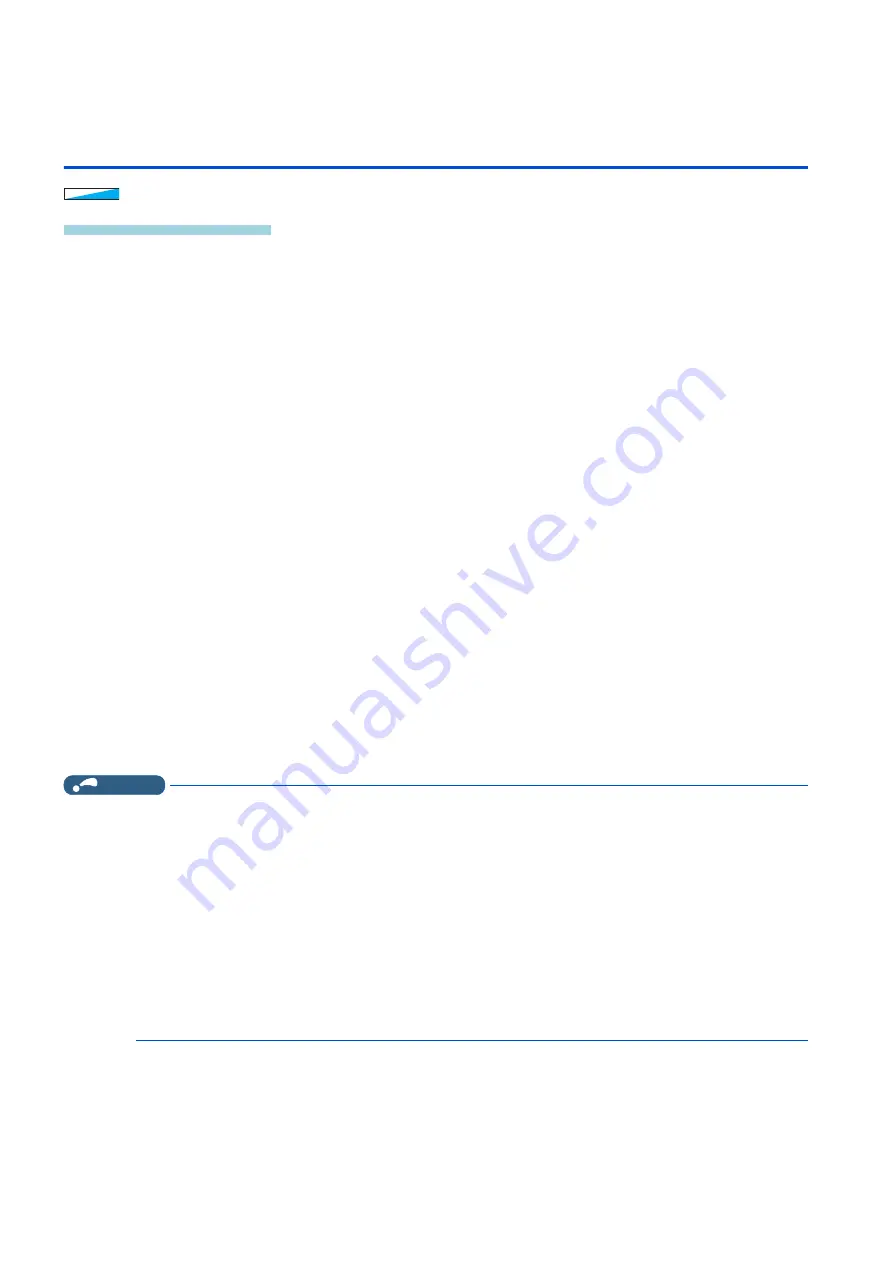
142
6. Torque Control
6.3 Setting procedure for Vector control (torque control)
6.3
Setting procedure for Vector control (torque
control)
Operating procedure
1.
Perform secure wiring. (Refer to the Instruction Manual (Connection).)
Install a Vector control compatible option.
2.
Set the motor and the encoder (
Pr.71, Pr.359, Pr.369
). (Refer to
,
3.
Set the overheat protection of the motor (
Pr.9
). (Refer to
.)
When using the SF-V5RU or a motor equipped with a thermal sensor, set
Pr.9
= 0 A. For details on connecting a
motor equipped with a thermal sensor, refer to the Instruction Manual (Connection).
4.
Set the motor capacity and the number of motor poles (
Pr.80, Pr.81
). (Refer to
V/F control is performed when the setting is "9999" (initial value).
5.
Set the rated motor voltage and frequency (
Pr.83, Pr.84
). (Refer to
.)
6.
Select the control method (
Pr.800
Select
Pr.800 Control method selection
= "1" (torque control) or "2" (speed/torque switchover) to enable torque
control.
7.
Set the torque command (
Pr.804
.)
8.
Set the speed limit (
Pr.807
.)
9.
Set the acceleration time to "0" (
Pr.7
). (Refer to
10.
Perform the test operation.
As required
• Perform offline auto tuning
(Pr.96)
. (Refer to
• Select online auto tuning (
Pr.95
.)
• Adjust the torque control gain manually. (Refer to
.)
NOTE
• Under Vector control, the magnetic flux observer is enabled to estimate or measure the flux within the motor using the current
running through the motor and the inverter output voltage. This improves the torque accuracy since the flux of a motor can be
accurately estimated and optimum characteristics can be obtained without being affected by temperature change in the
second resistor.
• Performing pre-excitation (LX signal and X13 signal) under torque control may start the motor running at a low speed even
when the start signal (STF or STR) is not input. This product with the start command ON may also rotate the motor at a low
speed when the speed limit value is set to zero. Confirm that the motor running does not cause any safety problems before
performing pre-excitation.
• The carrier frequency is limited during Vector control. (Refer to
.)
• Torque control is not available under the Vector control with PM motors.
• To give the constant torque command in the constant output range, set "1" in
Pr.803 Constant output range torque
characteristic selection
. (Refer to
• For the settings for the SF-V5RU, refer to
.
Vector
Vector
Vector
Содержание FR-E800
Страница 17: ...16 1 Introduction 1 3 Related manuals MEMO ...
Страница 51: ...50 2 Basic Operation 2 8 I O terminal function assignment MEMO ...
Страница 89: ...88 3 Parameters 3 4 Parameter list by function group number MEMO ...
Страница 135: ...134 5 Speed Control 5 9 Troubleshooting in the speed control MEMO ...
Страница 153: ...152 6 Torque Control 6 7 Troubleshooting in torque control MEMO ...
Страница 195: ...194 8 E Environment Setting Parameters 8 18 Current average value monitor signal MEMO ...
Страница 237: ...236 10 D Operation Command and Frequency Command 10 6 Operation by multi speed setting MEMO ...
Страница 339: ...338 13 T Multi Function Input Terminal Parameters 13 9 Start signal operation selection MEMO ...
Страница 455: ...454 16 G Control Parameters 16 13 Speed smoothing control MEMO ...
Страница 481: ...480 18 Appendix 18 4 Parameters functions and instruction codes under different control methods MEMO ...