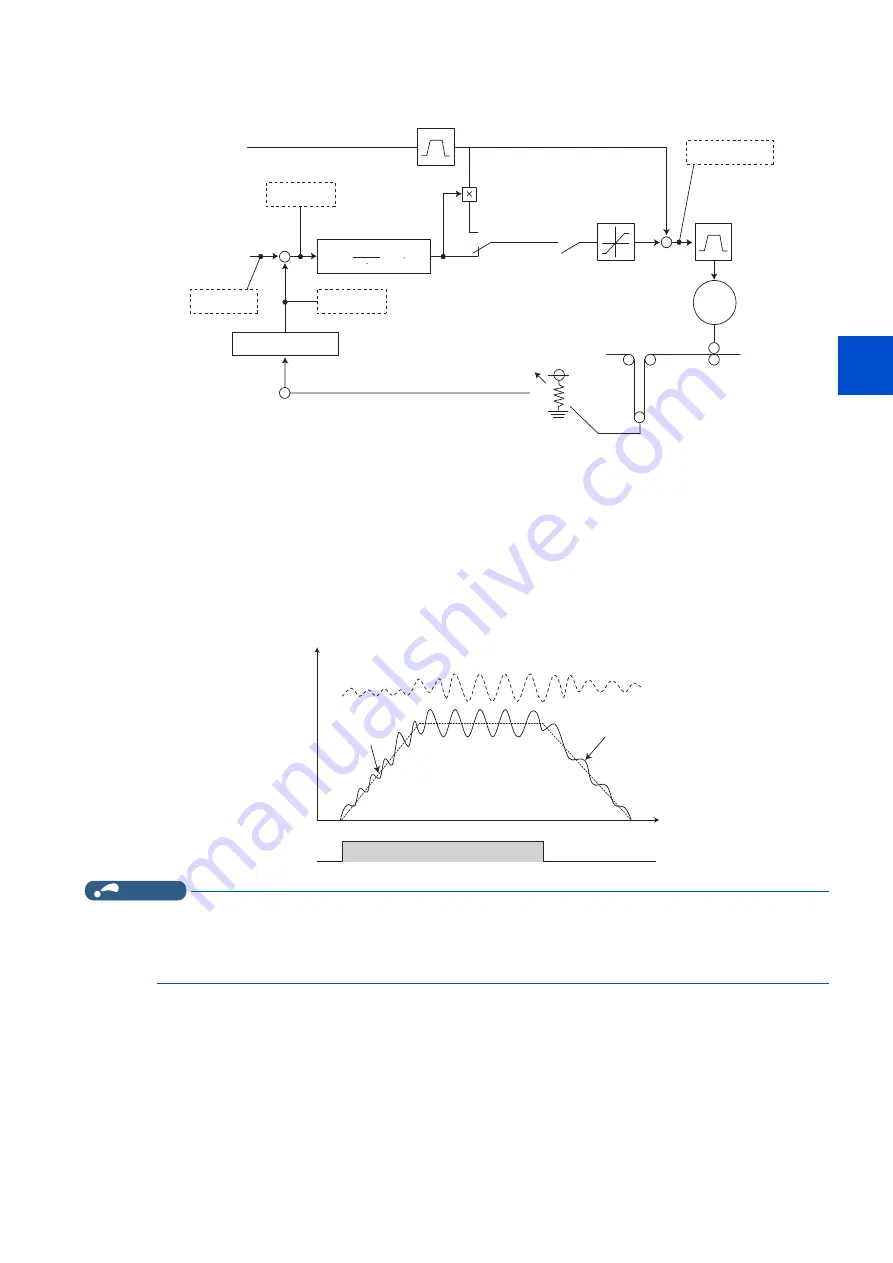
11
12
13
14
15
16
17
18
19
20
397
15. (A) Application Parameters
15.6 Dancer control
Block diagram of dancer control
*1
The main speed can be selected in all operation modes, External (analog voltage input, multi-speed), PU (digital frequency setting) and
Communication.
Outline of dancer control
• Dancer control is performed by setting "40 to 43" in
Pr.128 PID action selection
. The main speed command is the speed
command for each operation mode (External, PU, and communication). PID control is performed by the dancer roll position
detection signal, and the control result is added to the main speed command. For the main speed acceleration/deceleration
time, set the acceleration time to
Pr.44 Second acceleration/deceleration time
and the deceleration time to
Pr.45
Second deceleration time
.
NOTE
• Normally, set
Pr.7 Acceleration time
and
Pr.8 Deceleration time
to 0 s. When the
Pr.7 and Pr.8
settings are large, dancer
control response becomes slow during acceleration/deceleration.
• If an automatic restart after instantaneous power failure is activated during dancer control, E.OC[] or E.OV[] is likely to occur.
In such case, disable the automatic restart after instantaneous power failure function (
Pr.57
= "9999").
Limit
Ratio
Acceleration/deceleration
of main speed
Main speed command
*1
Dancer roll
setting point
Pr.133
Terminal 4
Potentiometer
Dancer roll position detection
PID control
PID deviation
PID feedback
PID set point
Target frequency
X14
Pr.128
= 40, 41
Pr.128
= 42, 43
Acceleration/
deceleration
+
-
Kp(1+ +Td S)
Ti S
1
Convert to 0 to 100%
M
+
+
STF
PID adding value
Main speed
ON
Output frequency
Time
Output frequency
Содержание FR-E800
Страница 17: ...16 1 Introduction 1 3 Related manuals MEMO ...
Страница 51: ...50 2 Basic Operation 2 8 I O terminal function assignment MEMO ...
Страница 89: ...88 3 Parameters 3 4 Parameter list by function group number MEMO ...
Страница 135: ...134 5 Speed Control 5 9 Troubleshooting in the speed control MEMO ...
Страница 153: ...152 6 Torque Control 6 7 Troubleshooting in torque control MEMO ...
Страница 195: ...194 8 E Environment Setting Parameters 8 18 Current average value monitor signal MEMO ...
Страница 237: ...236 10 D Operation Command and Frequency Command 10 6 Operation by multi speed setting MEMO ...
Страница 339: ...338 13 T Multi Function Input Terminal Parameters 13 9 Start signal operation selection MEMO ...
Страница 455: ...454 16 G Control Parameters 16 13 Speed smoothing control MEMO ...
Страница 481: ...480 18 Appendix 18 4 Parameters functions and instruction codes under different control methods MEMO ...