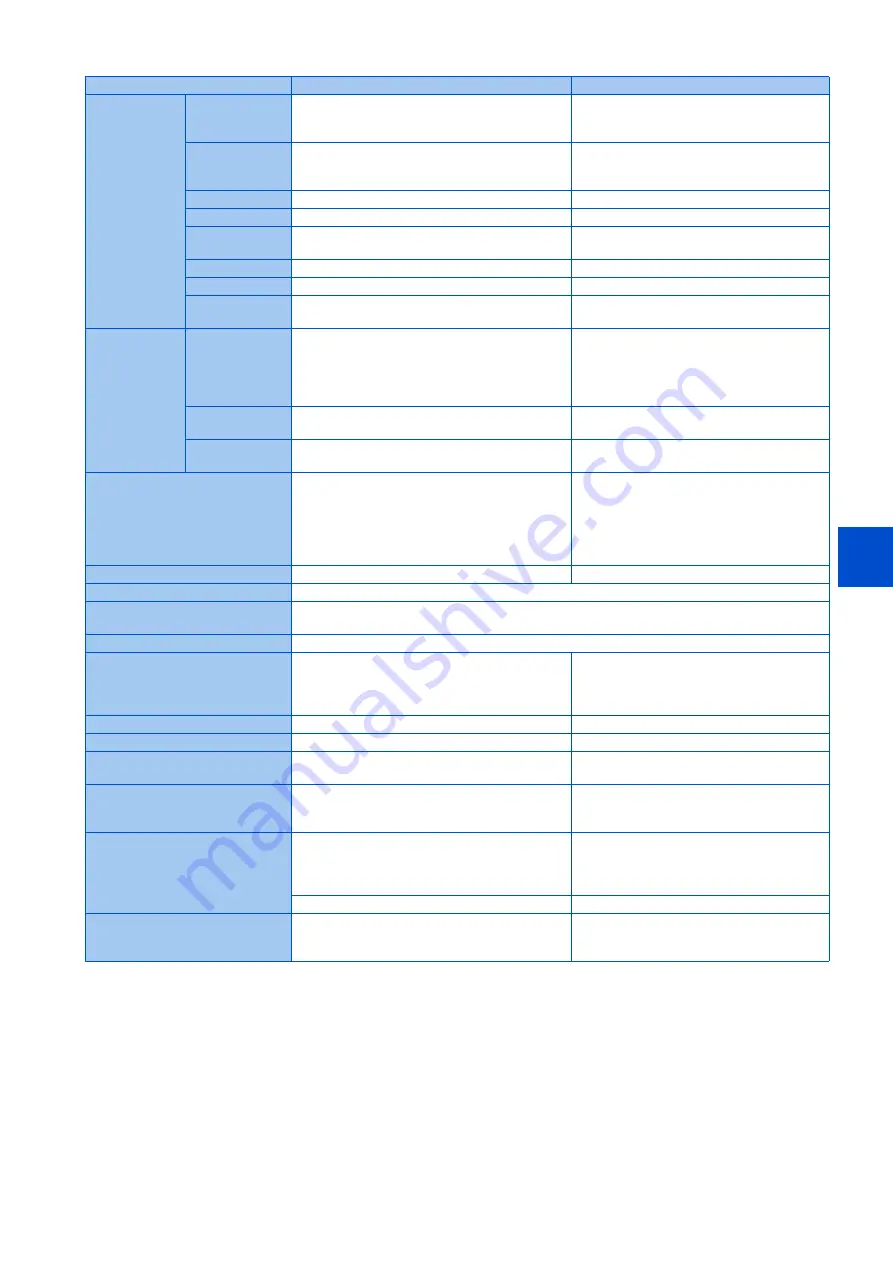
11
12
13
14
15
16
17
18
19
20
461
18. Appendix
18.1 For customers replacing the conventional model with this inverter
Installation precautions
• Removal procedure of the front cover is different. (Refer to the Instruction Manual (Connection).)
• Plug-in options of the FR-E700 series are not compatible.
Wiring instructions
• When the FR-E700 standard control circuit terminal model is replaced, the terminal block type is changed from the screw
type to the spring clamp type. Use of blade terminals is recommended.
• To use the PU connector, note that wiring methods are different. (Refer to the Instruction Manual (Connection).)
Control circuit
terminal
Shape of
terminal block
Spring clamp type
Standard control circuit terminal model: screw
type
Safety stop function model: Spring clamp type
Contact input
Standard model: 7
Ethernet model: 2
Safety communication model: 0
Standard control circuit terminal model: 7
Safety stop function model: 6
Analog input
2
2
Relay output
1
1
Open collector
output
Standard model: 2
Ethernet model and safety communication model: 0
2
Pulse output
1 (FM type only)
1 (FR-E700)
Analog output
1 (AM type only)
1 (FR-E700-NA/EC/CHT)
Safety input/
output
S1, S2, PC, SO, SOC
S1, S2, PC (safety stop function model only)
Communication
Ethernet
2 ports (Ethernet model and safety communication
model)
CC-Link IE TSN, CC-Link IE Field Network Basic,
EtherNet/IP, PROFINET, MODBUS/TCP, and
BACnet/IP
1 port (FR-E700-NE only)
CC-Link IE Field Network Basic and MODBUS/
TCP
RS-485
1 port (standard model)
Mitsubishi inverter protocol, MODBUS RTU
1 port
Mitsubishi inverter protocol, MODBUS RTU
USB
Mini B connector: USB bus power available
(Maximum SCCR: 500 mA)
Mini B connector: USB bus power unavailable
Surrounding air temperature
200/400 V class: -20°C to +60°C (Derate the rated
current when using the inverter in a temperature of
50°C or higher.)
575 V class: -10°C to +60°C (Derate the rated
current when using the inverter in a temperature of
50°C or higher.)
-10°C to +50°C
Storage temperature
-40°C to +70°C
-20°C to +65°C
Plug-in option
Dedicated plug-in options (not interchangeable)
Installation size
Compatible (Use the installation interchange attachment for replacement of the FR-E720-175(3.7K)
and FR-E740-016(0.4K) to 040(1.5K).)
Panel through attachment
Not compatible
Machine speed display
The rotation speed is displayed when
Pr.53
= "1".
The machine speed is displayed when
Pr.53
= "4".
Use
Pr.37
and
Pr.505
to set the reference for
machine speed.
The machine speed is displayed when
Pr.37
≠
"0".
Built-in potentiometer switching
Pr.146
unavailable (PA02 not supported)
Pr.146
available
Control mode selection
V/F control when "40" is set in
Pr.800
.
V/F control when "9999" is set in
Pr.80
or
Pr.81
.
MRS input selection
Use
Pr.17
to change the input specifications of the
MRS and X10 signals.
Use
Pr.17
to change the input specification of
the MRS signal.
Offline auto tuning
Set
Pr.96
= "11" to enable offline auto tuning for V/
F control (frequency search for the automatic restart
after instantaneous power failure).
Set
Pr.96
= "21" to enable offline auto tuning for
V/F control (frequency search for the automatic
restart after instantaneous power failure).
Applicable motor
Offline auto tuning is enabled regardless of the
Pr.71
setting.
Set
Pr.71
to a value whose last digit is 3 to change
the setting range of the motor constant.
Set
Pr.71
to a value whose last digit is 3 to
enable offline auto tuning.
Set
Pr.71
to a value whose last digit is 4 to read
offline auto tuning data and change the setting.
Set "10" for the constant-torque motor.
Set "1" for the constant-torque motor.
Increment/range of acceleration/
deceleration time
The setting range cannot be changed from "0 to
3600 s" even when the increment is 0.01 s (
Pr.21
=
"1").
The setting range can be changed to "0 to 360
s" when the increment is 0.01 s (
Pr.21
= "1").
Item
FR-E800
FR-E700
Содержание FR-E800
Страница 17: ...16 1 Introduction 1 3 Related manuals MEMO ...
Страница 51: ...50 2 Basic Operation 2 8 I O terminal function assignment MEMO ...
Страница 89: ...88 3 Parameters 3 4 Parameter list by function group number MEMO ...
Страница 135: ...134 5 Speed Control 5 9 Troubleshooting in the speed control MEMO ...
Страница 153: ...152 6 Torque Control 6 7 Troubleshooting in torque control MEMO ...
Страница 195: ...194 8 E Environment Setting Parameters 8 18 Current average value monitor signal MEMO ...
Страница 237: ...236 10 D Operation Command and Frequency Command 10 6 Operation by multi speed setting MEMO ...
Страница 339: ...338 13 T Multi Function Input Terminal Parameters 13 9 Start signal operation selection MEMO ...
Страница 455: ...454 16 G Control Parameters 16 13 Speed smoothing control MEMO ...
Страница 481: ...480 18 Appendix 18 4 Parameters functions and instruction codes under different control methods MEMO ...