
Pr.71 Applied motor
to "0" (standard motor) or "10" (constant-torque motor).
3.
Set the overheat protection of the motor (
Pr.9
.)
4.
Set the motor capacity and number of motor poles (
Pr.80, Pr.81
). (Refer to
.)
Operation does not start when the setting value is "9999" (initial value).
5.
Set the rated motor voltage and the rated motor frequency (
Pr.83, Pr.84
). (Refer to
6.
Select the control method (
Pr.800
). (Refer to
.)
Select
Pr.800
= "10" (speed control) or "12" (speed/torque switchover) to enable speed control.
7.
Set the operation command. (Refer to
.)
Select the start command and speed command.
8.
Set the torque limit (
Pr.810
). (Refer to
.)
9.
Perform the offline auto tuning (
Pr.96
). (Refer to
.)
10.
Perform the test operation.
As required
• Select online auto tuning (
Pr.95
). (Refer to
• Adjust the speed control gain manually. (Refer to
NOTE
• During Real sensorless vector control, offline auto tuning must be performed properly before starting operations.
• The speed command setting range under Real sensorless vector control is 0 to 400 Hz.
• The carrier frequency is limited during Real sensorless vector control. (Refer to
.)
• Torque control is not available in a low-speed (about 10 Hz or lower) regenerative range, or with a low speed and light load
(about 5 Hz or lower and rated torque about 20% or lower). Vector control must be selected.
• Performing pre-excitation (LX signal and X13 signal) under torque control may start the motor running at a low speed even
when the start signal (STF or STR) is not input. This product with the start command ON may also rotate the motor at a low
speed when the speed limit value is set to zero. Confirm that the motor running does not cause any safety problems before
performing pre-excitation.
• Switching between the forward rotation command (STF) and reverse rotation command (STR) must not be performed during
operations under torque control. An overcurrent trip (E.OC[]) or opposite rotation deceleration fault (E.11) will occur.
• In case of starting the motor while the motor is coasting under Real sensorless vector control, the frequency search must be
set for the automatic restart after instantaneous power failure function (
Pr.57
≠
"9999",
Pr.162
= "10"). (Refer to
• When Real sensorless vector control is applied, there may not be enough torque provided in the ultra low-speed range of about
2 Hz or lower.
Sensorless
Sensorless
Sensorless
Generally, the speed control range is as follows.
For power driving, 1:200 (2, 4 or 6 poles) (available at 0.3 Hz or higher when the rating is 60 Hz), 1:30 (8 or 10 poles) (available
at 2 Hz or higher when the rating is 60 Hz).
For regenerative driving, 1:12 (2 to 10 poles) (available at 5 Hz or higher when the rating is 60 Hz).
Содержание FR-E800
Страница 17: ...16 1 Introduction 1 3 Related manuals MEMO ...
Страница 51: ...50 2 Basic Operation 2 8 I O terminal function assignment MEMO ...
Страница 89: ...88 3 Parameters 3 4 Parameter list by function group number MEMO ...
Страница 135: ...134 5 Speed Control 5 9 Troubleshooting in the speed control MEMO ...
Страница 153: ...152 6 Torque Control 6 7 Troubleshooting in torque control MEMO ...
Страница 195: ...194 8 E Environment Setting Parameters 8 18 Current average value monitor signal MEMO ...
Страница 237: ...236 10 D Operation Command and Frequency Command 10 6 Operation by multi speed setting MEMO ...
Страница 339: ...338 13 T Multi Function Input Terminal Parameters 13 9 Start signal operation selection MEMO ...
Страница 455: ...454 16 G Control Parameters 16 13 Speed smoothing control MEMO ...
Страница 481: ...480 18 Appendix 18 4 Parameters functions and instruction codes under different control methods MEMO ...