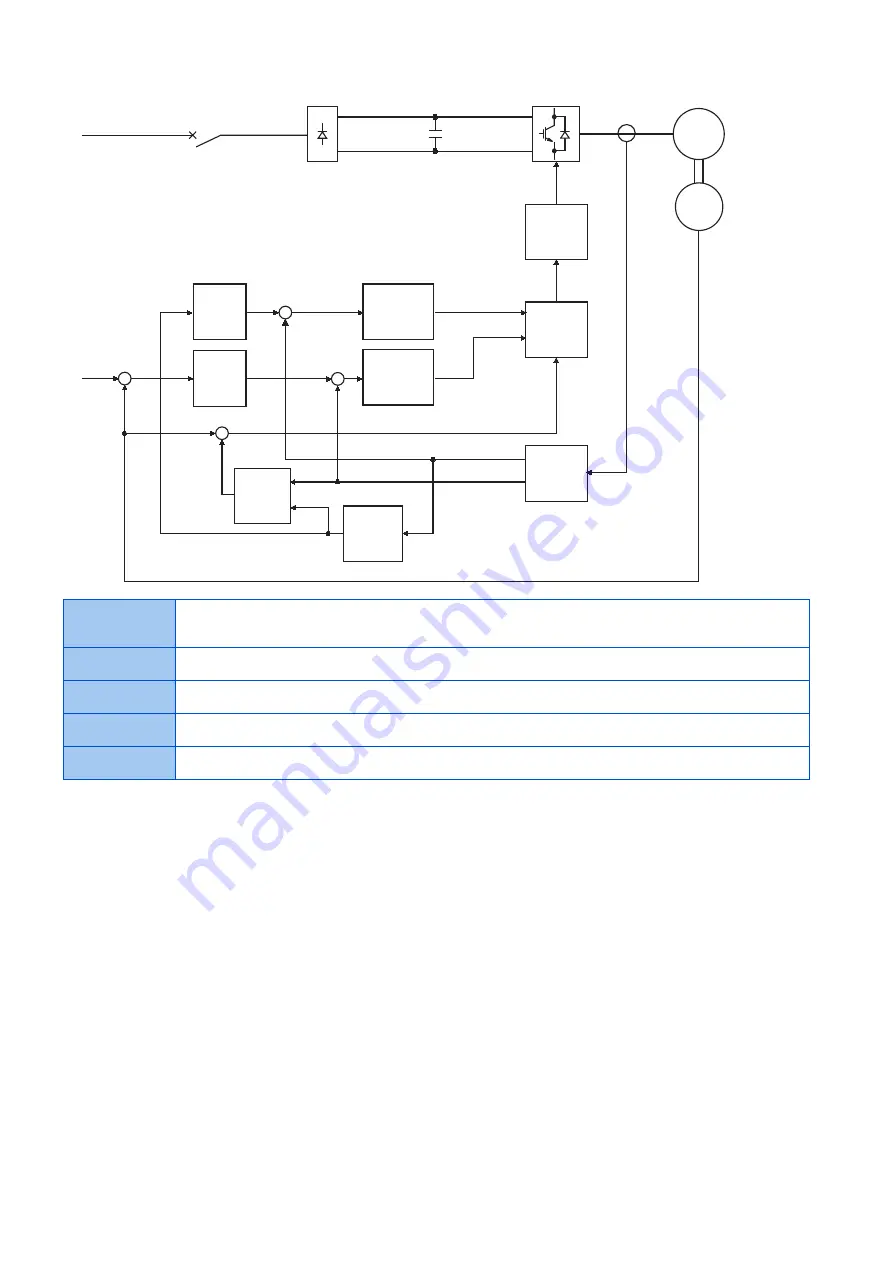
96
4. Control Method
4.1 Vector control and Real sensorless vector control
The above results are used to make PWM modulation and run the motor.
PWM
modulation
Output
voltage
conversion
Torque
current
control
Speed
control
Slip
calculation
Current
conversion
Pre-excitation
current
control
Magnetic
flux
control
Magnetic
flux
calculation
ω
ω
FB
-
+
+
-
iq
id
Vq
Vd
ω 0
ω
s
iq
φ
2
id
φ
2
id
I M
Encoder
ω
FB
+
-
iq
ω
0
+
+
iq
id
*
*
*
Block diagram of Vector control
Speed control
Speed control operation is performed to zero the difference between the speed command (
ω
*) and actual rotation value
detected by encoder (
ω
FB). At this time, the motor load is found and its result is transferred to the torque current
controller as a torque current command (iq*).
Torque current
control
A voltage (Vq) is calculated to flow a current (iq) which is identical to the torque current command (iq*) found by the
speed controller.
Magnetic flux
control
The magnetic flux (
Φ
2) of the motor is derived from the excitation current (id). The excitation current command (id*) is
calculated to use that motor magnetic flux (
Ф
2) as a predetermined magnetic flux.
Excitation current
control
A voltage (Vd) is calculated to flow a current (id) which is identical to the excitation current command (id*).
Output frequency
calculation
Motor slip (
ω
s) is calculated on the basis of the torque current value (iq) and magnetic flux (
Φ
2). The output frequency
(
ω
0) is found by adding that slip (
ω
s) to the feedback (
ω
FB) found by a feedback from the encoder.
Содержание FR-E800
Страница 17: ...16 1 Introduction 1 3 Related manuals MEMO ...
Страница 51: ...50 2 Basic Operation 2 8 I O terminal function assignment MEMO ...
Страница 89: ...88 3 Parameters 3 4 Parameter list by function group number MEMO ...
Страница 135: ...134 5 Speed Control 5 9 Troubleshooting in the speed control MEMO ...
Страница 153: ...152 6 Torque Control 6 7 Troubleshooting in torque control MEMO ...
Страница 195: ...194 8 E Environment Setting Parameters 8 18 Current average value monitor signal MEMO ...
Страница 237: ...236 10 D Operation Command and Frequency Command 10 6 Operation by multi speed setting MEMO ...
Страница 339: ...338 13 T Multi Function Input Terminal Parameters 13 9 Start signal operation selection MEMO ...
Страница 455: ...454 16 G Control Parameters 16 13 Speed smoothing control MEMO ...
Страница 481: ...480 18 Appendix 18 4 Parameters functions and instruction codes under different control methods MEMO ...